安徽机械设备铜基板厂
铜是一种常用的导热性能优良的金属,因此在许多应用中被用作热导体。铜的热导率是指单位厚度的铜材料在单位温度梯度下通过单位面积的热量传导速率。铜的热导率通常约为 385 W/(m·K)。这意味着在铜制基板中,热量可以相对迅速而高效地传导。铜基板的高热导率使其在电子设备、散热器和其他需要有效散热的应用中得到普遍应用。热导率的高低直接影响了材料的散热性能,铜由于其优异的导热特性而被普遍选择。在实际应用中,了解材料的热导率对设计高效的散热系统至关重要。选择合适的材料来实现所需的散热效果,可以提高设备的性能和可靠性。铜基板的表面处理可改善其防氧化性。安徽机械设备铜基板厂
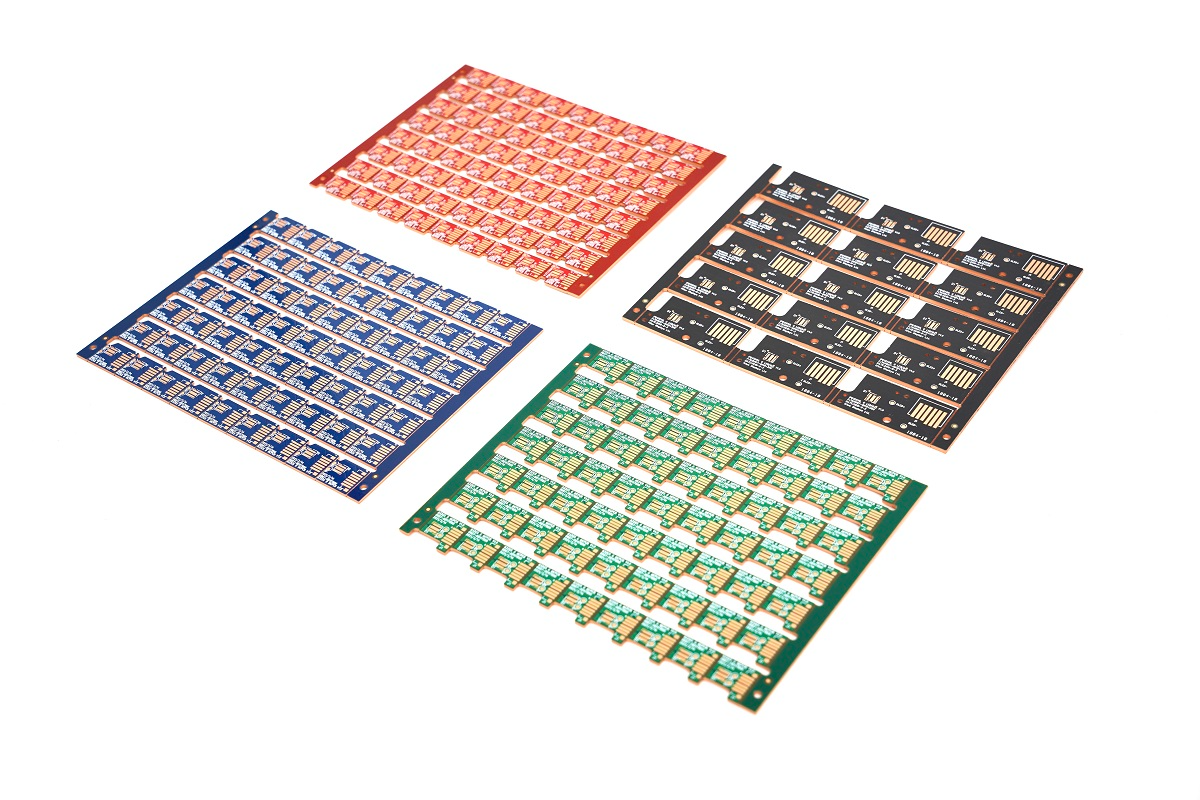
铜基板的尺寸标准通常根据具体的应用和制造要求而有所不同。一般情况下,铜基板的尺寸会根据所需的电子元件大小、散热需求、电路复杂度等因素进行设计。在电子制造行业中,常见的标准尺寸通常包括:常见尺寸:一般常见的铜基板尺寸为4x4英寸(101.6x101.6毫米)、8x8英寸(203.2x203.2毫米)等。厚度:铜基板的厚度常见的有0.8mm、1.0mm、1.2mm等。不同厚度的铜基板在散热性能、强度等方面有所不同。形状:除了常见的正方形尺寸外,铜基板的形状也可以是长方形、圆形、异形等,取决于具体的设计要求。定制尺寸:对于某些特殊应用,需要需要定制尺寸的铜基板,这些尺寸会根据具体的设计要求进行制定。因此,铜基板的尺寸标准并非固定不变,而是根据具体应用的需求和制造工艺的要求而定制的。在实际应用中,你可以根据自己的需求选择合适的尺寸和厚度。需要注意的是,不同厂家生产的铜基板规格需要稍有差异,建议在选购时与供应商确认具体的尺寸标准。广东PCB铜基板单价铜基板的表面平整度对于电路板的性能和可靠性至关重要。
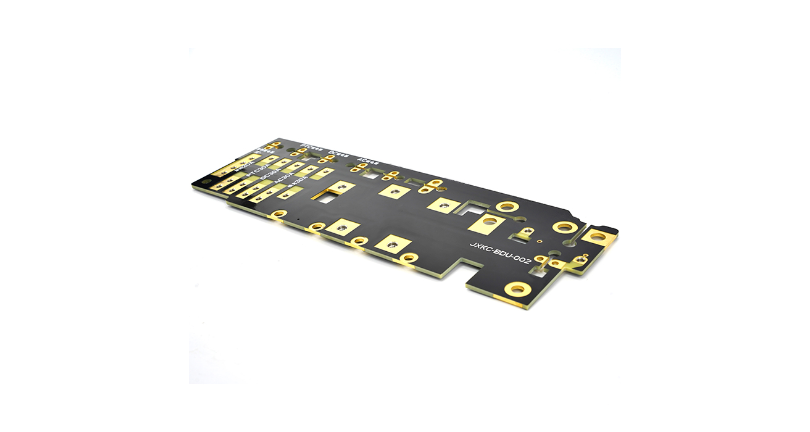
铜基板的塑形工艺主要是指在电路板制造过程中对铜基板进行加工和成型的工艺流程。以下是铜基板的常见塑形工艺步骤:切割(Cutting):首先,根据设计要求,将原始铜基板切割成所需尺寸的小块或小片。打孔(Drilling):在铜基板上打孔,用于安装元件或连接导线。通常使用数控钻床进行精确的孔位加工。蚀刻(Etching):将铜基板放入腐蚀剂或蚀刻液中,蚀刻掉不需要的铜箔,保留下电路图案。成型(Forming):铜基板需要需要根据特定的形状和要求进行成型。成型可以通过热压、机械压制或钳工等方法实现。折弯(Bending):根据设计要求,有时需要在铜基板上进行折弯,以满足特定的结构要求或连接要求。
铜基板的表面氧化对其电性能有着重要的影响,主要表现在以下几个方面:电阻增加: 铜基板表面的氧化会增加表面电阻,导致电流传输过程中产生更大的电阻,从而降低了电子器件的导电性能。接触电阻增加: 表面氧化会增加铜基板与其他器件或连接物之间的接触电阻,影响信号传输的稳定性和可靠性。焊接困难: 表面氧化会降低铜基板与其他元件的焊接质量,增加焊接难度,同时也需要降低焊接接触的可靠性。热散失增加: 表面氧化会影响铜基板的热传导性能,降低散热效率,导致器件工作温度升高,影响器件的性能和寿命。信号传输损耗增加: 表面氧化会增加信号在铜基板表面的传输损耗,降低信号传输的质量和速率。铜基板的表面光洁度对印刷电路板的制造至关重要。
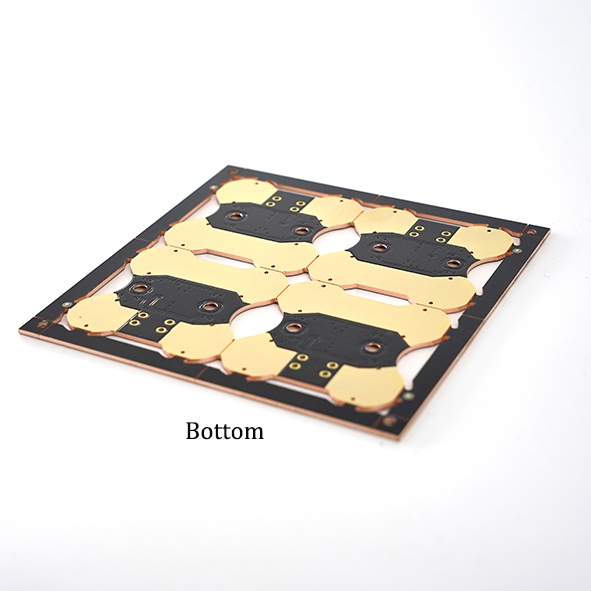
铜基板的热膨胀性能对焊接质量具有重要影响,主要有以下几点:匹配性:焊接时使用的焊料和基板的热膨胀系数应该尽需要匹配,以避免由于热胀冷缩不匹配而导致焊点周围产生应力。如果热膨胀系数不匹配,焊点区域需要会出现裂纹或焊接点受力不均,影响焊接接头的可靠性和稳定性。热应力:当焊接材料冷却时,基板和焊料会因为温度变化而发生不同程度的收缩或膨胀,这会引起焊接点周围的热应力。如果基板的热膨胀系数与焊料的系数差异太大,需要会导致焊点区域的破裂或变形,影响焊接质量。热传导性能:铜基板通常具有良好的热传导性能,这有助于快速散热并避免焊接过程中局部温度过高。高热传导性有助于保持焊点周围温度均匀,减少热应力的积累。对铜基板进行特定的防腐蚀处理有助于延长其寿命。河北单面热电分离铜基板厂家
铜基板上的焊接技术影响整个电路板的稳定性。安徽机械设备铜基板厂
铜基板通常具有较高的压弯性能,这使得它在许多应用中成为理想的选择。以下是关于铜基板压弯性能的几个重要方面:强度:铜基板通常具有良好的强度,可以经受一定程度的压力和弯曲而不会容易变形或破裂。柔韧性:铜具有相对良好的柔韧性,使得它能够在适量的应变下保持稳定性,不易产生裂纹或断裂。成形性:铜基板可以相对容易地被加工成各种形状,这使得在制造过程中可以针对不同的需求进行弯曲、切割等操作。回弹性:与一些其他材料相比,铜在经历一定程度的压弯后通常具有较好的回弹性,可以恢复到较接近初始状态的形状。安徽机械设备铜基板厂
上一篇: 广州四层热电分离铜基板报价
下一篇: 山东铝基板厂商