机器外壳厚板吸塑定制
怎么样去设计厚板吸塑产品:1. 通过模具的分析,我们可以清楚明白产品的成型过程,在这个过程中,要出现一定的拔模角度(3度),表面要一定的圆角(R>3.5),侧面可以出现一定的行位、碰穿. 装配位(boss柱、卡扣)不适合,怎么样实现装配位:1):转接件粘接;2):转接件锁螺丝,精度不是很好,需做定位治具,对于精度特别高的,无法实现,一般大部分的反插骨可以通过这种方法去实现。2. 这种产品的实现有点类似于钣金的冲压和拉伸(缺少加热系统),拉伸的过程相当于吸塑加热的过程;跟碳纤维的热压工艺也类似。厚片吸塑可以替代传统式的手工制做,具备生产工艺流程优良,速度更快,质量可靠等优势。机器外壳厚板吸塑定制

厚片吸塑工艺介绍,原理和流程:厚片吸塑(Thermoforming)是一种将热塑性塑料材料加热至塑性状态,再通过负压和正压将其吸附在模具上,冷却成型的工艺。具体流程如下:1. 选材。吸塑材料通常为热塑性塑料片材,如ABS、PC、PMMA等。选择材料需要根据产品的使用环境、功能和成本等因素考虑。2. 制模。根据产品的设计图纸制作母模和子模,通常由铝合金、复合材料或铜制成,并采用CNC加工工艺进行修整和抛光。3. 加热和成型。将塑料片材放置在吸塑机的加热炉中,加热至塑性状态,然后通过负压和正压将其吸附在模具上,冷却成型,待脱模后得到产品。4. 切割和后处理。根据产品的尺寸和形状进行切割,并进行表面处理、涂装和装配等工艺。吉林厚板吸塑供应商厚板吸塑加工工艺,是将定位好的板材通过烘箱加热到软化的状态。
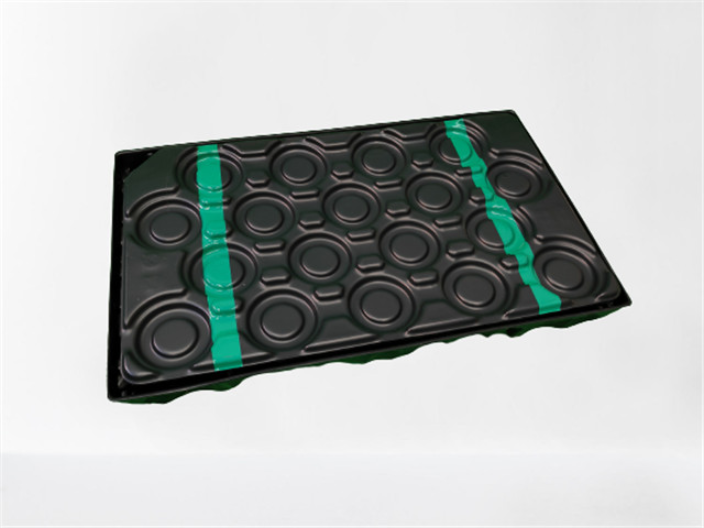
展望未来:航空航天制造中厚片吸塑的未来,随着材料科学和数字技术的进步,厚片吸塑在航空航天制造领域的前景广阔。 新型高性能塑料的推出将扩大厚片吸塑的应用范围,从而能够生产更复杂、更强度高的部件。人工智能、物联网和机器人等工业4.0技术将进一步提高厚片吸塑的精度和效率,实现更加灵活和响应迅速的生产、实时监控和预测性维护。驾驭监管环境,航空航天业的制造商在严格监管的环境中运营。 安全至关重要,任何组件——无论是结构、功能还是美观——都必须满足严格的安全和质量标准。
在下一节中,我们将更深入地探讨模具设计的高级方面,包括排气、公差和现代技术的作用。通过了解这些基本原理,设计师和制造商可以确保他们的厚片吸塑项目不只可行,而且经过优化以获得较佳结果。通风和浇口,模具设计中一个关键但经常被忽视的方面是排气和浇注系统。 这些是模具中的通道或孔,可让空气逸出并均匀分布真空。 通风口位置不正确可能会导致光洁度不佳,甚至成型不完全。门控是指真空所遵循的路径。 精心设计的浇口可确保真空的均匀性,这对于在整个成型件中实现一致的厚度至关重要。 通风口和浇口的放置是一个细致的过程,会对较终产品产生相当大的影响。厚板吸塑用途分类:运动教学器材产品外壳吸塑、美容活动器材使用外壳吸塑、医疗服务器械公司外壳吸塑。
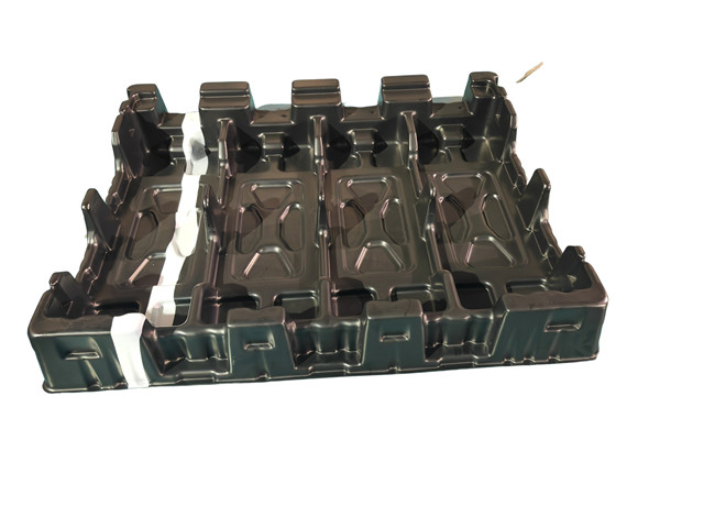
特殊厚片吸塑厚度为0.14-8.0mm,主要是采用PVC、PP、PS、HIPS、PET(包括APET和PETG)、ABS、PC、PE和PMMA等各种材质与效果的注塑类型吸塑制品。厚片吸塑主要产品有冰箱内胆、广告灯箱、商品展示架、宠物笼底盘、背投电视后壳和各种机械面板等。厚片吸塑产品的成型工艺主要是通过专门使用的吸塑成型机来完成的,这其中还分为自动化和人工两种不同的操作方式。自动化成型特别适合大批量产品的生产加工,因为它从原料到成品整个过程都实现了自动化操作,所以效率是很高的,而且质量也比较稳定。厚片吸塑成型产品主要有厚板吸塑、厚壁吸塑、亚克力吸塑、PMMA吸塑等。机器外壳厚板吸塑定制
厚板吸塑智能化生产线,实现生产过程实时监控,提升产品质量。机器外壳厚板吸塑定制
厚片吸塑在医疗器械制造中的优势:材料多样性,厚片吸塑可使用多种材料,其中许多材料非常适合医疗应用。 这些材料的范围从高抗冲聚苯乙烯和 ABS(丙烯腈丁二烯苯乙烯)到各种等级的医用品质 PVC(聚氯乙烯)和 PETG(聚对苯二甲酸乙二醇酯)。 制造商可以根据设备的要求选择材料,包括耐用性、耐化学性、耐温性和生物相容性。速度和效率,厚片吸塑可实现快速原型设计和生产,从而缩短医疗设备的上市时间。 它还可以在成型过程中集成安装点和固定件等功能,从而消除二次操作并节省时间。机器外壳厚板吸塑定制
上一篇: 托盘式围板箱厂家批发
下一篇: 安徽PE双层厚片吸塑工艺