机加工工装铸造工艺
螺钉:也是由头部和螺杆两部分构成的一类紧固件,按用途可以分为三类:钢结构螺钉、紧定螺钉和特殊用途螺钉。机器螺钉主要用于一个紧定螺纹孔的零件,与一个带有通孔的零件之间的紧固连接,不需要螺母配合(这种连接形式称为螺钉连接,也属于可拆卸连接;也可以与螺母配合,用于两个带有通孔的零件之间的紧固连接。)紧定螺钉主要用于固定两个零件之间的相对位置。特殊用途螺钉例如有吊环螺钉等供吊装零件用.....若轴承安装在紧定套上,确定轴承座的方向。轴承座顶盖的油嘴位置应总是在紧定套螺母的另一侧。必须注意整个轴承座的方向,因为顶盖和底座须按原来的方向安装。1.轴承的安装和拆卸有时会涉及到;重物的搬动、工具和其他设备的使用或高压油的使用。2.确保环境清洁。3.检查轴颈的尺寸和形状公差。4.检查支撑面的表面粗糙度Ra不大于12.5μm。平面度公差应为IT7。对于要求较低的应用,可用IT8。精密的工装设计提高了机械设备的工作效率,减少了人工操作的误差。机加工工装铸造工艺
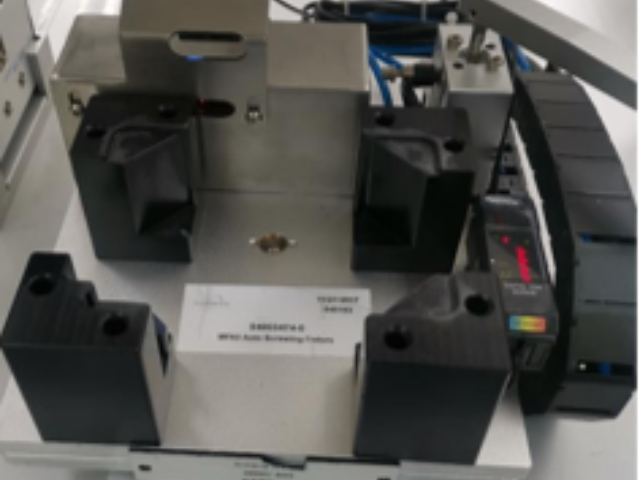
螺栓:由头部和螺杆(带有外螺纹的圆柱体)两部分组成的一类紧固件,需与螺母配合,用于紧固连接两个带有通孔的零件。这种连接形式称螺栓连接。如把螺母从螺栓上旋下,又可以使这两个零件分开,故螺栓连接是属于可拆卸连接。螺柱:没有头部的,只有两端均外带螺纹的一类紧固件。连接时,它的一端必须旋入带有内螺纹孔的零件中,另一端穿过带有通孔的零件中,然后旋上螺母, 即使这两个零件紧固连接成一整体。这种连接形式称为螺柱连接,也是属于可拆卸连接。主要用于被连接零件之一厚度较大、要求结构紧凑,或因拆卸频繁,不宜采用螺栓连接的场合。常州零件支持定制不同行业和应用领域对零件、工装、冶具的需求有所不同,需要根据具体情况进行选择和定制。
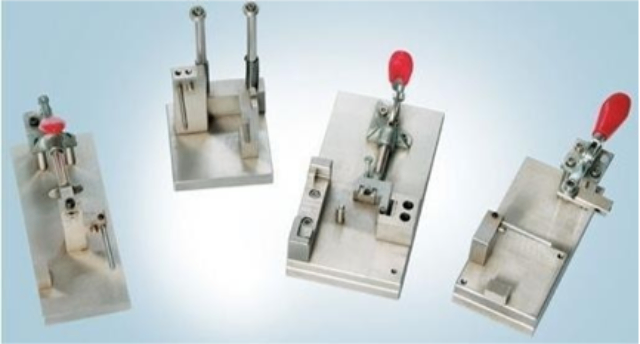
为了改善钢的性能,特意加入了一些合金元素的钢称为合金钢。碳素结构钢这类钢的含碳量一般不超过0.7%。含碳量低于0.25%的低碳钢,它的强度极限和屈服极限较低,塑性很高,且具有良好的焊接性,适于冲压、焊接,常用来制作螺钉、螺母、垫圈、轴、气门导杆和焊接构件等。含碳量在0.l%~0.2%的低碳钢还用以制作渗碳的零件,如齿轮、活塞销、链轮等。通过渗碳淬火可使零件表面硬而耐磨,心部韧而耐冲击。如果要求有更强度高和耐冲击性能时,可采用低碳含金刚。含碳量在 0.3%~0.5%的中碳钢,它的综合力学性能较好,既有较高的强度,又有一定的塑性和韧性,常用作受力较大的螺栓、螺母、键、齿轮和轴等零件。含碳量在0.55%一0.7%的高碳钢,具有高的强度和弹性,多用来制作普通的板弹簧、螺旋弹簧或钢丝绳等。
工装夹具的设计原则:1、用夹具固定产品及工具,以固定用台钳及夹持具等来固定产品及工具,以解放人手从而进行双手作业。2.使用专门使用工具,生产线中所用工装应较适合该产品及人工操作的专门使用工具以提高生产效率。3、合并二种工装为一种,减少工具的更换麻烦,以减少转拉的工时消耗,提高工作效率。生活中我们常见的红、蓝两用毛及带有橡皮的铅笔。4.提高工具设计便利性减少疲劳:(1)工具手柄方便抓握,(2)作业工具与人体动作相协调,(3)工装夹具的操作应以I的方法进行评估。产线上的工人们精心操作各种设备,将各种零件和工装加工成符合要求的成品。
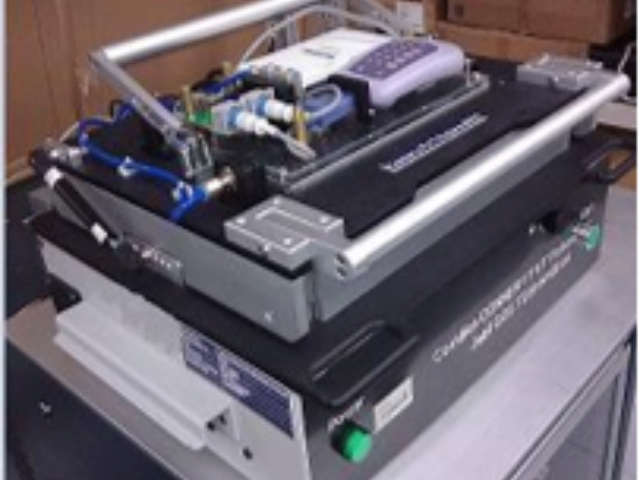
自从出现机械,就有了相应的机械零件。但作为一门学科,机械零件是从机械构造学和力学分离出来的。随着机械工业的发展,新的设计理论和方法、新材料、新工艺的出现,机械零件进入了新的发展阶段。有限元法、断裂力学、弹性流体动压润滑、优化设计、可靠性设计、计算机辅助设计(CAD)、实体建模(Pro、Ug、Solidworks等)、系统分析和设计方法学等理论,已逐渐用于机械零件的研究和设计。更好地实现多种学科的综合,实现宏观与微观相结合,探求新的原理和结构,更多地采用动态设计和精确设计,更有效地利用电子计算机,进一步发展设计理论和方法,是这一学科发展的重要趋向。自动化流水线较大程度上提高了零件的加工效率,减少了人为因素对产品质量的影响。机加工工装铸造工艺
冶具是用于热处理、铸造等工艺的工具和设备,能够改善材料的性能和质量。机加工工装铸造工艺
作为一个机械设计人员,在选材时必须了解工业发展趋势,按国家标准,结合我国资源和生产条件,从实际出发全方面考虑材料及其选择机械制造中较常用的材料是钢和铸铁,其次是有色金属合金。非金属材料如塑料、橡胶等,在机械制造中也具有独特的使用价值。铸钢,铸钢的液态流动性比铸铁差,所以用普通砂型铸造时,壁厚常不小于10mm。铸钢件的收缩率比铸铁件大,故铸钢件的圆角和不同壁厚的过渡部分均应比铸铁件大些。选择钢材时,应在满足使用要求的条件下,尽量采用价格便宜供应充分的碳素钢,必须采用合金钢时也应优先选用硅、锰、硼、钒类合金钢。机加工工装铸造工艺
上一篇: 嘉兴气密检测供应商
下一篇: 湖州电源测试系统原理