东莞3CMIM工艺
材料利用率高,MIM成型是一种近净成型的工艺,其零件其外形已接近较终产品形态,资料应用率高,这一点关于贵重金属的加工损失特别具有重要意义。零件微观组织均匀、密度高、性能好,MIM是一种流体成型工艺,粘接剂的存在保证了粉末的平均排布,从而可消弭毛坯微观组织上的不平均,进而使烧结制品密度可到达其资料的理论密度。普通来说,MIM能够到达理论密度的95%~99%,高致密性可使MIM零件强度增加、韧性增强、延展性和导电导热性得到改善,磁性能进步。MIM技术能够高效制造复杂形状的金属零件,适用于高精度和高性能要求的领域。东莞3CMIM工艺
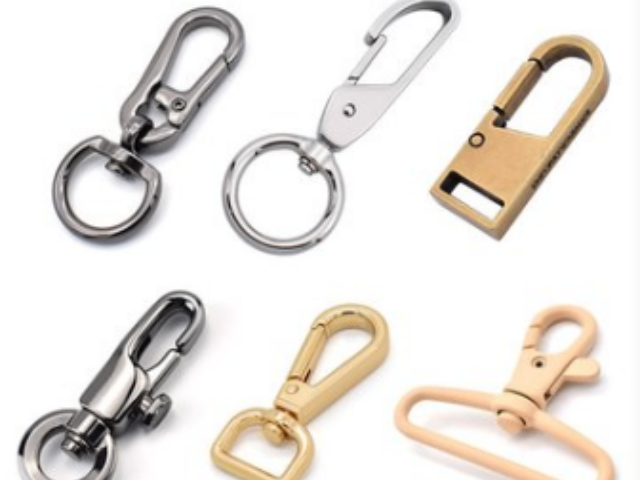
MIM技术特点:1、零部件几何形状的自由度高,能像生产塑料制品一样,一次成型生产形状复杂的金属零部件。2、MIM产品密度均匀、光洁度好,表面粗糙度可达到Ra 0.80~1.6μm,重量范围在0.1~200g。尺寸精度高(±0.1%~±0.3%),一般无需后续加工。3、适用材料范围宽,应用领域广,原材料利用率高,生产自动化程度高,工序简单,可实现连续大批量生产。4、产品质量稳定、性能可靠,制品的相对密度可达95%~99%,可进行渗碳、淬火、回火等热处理。产品强度、硬度、延伸率等力学性能高,耐磨性好,耐疲劳,组织均匀。江门焊接材料MIM制品定制MIM工艺首先将金属粉末与聚合物混合,然后注射成型,再进行脱脂和烧结等工艺步骤。
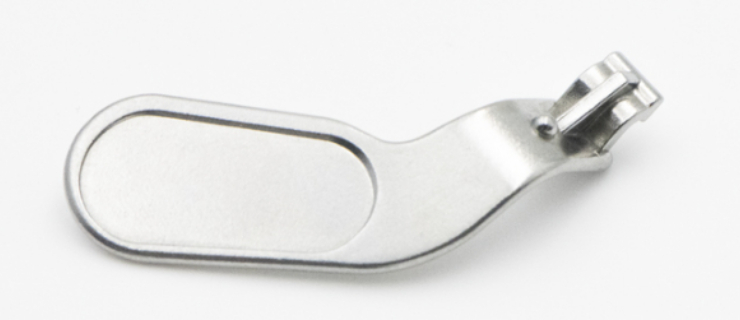
而传统粉末成型压制的零件,其密度较高只能达到理论密度的85%,这主要是由于模壁与粉末以及粉末与粉末之间的摩擦力,使得压制压力分布不均匀,也就导致了压制毛坯在微观组织上不均匀,这样就会造成压制粉末冶金件在烧结过程中收缩不均匀,因此不得不降低烧结温度以减少这种效应,从而使制品孔隙度大、材料致密性差、密度低,严重影响零件的机械性能。效率高,易于实现大批量和规模化生产,MIM使用注射机成型产品生坯,生产效率大幅度提高,适合大批量生产;同时注射成型产品的一致性、重复性好,从而为大批量和规模化工业生产提供了保证。
MIM的工艺过程。MIM工艺过程主要分为四个阶段,包括造粒、注射、脱脂和烧结,如有需要后续可以进行机加工或者拉丝、电镀等二次加工工艺。1 造粒。精细金属粉末和石蜡粘结剂、热塑性塑料按照精确比例进行混合。混合过程在一个专门的混合设备中进行,加热到一定的温度使粘结剂熔化。大部分情况使用机械进行混合,直到金属粉末颗粒均匀地涂上粘结剂冷却后,形成颗粒状(称为原料),这些颗粒能够被注入模腔。2 注射。颗粒状的原料被送入机器加热并在高压下注入模腔,通过注射成型得到生坯(green part),该过程同塑料注塑成型很类似 。模具可以设计为多腔以提高生产率,模腔尺寸设计要考虑金属部件烧结过程中产生的收缩。随着工业技术的不断更新和市场需求的发展,MIM技术将继续发展壮大,成为制造业的重要支柱之一。
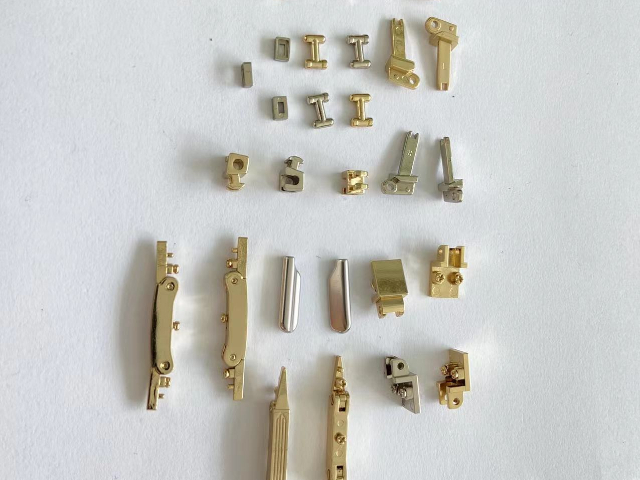
MIM产品制造过程中,原材料和工艺本身存在收缩率较大(15-18%左右)的特点。同时,MIM工艺常用于结构复杂的产品,在注射成形、脱脂、烧结工序过程中,在不同的产品设计特征和摆放方式的重力场作用双重影响下,产品在不同方向、不同结构的收缩率存在一定的差异,对尺寸管控造成一定难度。混合喂料,精细金属粉末和热塑性塑料、石蜡粘结剂按照精确比例进行混合,加热到一定的温度使粘结剂熔化,均匀地涂金属粉末颗粒上,形成原料。混合料的均匀程度直接影响其流动性,从而影响注射成型工艺参数以及较终材料的密度及其它性能。质量比例大约为90%的金属粉末与10%的粘结剂混合成均质的喂料。MIM技术的不断发展和完善将进一步推动金属粉末成型工艺的应用和发展,促进制造业的转型升级。江门焊接材料MIM制品定制
MIM工艺可实现对复杂内部结构的制造,如空心结构、内部螺纹等,提高了零件的功能性。东莞3CMIM工艺
金属注射成形 ( Metal injection Molding ,MIM ) 是一种将金属粉末与其粘结剂的增塑混合料注射于模型中的成型方法。它是先将所选粉末与粘结剂进行混合,然后将混合料进行制粒再注射成型所需要的形状。聚合物将其黏性流动的特征赋予混合料,而有助于成形、模腔填充和粉末装填的均匀性。成形以后排除粘结剂,再对脱脂坯进行烧结。有的烧结产品还可能要进行进一步致密化处理、热处理或机加工。烧结产品不只具有与塑料注射成型法所得制品一样的复杂形状和高精度,而且具有与锻件接近的物理、化学与机械性能。该工艺技术适合大批量生产小型、精密、三维形状复杂以及具有特殊性能要求的金属零部件的制造。MIM工艺流程:产品技术交流→产品设计→模具设计→模具制造;金属、陶瓷粉末、粘接剂→混炼→注射成形→脱除粘接剂→烧结→整形→检验→成品;(配料→混炼→造粒→注射成形→化学萃取→高温脱粘→烧结→后处理→成品)。东莞3CMIM工艺
上一篇: 湖南铁基精密零件价位
下一篇: 佛山非标精密零件价位