中山电器五金加工
现在五金冲压的应用范围在不断的加大,五金加工件的需求也在不断的增多,五金加工厂的数量也随之增多,为了提升产品的竞争实力,那么五金加工过程中应该注意哪些问题呢?五金加工过程的注意事项:1.五金加工件上有划痕:零件上有划痕的主要原因是模具上有尖锐的痕迹或金属灰尘掉入模具,防止措施是磨削模具上的痕迹和清理金属灰尘。2.冲压零件底部开裂:零件底部开裂的主要原因是材料塑性差或模具压边圈压得太紧,防止措施是更换塑性好的材料或放松压边圈。3.冲压零件侧壁有皱纹:零件侧壁出现皱纹的主要原因是材料厚度不够(比较小允许厚度薄)或上部,下模安装偏心,导致一侧间隙大,另一侧间隙小。防止措施是立即更换材料并重新调整模具。五金加工件必须满足产品的使用和技术性能,便于组装和修配。中山电器五金加工
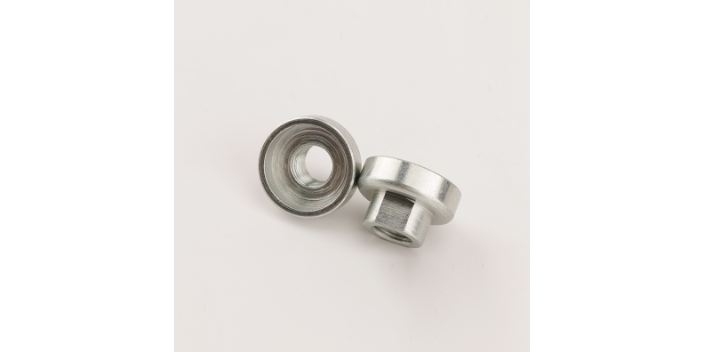
齿轮是汽车里的中心传动部件,其质量可直接影响整车的振动、噪声和可靠性。齿轮可以用CNC加工来保证齿轮的质量和精度。齿轮CNC加工顺序应按照先基面铣削,先粗后精铣,先主后次的原则进行。先加工各外圆,注意粗、精加工的分离。粗加工后进行淬火回火热处理工艺、淬火后进行精加工。各工序分开,以保证较终主表面的精细程度,使其不会受到其他表面加工时的影响。各外圆半精加工完成后开始进行齿轮齿形的粗加工。因为齿形加工比较繁重和困难,所以其加工时适当留有余量。这样可以提高定位基准,以便进行精加工。齿形精加工应安排在零件外圆的所有表面加工完成后进行,以消除齿形局部淬火引起的变形。为保证工件的精度,避免降低工件的刚性。圆柱面的加工应先加工大直径圆柱面,后加工小直径圆柱面。精密五金加工批发价数控精密五金加工的生产效率更高,数控五金加工能够同时加工多个表面。
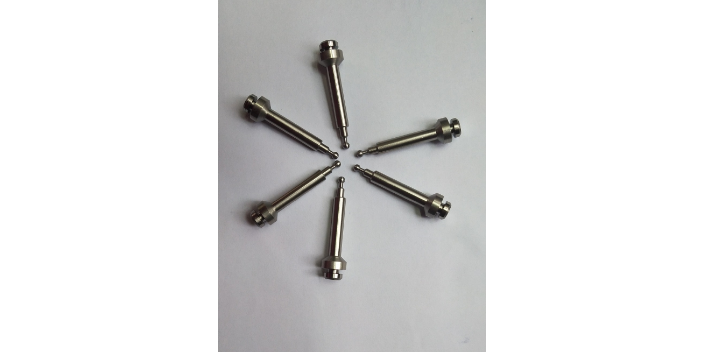
五金加工误差大且精度低的原因可能是部件受热变形:金属件加工过程中,由于不断的摩擦与强度高的运转,使得零件在生产过程中容易发生热变形,零件受热变形必然会影响零件的加工精度,这是造成零件误差的一个重要原因,在我们加工大型高精密零件时,其影响会更加明显,零件在加工过程中受多种因素影响,随着介质的不断传递,温度会逐渐上升,温度上升后会由于不停地传递热量,导致夹具.刀具和部件都会受热而产生物理反应,热积累到一定程度,会导致机床的一些部件出现热变形,影响五金机床的加工精度。
五金加工过程中出现凹凸的原因是什么?事实上,大多数是由于灰尘或铁屑附着在原材料或模具的外观上造成的,这使得产品的外观性格低下,生产率大幅下降。减少五金加工件凹凸的具体方法如下:1.拉延模的检查和修正:拉延模需要定期检查和维护,以减少五金加工件凸凹的产生,保持稳定状态。通常的做法是检查压边圈的粘合划痕和加工面(凹模圆角、凸模圆角)。2.剪切模的检查和修正:剪切过程中五金加工件凸凹的原因是剪切过程中产生铁粉,所以冲压前一定要观察铁粉,避免凸凹。车削外圆面五金加工的特点:易于保证工件各加工面的位置精度。
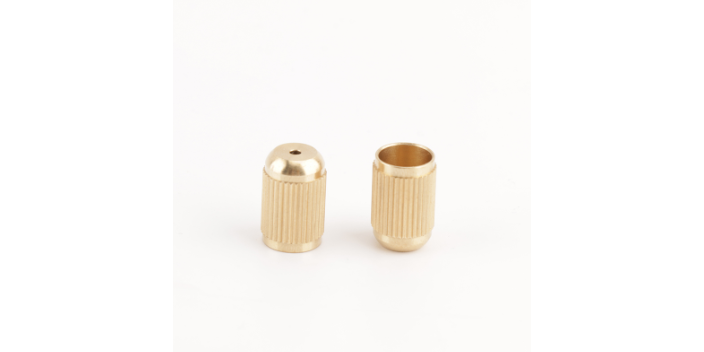
五金加工财产链各阶段的利润空间均在压缩,降价的空间减少。越来越多的企业认识到单靠价格竞争不能建立重点竞争力,不是久远发展的方向,从而努力探索新的发展道路。许多五金企业加大了技术投入,研发新的具备高技术含量的产品,将产品的差异化作为企业发展的经久之计,寻求新的市场需求,建立新的经济增长点(进入如小家电和其他相近行业),跟着竞争的深入。以实现企业的可持续发展。海内外企业的融合将进一步加快。更快地拓展国际市场,海内五金加工企业为了提高自身实力。将通过多种手段加快和国外企业的融合以提高产品质量、提高竞争力。在五金加工工艺中,精密五金件优良的冷却性能和极压耐磨性,使模具寿命和工件精度有了质的飞跃。番禺不锈钢五金加工工厂
五金加工企业主要是从事精密机械元件、设备组装以及自动化装配线的制造。中山电器五金加工
五金零件常见的一些加工工艺:1、五金:五金模具制作快速且便宜,交货时间非常短。五金可以成为内部结构部件注塑成型塑料的一个很好的替代品,因为它在设计过程的早期阶段提供了更大的灵活性,当产品可能仍会发生变化或产品的预测不明确时。2、CNC加工:CNC是加工形状复杂和公差严格的零件的经济高效的解决方案。CNC精密加工几乎可以加工出任何形状,只要旋转的切削工具可以接近材料。3、车削:车削工艺包括切削、端面、螺纹、成型、钻孔、滚花和镗孔。对于五金零件表面的加工,如果想在复杂的机器中拥有精密轴承表面,车削通常是不错的选择。中山电器五金加工
广州市白云精工五金加工厂是以提供五金机加工,小五金配件加工,电子电器五金件,精密轴类五金配件为主的股份合作企业,公司始建于1999-01-21,在全国各个地区建立了良好的商贸渠道和技术协作关系。白云精工致力于构建机械及行业设备自主创新的竞争力,产品已销往多个国家和地区,被国内外众多企业和客户所认可。
上一篇: 广州尼龙机加工件多少钱
下一篇: 东莞铜件精密五金