江西高精度晶圆缺陷检测光学系统
晶圆缺陷检测光学系统如何进行数据处理和分析?晶圆缺陷检测光学系统进行数据处理和分析通常分为以下几个步骤:1、图像预处理:首先对采集到的缺陷图像进行预处理,包括去除噪声、调整图像亮度和对比度等。2、特征提取:在预处理后的缺陷图像中提取特征,主要包括形状、大小、位置、灰度、纹理等等多种特征。3、数据分类:对提取到的特征进行分类,将缺陷分为不同类别。分类模型可以采用监督学习、无监督学习和半监督学习等方法。4、缺陷分析:对不同类别的缺陷进行分析,包括缺陷的生产原因、对产品性能的影响、改进产品工艺等方面。5、系统优化:通过缺陷分析反馈,不断优化晶圆缺陷检测光学系统的算法,提高检测准确率和速度。高精度、高速度、自动化程度高是晶圆缺陷检测设备的主要特点。江西高精度晶圆缺陷检测光学系统
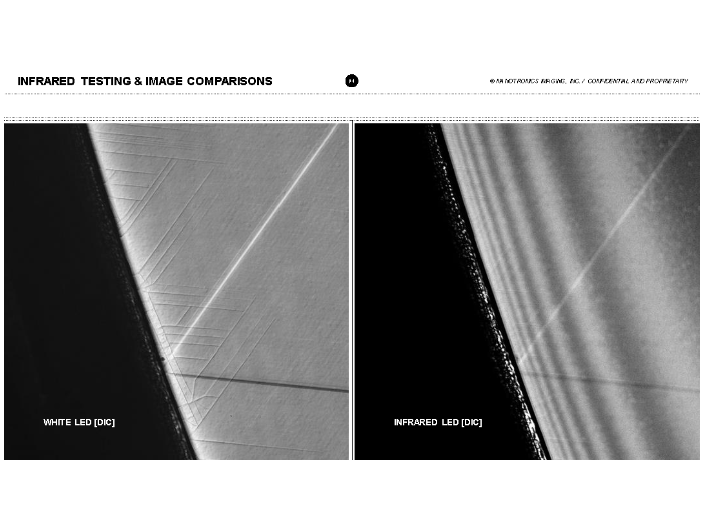
晶圆缺陷检测设备的保养对于设备的稳定性和运行效率至关重要。以下是几个保养晶圆缺陷检测设备的方法:1、定期保养:定期保养是减少机械故障的关键。通常是在生产周期结束后进行。清洁设备并检查有无维修必要,如更换气缸密封圈、更换照明灯等。2、保持干燥:由于产生静电有时会损坏设备,因此要保持适当的湿度和通风,以减少静电的产生。保持仓库或制造厂的温湿度稳定。3、清洁晶圆:晶圆是有效检测缺陷的关键,如果有灰尘或污垢附着在晶圆上,检测结果将不准确而导致不稳定的产量。因此,应该在晶圆缺陷检测之前做好晶圆的清理工作。4、保持设备干净:应该保持设备的干净,不允许有灰尘和污垢附着在设备上,影响检测准确度。应定期进行设备清洁。江西高精度晶圆缺陷检测光学系统晶圆缺陷检测设备可以通过云平台等技术进行远程监控和管理,提高生产效率和降低成本。
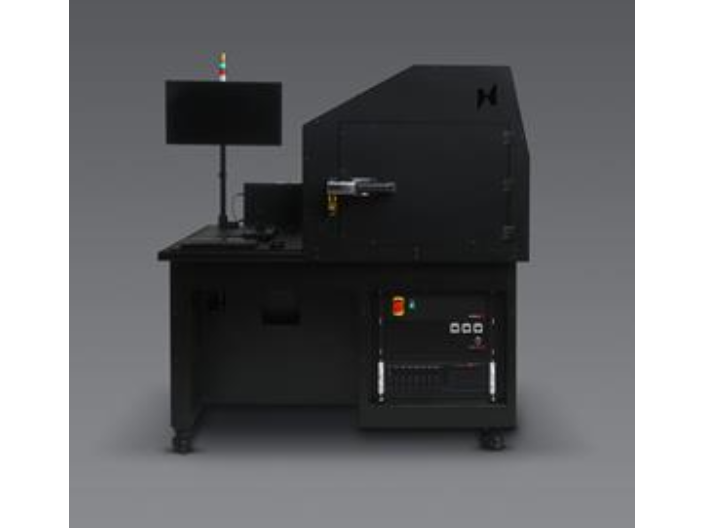
晶圆缺陷检测设备主要应用于半导体制造过程中的质量控制,包括以下几个方面:1、晶圆表面缺陷检测:检测晶圆表面的缺陷,如划痕、裂纹、污染等,以保证晶圆的质量。2、晶圆厚度测量:测量晶圆的厚度,以保证晶圆的尺寸符合要求。3、晶圆形状检测:检测晶圆的形状,如平整度、直径、圆度等,以保证晶圆的几何形状符合要求。4、晶圆材质分析:分析晶圆的材质成分,以保证晶圆的材质符合要求。5、晶圆电学性能测试:测试晶圆的电学性能,如电阻、电容、电感等,以保证晶圆的电学性能符合要求。6、晶圆光学性能测试:测试晶圆的光学性能,如透过率、反射率、折射率等,以保证晶圆的光学性能符合要求。
晶圆缺陷检测设备的优点:1、高效性:晶圆缺陷检测设备采用自动化设备进行检测,不仅检测速度快,而且可同时处理多个晶圆,提高了生产效率。2、准确性:晶圆缺陷检测设备采用多种成像技术和算法,可以精确地检测各种缺陷,并且可以判断缺陷类型、大小和位置等。3、非接触式检测:晶圆缺陷检测设备采用光学、电学和X射线等非接触式检测技术,不会对晶圆产生物理损伤。4、全方面性:晶圆缺陷检测设备可以检测多种不同种类和大小的缺陷,包括分界线、晶体缺陷、杂质、污染、裂纹等。5、可靠性:晶圆缺陷检测设备不仅可以检测缺陷情况,还可以对检测结果进行存储,便于后续生产过程中的质量控制。晶圆缺陷检测设备需要具备良好的可维护性和可升级性,以延长设备使用寿命,并适应不断变化的制造需求。
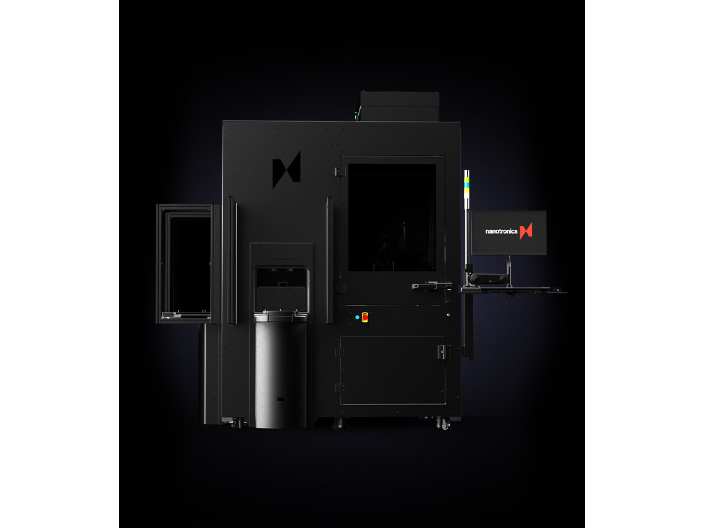
晶圆缺陷检测设备可以检测哪些类型的缺陷?晶圆缺陷检测设备可以检测以下类型的缺陷:1、晶圆表面缺陷:如划痕、污点、裂纹等。2、晶圆边缘缺陷:如裂纹、缺口、磨损等。3、晶圆内部缺陷:如晶粒缺陷、气泡、金属杂质等。4、晶圆厚度缺陷:如厚度不均匀、凹陷、涂层问题等。5、晶圆尺寸缺陷:如尺寸不符合要求、形状不规则等。6、晶圆电性缺陷:如漏电、短路、开路等。7、晶圆光学缺陷:如反射率、透过率、色差等。8、晶圆结构缺陷:如晶格缺陷、晶面偏差等。晶圆缺陷检测设备的应用范围覆盖了半导体、光电、机械等多个领域。福建多功能晶圆表面缺陷检测设备
晶圆缺陷检测设备可以对晶圆进行全方面的检测,包括表面缺陷、晶体缺陷等。江西高精度晶圆缺陷检测光学系统
晶圆缺陷检测光学系统如何确保检测结果的准确性?1、优化硬件设备:光源、透镜系统和CCD相机等硬件设备都需要经过精心设计和优化,以确保从样品表面反射回来的光信号可以尽可能地被采集和处理。2、优化算法:检测算法是晶圆缺陷检测的关键。通过采用先进的图像处理算法,如深度学习、卷积神经网络等,可以大幅提高检测系统的准确性和稳定性。3、高精度定位技术:晶圆表面的缺陷位于不同的位置和深度,因此需要采用高精度的位置定位技术,以便对不同位置和深度的缺陷进行准确检测。4、标准化测试样品:标准化测试样品是确保检测结果准确性的重要保障。通过使用已知尺寸和形状的标准化测试样品,可以验证检测系统的准确性和一致性。江西高精度晶圆缺陷检测光学系统
上一篇: 天津多功能薄膜应力分析设备怎么样
下一篇: 晶圆缺陷检测光学系统采购