产线治具铸造工艺
常用机械零件包括:轴、轴承、联轴器、离合器、键、销等。轴是机械中的重要零件,其功用是支承转动零件及传递运动和动力:而将轴和轴上零件进行周向固定并传递转矩的零件是键;轴承是文承轴及轴上零件,保持轴的旋转精度和减少轴与支承间的摩擦和磨损:联轴器和离合器是联接不同机构中的两根轴,使它们一起回转并传递转矩。轴一般是实心轴,有特殊要求时也可制成空心轴,如航空发动机的主轴,除了刚性轴外,还有钢丝软轴(挠性轴)挠性轴是刚度很小,可以自由弯曲的轴,也称软轴挠性轴用于连接不在同一轴线和不在同一方向或有相对运动的两轴,以传递旋转运动和扭矩。可以把回转运动灵活地传到不开敞地空间位置。POM是一种常用的工程塑料材料,具有优良的机械性能和耐磨性。产线治具铸造工艺
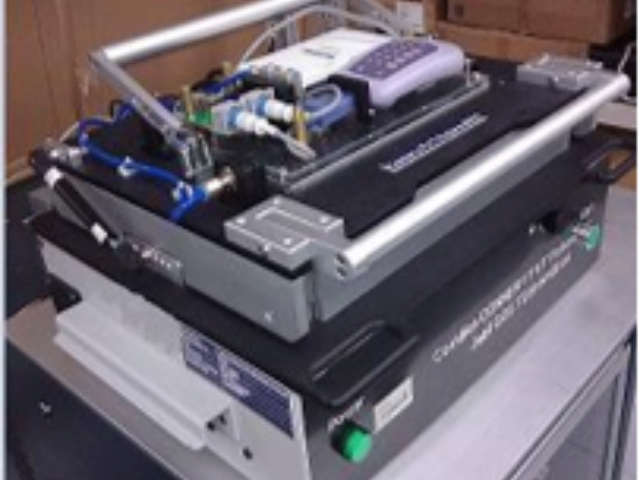
夹具通常由定位元件(确定工件在夹具中的准确位置)、夹紧装置、对刀引导元件(确定刀具与工件的相对位置或导引刀具方向)、分度装置(使工件在一次安装中能完成数个工位的加工,有回转分度装置和直线移动分度装置两类)连接元件以及夹详细(夹具底座)等组成。机床导轨的选材,机床导轨的精度对整个机床的精度有很大的影响。必须防止其变形和磨损,所以机床导轨通常都是选用灰口铸铁制造,如HT200和HT350等。灰口铸铁在润滑条件下耐磨性较好,但抗磨粒磨损能力较差。为了提高耐磨性,可以对导轨表面进行淬火处理。数控零件定制设计电子设备的主要部件需要精密零件支撑,这些零件在自动化流水线上经过严格测试后出厂。
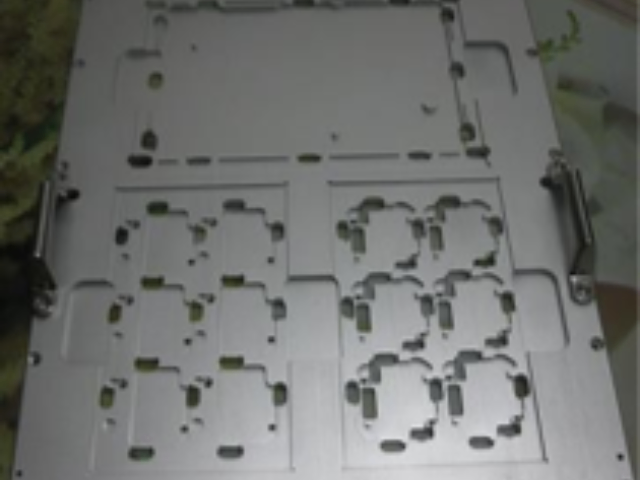
在特殊工况下,必须对润滑剂提出如下特殊要求:1、长寿命的要求 要求润滑剂的使用寿命特别长。2、无害性的要求;3、耐低温的要求 要求能耐—63℃以下的低温。4、低摩擦力矩的要求 要求润滑剂的摩擦阻力很低。5、边界润滑特性好的要求;6、耐高温的要求 要求能耐250℃以上的高温。7、耐高真空的要求 要求在高真空的条件下,不挥发,不散失,不变质,特别是在失重状态的高真空条件下。机械零件(machine element)又称机械元件(machine part)是构成机械的基本元件,是组成机械和机器的不可分拆的单个制件。机械零件既是研究和设计各种设备中机械基础件的一门学科,也是零件和部件的泛称。研究和设计各种设备中机械基础件的一门学科,也是零件和部件的泛称。
作为一门学科,机械零件从机械设计的整体出发,综合运用各有关学科的成果,研究各种基础件的原理、结构、特点、应用、失效形式、承载能力和设计程序;研究设计基础件的理论、方法和准则,并由此建立了本学科的结合实际的理论体系,成为研究和设计机械的重要基础。自从出现机械,就有了相应的机械零件。但作为一门学科,机械零件是从机械构造学和力学分离出来的。随着机械工业的发展,新的设计理论和方法、新材料、新工艺的出现,机械零件进入了新的发展阶段。有限元法、断裂力学、弹性流体动压润滑、优化设计、可靠性设计、计算机辅助设计(CAD)、实体建模(Pro、Ug、Solidworks等)、系统分析和设计方法学等理论,已逐渐用于机械零件的研究和设计。更好地实现多种学科的综合,实现宏观与微观相结合,探求新的原理和结构,更多地采用动态设计和精确设计,更有效地利用电子计算机,进一步发展设计理论和方法,是这一学科发展的重要趋向。波峰焊工艺中,工装的设计至关重要,它确保了零件焊接的稳固与精确。
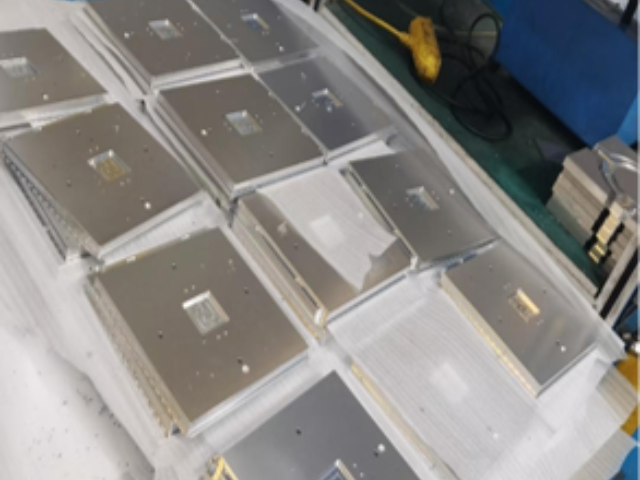
玻纤板波峰焊治具具有平整度好、表面光滑、无凹坑、耐热性、耐潮性、阻燃等优点,常用于电气、电子等行业绝缘结构零部件的生产。铝波峰焊治具则具有良好的传热性能和较高的机械强度,可以耐受高温和化学腐蚀,通常用于特殊环境下的生产。由于电子产品的小型化、轻量化推动了电子元件从插件元件向贴片元件转化,但还是有部分插件元件存在各种因素的制约,无法转化成贴片元件,所以混装电路板会一直存在。关于混装电路板的焊接,不论是波峰焊还是手工焊接,都存在效率低的问题,所以选择使用合适的波峰焊治具,则尤为重要。烧录是将数据或程序写入芯片中的过程,常用于电子产品的制造。CNC治具
精密加工需要使用高精度的机床和工具,以确保零件的尺寸和形状的精确度。产线治具铸造工艺
在通常情况下,机械零件尺寸公差要求越小,机械零件的表面粗糙度值也越小,但是它们之间又不存在固定的函数关系。例如一些机器、仪器上的手柄、手轮以及卫生设备、食品机械上的某些机械零件的修饰表面,它们的表面要求加工得很光滑即表面粗糙度要求很高,但其尺寸公差要求却很低。在一般情况下,有尺寸公差要求的零件,其公差等级与表面粗糙度数值之间还是有一定的对应关系的。在一些机械零件设计手册和机械制造专著中,对机械零件的表面粗糙度和机械零件的尺寸公差关系的经验及计算公式都有很多介绍,并列表供读者选用,但只要细心阅来,就会发现,虽然采取完全相同的经验计算公式,但所列表中的数值也不尽相同,有的还有很大的差异。这就给不熟悉这方面情况的人带来了迷惑。同时也增加了他们在机械零件工作中选择表面粗糙度的困难。产线治具铸造工艺