福建精益生产心得体会
如果制造企业在质量门管理中没有理顺上述问题,不能从逻辑上充分解释质量管理,也不能在实际操作中保证严格执行,而只是笼统地说“我们在使用质量门工具”,那么结果往往是质量门没有起到应有的作用,质量问题在工位甚至车间之间还是不断溢出。因此,精益要素需要以详细的流程和定制化的管理机制作为保障。企业需要在每个流程中载明每一步涉及哪些人员、每个人员的职责是什么、流程每个节点的交付成果是什么、每个流程环节的要求时间是多少、决策的升级机制是什么、每个人员在该流程中如何接受考核、对人员的能力有哪些要求等等。由日本丰田公司首先推出的,在生产组织、管理方面的一种好方式。福建精益生产心得体会
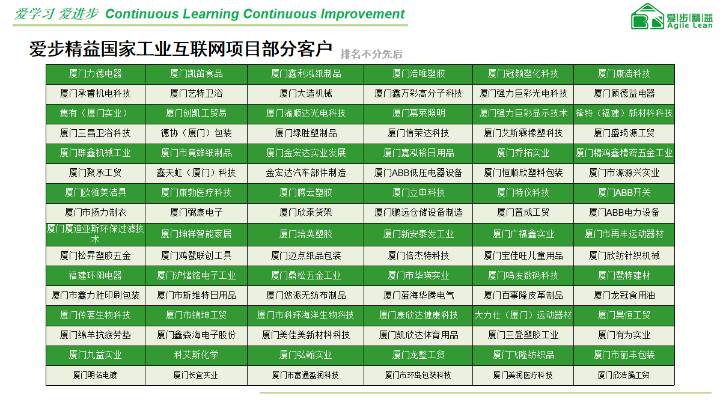
流程标准化
流程标准化是企业运营和管理的重要手段,它通过对流程进行定义、图绘制、规范、文档、执行、监控、优化以及培训和支持等环节,提高企业运营效率,降低成本,提升企业竞争力。
流程定义1.对企业的业务流程进行明确,确定哪些流程需要标准化。2.针对每个需要标准化的流程,明确其输入、输出、关键步骤和关键绩效指标。
流程图绘制1.使用流程图绘制工具,将每个需要标准化的流程绘制成流程图。2.确保流程图清晰、简洁,易于理解和操作。
流程规范1.对每个需要标准化的流程,制定详细的流程规范。2.确保流程规范涵盖了所有关键步骤和操作细节。
流程执行1.对员工进行培训,确保他们了解并掌握每个需要标准化的流程。2.鼓励员工在实际工作中按照流程规范和文档执行流程。3.对员工在执行过程中遇到的问题进行及时解答和指导。
流程监控
流程优化
培训和支持1.对员工进行持续的培训和教育,提高他们对需要标准化的流程的理解和掌握能力。2.提供必要的支持和资源,帮助员工更好地执行和优化需要标准化的流程。3.对员工的培训和支持效果进行评估和反馈,持续改进和提升培训效果和质量。 揭阳爱步精益精益生产流程标准化员工改善量小、持续性差。
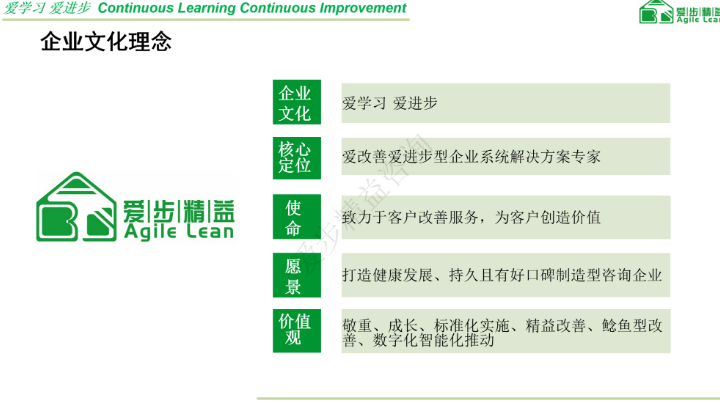
七大浪费之一运输浪费表现:人员走动过多;需要专门运输来实现工序间的衔接;过多的运输。原因:低效的车间布局、过于庞大的设备、不流畅的生产等。对策:杜绝孤岛式生产,合理紧凑安排工序,让作业流动起来,形成节拍,从而无需过多运输!
七大浪费之二动作浪费表现:作业动作不连贯、幅度过大、转身角度大、弯腰、动作重复或多余等形成浪费。危害:动作浪费对生产效率、质量以及人员安全都会造成负面影响。对策:从人机工程学角度,合理运用工业工程手法来进行作业台布局优化以及作业动作标准化。
七大浪费之三加工浪费表现:加工余量过大、无谓的加工精度、多余的产品功能、重复检验包装等。原因:自以为是的作业,而不是以客户价值为导向。对策:用省略、替代、重组或合并的方法审视现有工序;准确把握客户需求、优化作业标准以及工序间的衔接。
企业管理咨询现场通常是指咨询师与企业管理层和员工进行深入的沟通和合作,以便更好地了解企业的情况和问题,并制定出适合企业的解决方案。以下是企业管理咨询现场的一些典型场景:1.企业管理层会议:咨询师与企业管理层进行会议,了解企业的战略规划、组织结构、流程和人力资源管理等方面的情况,并提出建议和解决方案。2.现场观察和调研:咨询师到企业现场进行观察和调研,了解企业的生产流程、员工工作环境、设备设施等方面的情况,并提出改进建议。3.员工访谈和调查:咨询师与企业员工进行访谈和调查,了解员工的工作情况、工作满意度、工作压力等方面的情况,并提出改进建议。4.数据分析和报告撰写:咨询师对企业的数据进行分析,撰写报告,提出改进建议和解决方案。5.培训和指导:咨询师对企业员工进行培训和指导,帮助员工提高工作效率和工作质量,提高企业的生产效率和经济效益。以上是企业管理咨询现场的一些典型场景,咨询师需要根据企业的具体情况和问题,制定出适合企业的解决方案,并与企业管理层和员工进行深入的沟通和合作,以便更好地实施解决方案。应用于各个行业和领域。它可以帮助企业提高生产效率、降低成本、提高产品质量,并实现持续改进和创新。
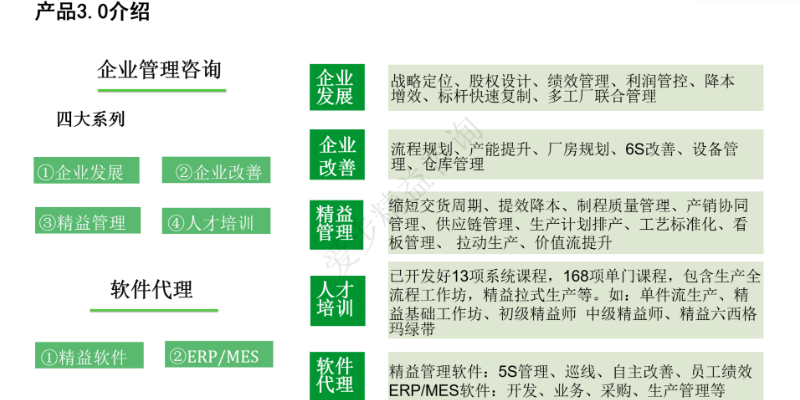
1、拉式生产(pullproduction)后工序根据前工序的需求来加工一定数量的产品,一个工序衔接一个工序的需求,这样就形成了拉式生产方式。为了有效便捷地传递需求,一般通过看板手段,即在看板上标明需求量及现有量等信息,后工序可根据看板信息进行生产。2、准时化生产(JustInTime)3、自働化(Jidoka)4、浪费(Muda)5、防呆法(Poka-yoke)6、快速换模(SMED)7、节拍时间(TAKTtime)8、价值流图(VSM)9、精益屋10、改善(Kaizen)人等料、料等人的现象大幅减少。福州爱步精益精益生产企业发展
降低成本:精益生产管理能够提高仓库使用率,通过减少存储产品来降低仓库管理的成本。福建精益生产心得体会
1、定义/识别价值精益实践的关键出发点是价值,而价值只能由客户来确定。而提供错误的产品或服务是一种“浪费”。请注意,“精益”不是制造系统的目标,“价值”才是制造系统的目标,客户的价值认知和我们的成本与努力无关。我们要以客户价值认知作为精益的起点,形成决定性竞争优势,作为发展制造系统的目标。如果“目标”错误,后续发展的制造系统会是一项“浪费”。很多情况,竞争对手未察觉产业或运营模式问题,而检视业界造成客户的问题,是识别决定性竞争优势的起点。福建精益生产心得体会
上一篇: 阳江现场标准化内容
下一篇: 惠州爱步精益咨询精益生产流程标准化