五金精密压铸
模具中的其它部件包括型芯滑板等。型芯是用来在铸件上开孔或开口的部件,它们也能用来增加铸件的细节。型芯主要有三种:固定、活动以及松散型。固定型芯的方向同铸件脱出模具的方向平行,它们要么是固定的,要么长久性地连接在模具上。可动型芯可以布置在除了脱出方向以外的任何方向上,铸件凝固后打开模具之前,必须利用分离装置把活动型芯从模腔内拿出。滑块和活动型芯很接近,比较大的区别在于滑块可以用来制造倒凹表面。在压铸中使用型芯和滑块会大幅增加成本。松散型芯也被称作取出块,可以用来制造复杂的表面,例如螺纹孔。在每个循环开始之前,需要先手动安装滑块,然后再同铸件一起被推出。然后再取出松散型芯。松散型芯是价格比较昂贵的型芯,因为制造它需要大量劳动,而且它会增加循环时间。每一精密压铸,都是精密压铸技术的结晶。五金精密压铸
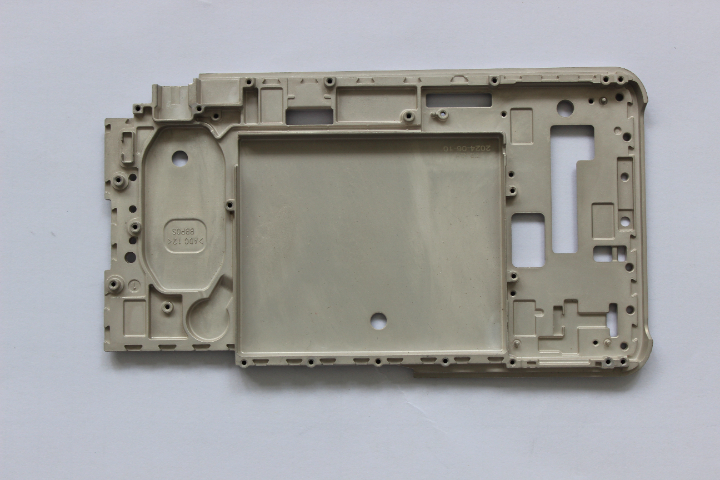
压铸工艺的不断创新也推动了精密压铸的应用范围的扩大。例如,无孔压铸工艺和直接注射工艺等改进型压铸技术能够减少铸造缺陷并增加成品率。这些技术的应用使得精密压铸在制造高精度、高质量产品方面具有更大的优势。此外,随着新材料的不断涌现和制造技术的不断进步,精密压铸的应用领域也将不断拓展。精密压铸的质量直接影响到产品的性能和寿命。因此,在精密压铸的生产过程中需要严格控制各个环节的质量。首先,需要选用高质量的原材料和模具材料,确保精密压铸的质量和性能。其次,需要制定合理的生产工艺参数和操作规程,确保压铸过程的稳定性和可控性。此外,还需要对精密压铸进行严格的检测和质量控制,确保每件产品都符合标准要求。苏州通信配件精密压铸公司压铸工艺精湛,产品精度高。
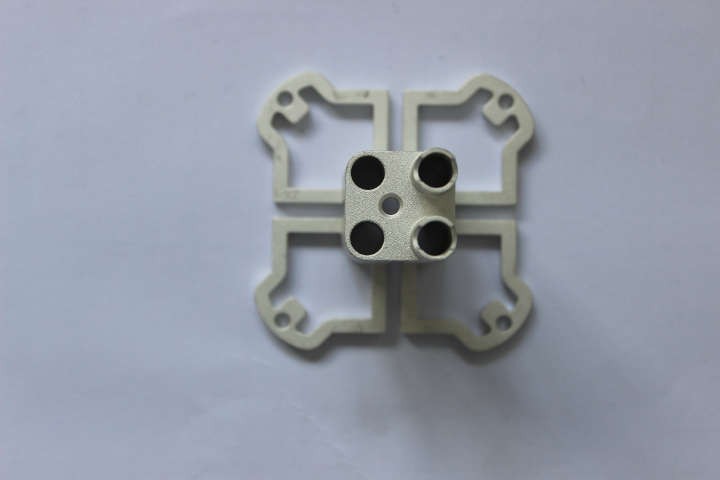
当压铸无法用于热室压铸工艺的金属时可以采用冷室压铸,包括铝、镁、铜以及含铝量较高的锌合金。在这种工艺中,需要在一个独自的坩埚中先把金属熔化掉。然后一定数量的熔融金属被转移到一个未被加热的注射室或注射嘴中。通过液压或者机械压力,这些金属被注入模具之中。由于需要把熔融金属转移进冷室,这种工艺比较大的缺点是循环时间很长。冷室压铸机还有立式与卧式之分,立式压铸机通常为小型机器,而卧式压铸机则具有各种型号。模具是经过特别设计的,当打开模具后铸件会留在活动部分内。这样活动部分的推杆就会把铸件给推出去,推杆通常是通过压板驱动的,它会准确地用同样大小的力量同时驱动所有的推杆,这样才能保证铸件不被损坏。
精密压铸的尺寸稳定性对于其使用性能至关重要。在压铸过程中,由于熔融金属的温度和压力变化以及模具的磨损等因素,可能导致铸件的尺寸发生变化。为了确保铸件的尺寸稳定性,需要采取一系列措施,如使用高精度的测量工具对模具进行定期检测和调整、控制熔融金属的温度和压力等参数、采用合适的模具材料和热处理工艺等。精密压铸具有普遍的应用领域,如汽车、电子、家电、通讯等行业。在汽车行业中,精密压铸常用于制造发动机零部件、底盘零部件等;在电子行业中,精密压铸常用于制造连接器、散热器等;在家电行业中,精密压铸常用于制造空调压缩机零部件、洗衣机零部件等。随着科技的不断进步和市场的不断扩大,精密压铸的应用领域也在不断拓展和深化。精密压铸,展现金属之美。
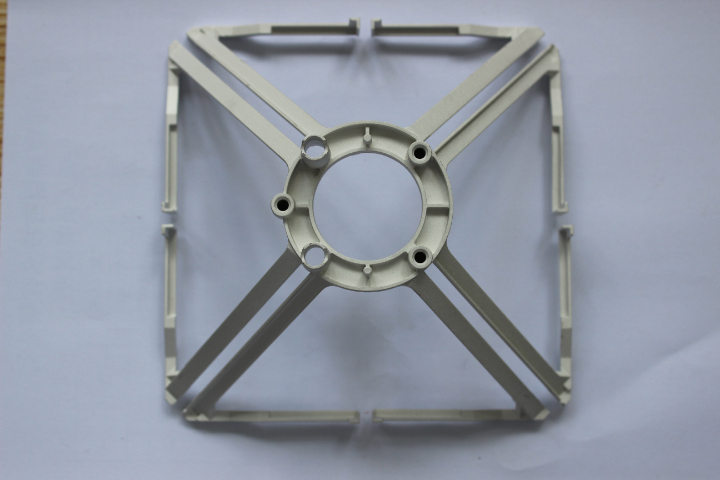
传统压铸工艺主要由四个步骤组成,或者称做高压压铸。这四个步骤包括模具准备、填充、注射以及落砂,它们也是各种改良版压铸工艺的基础。在准备过程中需要向模腔内喷上润滑剂,润滑剂除了可以帮助控制模具的温度之外还可以有助于铸件脱模。然后就可以关闭模具,用高压将熔融金属注射进模具内,这个压力范围大约在10到175兆帕之间。当熔融金属填充完毕后,压力就会一直保持直到铸件凝固。然后推杆就会推出所有的铸件,由于一个模具内可能会有多个模腔,所以每次铸造过程中可能会产生多个铸件。落砂的过程则需要分离残渣,包括造模口、流道、浇口以及飞边。这个过程通常是通过一个特别的修整模具挤精密压铸来完成的。其它的落砂方法包括锯和打磨。如果浇口比较易碎,可以直接摔打铸件,这样可以节省人力。多余的造模口可以在熔化后重复使用。通常的产量大约为67%。精确控制,铸就完美精密压铸。苏州通信配件精密压铸公司
严格把控品质,精密压铸值得信赖。五金精密压铸
精密压铸的制造过程体现了现代工业技术的精湛与高效。从熔融金属的注入到模具的闭合,再到高压下的成型,每一步都需要严格的操作和控制。精密压铸的高精度不只体现在其形状和尺寸上,更体现在其内部结构的致密性和均匀性上。这种精密铸造的特性使得精密压铸在承受复杂载荷和恶劣环境时,能够保持稳定的性能。此外,精密压铸还具有良好的可加工性和可焊接性,便于后续的加工和组装。精密压铸在汽车工业中的应用尤为普遍。汽车轮毂、发动机支架、传动系统部件等关键部位,都离不开精密压铸的支撑。压铸铝合金轮毂以其轻量化、高的强度、耐腐蚀等优点,成为现代汽车的重要部件。精密压铸的高精度和稳定性,保证了汽车行驶的安全性和舒适性。同时,精密压铸的批量生产也降低了汽车制造成本,提高了生产效率。五金精密压铸
上一篇: 笔记本支架压铸模具制造
下一篇: 深圳汽车压铸件技术要求