多轴联动数控铣床操作流程
数控系统小型化便于将机、电装置结合为一体。目前主要采用超大规模集成元件、多层印刷电路板,采用三维安装方法,使电子元器件得以高密度安装,较大规模缩小系统的占有空间。而利用新型的彩色液晶薄型显示器替代传统的阴极射线管,将使数控操作系统进一步小型化。这样可以方便地将它安装在机床设备上,更便于对数控机床的操作使用。数控机床的可靠性一直是用户较关心的主要指标。数控系统将采用更高集成度的电路芯片,利用大规模或超大规模的专业用及混合式集成电路,以减少元器件的数量,来提高可靠性。通过硬件功能软件化,以适应各种控制功能的要求。数控铣床可以实现多种加工形式的自动化,如自动送料、自动夹紧等,提高生产效率。多轴联动数控铣床操作流程
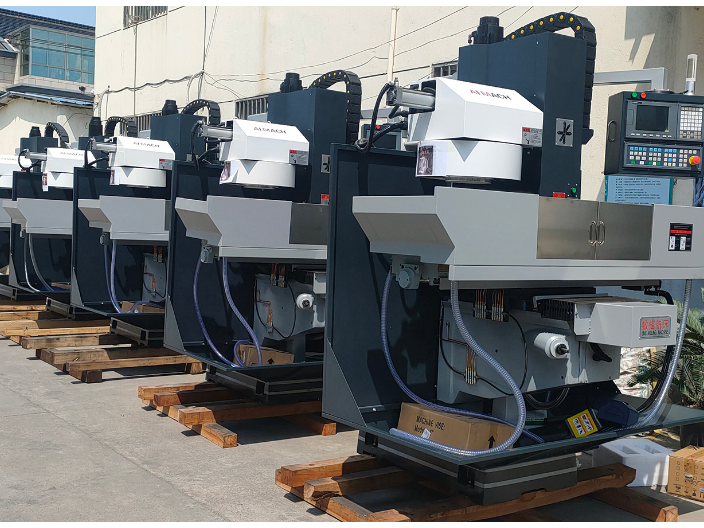
现代数控机床将引进自适应控制技术,根据切削条件的变化,自动调节工作参数,使加工过程中能保持较佳工作状态,从而得到较高的加工精度和较小的表面粗糙度,同时也能提高刀具的使用寿命和设备的生产效率。具有自诊断、自修复功能,在整个工作状态中,系统随时对CNC系统本身以及与其相连的各种设备进行自诊断、检查。一旦出现故障时,立即采用停机等措施,并进行故障报警,提示发生故障的部位、原因等。还可以自动使故障模块脱机,而接通备用模块,以确保无人化工作环境的要求。为实现更高的故障诊断要求,其发展趋势是采用人工智能诊断系统。成都智能数控铣床报价数控铣床一直把铣削加工作为要点。
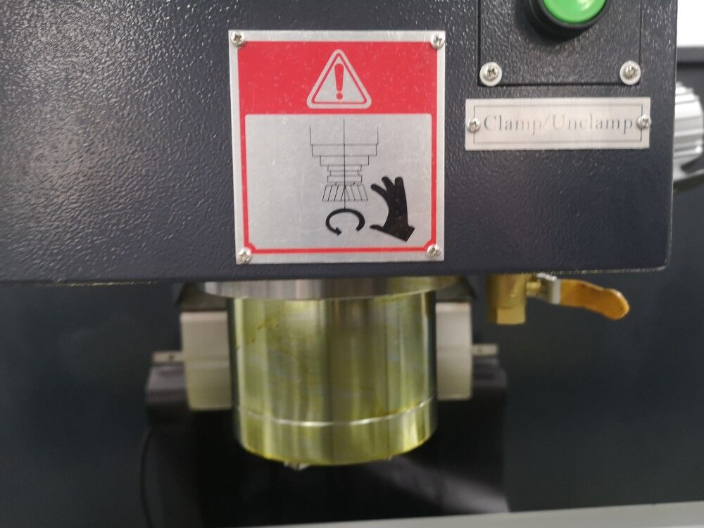
高速高精度并不只是指数控铣床对工件的加工速度要高要快,出厂的商品精度更高,并且也要求数控机床在工件加工的全部过程中都要高速工作、准确定位,以削减工件在准备、加工、转运、收储等各个环节占用的时间,归纳提高工厂的出厂效率,降低出厂成本。更高精度的机械商品在实际使用中会带来更多的益处,如削减工作过程中的冲击和发热,降低能源损耗,使整机工作愈加平稳牢靠,降低机床损坏的概率等等。机械加工更趋向于高精度、多种类、小批量、低成本、短周期和杂乱化的加工,复合加工是数控铣床的一个主要技能开展方向。
我国经济发展速度放缓,工业增长的乏力给整个加工中心行业产生了重大影响,现代社会,加工中心行业产能过剩所带来的负面效应开始显现。下一阶段行业将通过兼并重组吸收掉一批小厂家、淘汰一批落后企业、转移一批加工中心到国外、提高产品质量。这样既解决了产能过剩问题,又提高了加工中心行业整体水平。市场的低迷也给加工中心企业带来了转型的机遇,企业应将主要精力由销售产品转移到提高产品的质量上来,重新设定产品线,制定发展战略,淘汰掉落后的产品,多研发盈利能力强的加工中心,为市场回暖做好准备。数控铣床具有良好的适应性,能够适应不同材料和加工要求的加工任务。
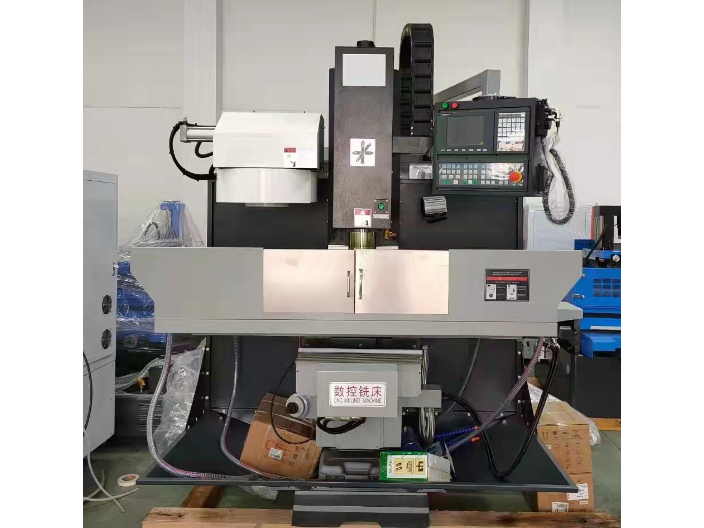
数控铣床在加工过程中实现高效润滑可以采取以下措施:1.选择合适的润滑剂:根据加工材料和工艺要求,选择适合的润滑剂。常用的润滑剂包括液体润滑剂和固体润滑剂。液体润滑剂可以提供良好的润滑效果,而固体润滑剂则可以减少磨损和摩擦。2.控制润滑剂的供给量:通过调整润滑剂的供给量,可以确保在加工过程中始终保持适当的润滑状态。过多的润滑剂可能会导致加工表面过度润滑,而过少的润滑剂则可能会导致加工表面磨损。3.定期清洁和更换润滑剂:定期清洁数控铣床的润滑系统,以确保润滑剂的质量和性能。同时,根据使用情况和润滑剂的寿命,及时更换润滑剂,以保证其有效性。4.使用高质量的润滑剂:选择高质量的润滑剂可以提供更好的润滑效果,并且能够减少加工过程中的摩擦和磨损。5.优化加工参数:通过调整加工参数,如切削速度、进给速度和切削深度等,可以减少加工过程中的摩擦和磨损,从而提高润滑效果。总之,通过选择合适的润滑剂、控制供给量、定期清洁和更换润滑剂、使用高质量的润滑剂以及优化加工参数,可以实现数控铣床在加工过程中的高效润滑。数控铣床在铣削带凸肩的平面时选用,一般不用于纯平面加工。多轴联动数控铣床操作流程
数控铣床可以进行多种形状的加工,如直线、曲线、圆弧等,满足不同产品的设计要求。多轴联动数控铣床操作流程
何为经济型数控铣床?经济型数控铣床在很多客户眼中或许只是便宜的数控铣床的代名词,但是实际上我们所说的经济型数控铣床更多时候指的是小型数控铣床。小型数控铣床是数控铣床中行程较小的数控铣床的统称,一般都是850以下的数控铣床,也有部分人把数控铣床也归纳为小型数控铣床,但是这些方面都是见仁见智的。小型数控铣床都可以被称为经济型数控铣床。很多客户认为小型数控铣床性能不好,其实并非如此。人们对小型数控铣床总是会存在这样的误区,因其行程小,不合适加工较大的工件,就认为小型数控铣床功能不强。但是事实上小型数控铣床是专门用于加工小型零件的铣床,和大型的数控铣床相比,两者的定位是不一样的,其实没办法去比较。多轴联动数控铣床操作流程
上一篇: 湖南单柱式加工中心报价
下一篇: 杭州单柱式加工中心价格多少