深圳PCBA贴片厂WMS系统功能
为了应对这些挑战,半导体制造企业正在积极探索和实施制造执行系统(MES),以提高生产效率、质量管理和资源利用效率。本文将详细介绍半导体制造企业为什么需要实施MES系统,MES系统的应用方式、应用工艺流程、具体应用场景以及为半导体企业带来的价值。MES系统简介,MES,即制造执行系统(Manufacturing Execution System),是一种集成了计划、监控和管理制造过程的计算机化系统。它在生产过程中的各个阶段都提供了实时数据和信息,帮助企业管理和优化生产活动。对于半导体制造企业,MES系统具有关键意义,因为它们通常面临复杂的工艺和高度精密的生产环境。MES系统可以帮助半导体企业实现生产过程的自动化。深圳PCBA贴片厂WMS系统功能
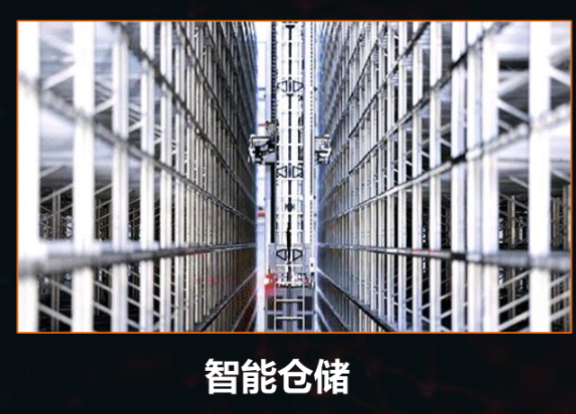
仓储系统WMS直接对接企业ERP系统,打通了不同工艺流程之间物质流和信息流,生产物流数据及产品批号全流程可追溯,实现物流数据与业务数据的流通,使从生产线至仓储线之间运营数据 无缝流转。1、实现 入库、盘货、出库、包装、码垛等环节的动态均衡。2、仓储系统WMS直接对接企业ERP系统,实现物流数据与业务数据的流通。3、用全程皮带线直接运输,所有运动都是靠皮带线动力而运动,不存在磨损风险。我们认为,对于生产制造业来说,仓库是资金聚集中心尤为重要,WMS系统可通过不同的维度来提升与优化企业仓库,比如货物进出情况不够详细、是否有存货、出错率高等问题都在不断出现,WMS系统根据其特性能够实时显示并更新仓库的情况,每一种货物的进出记录都会有详细的记录。湖南芯片设计公司WMS系统开发商WMS 在供应链中的应用,只有在仓库流程允许的情况下,供应链才能快速、准确和高效地运行。
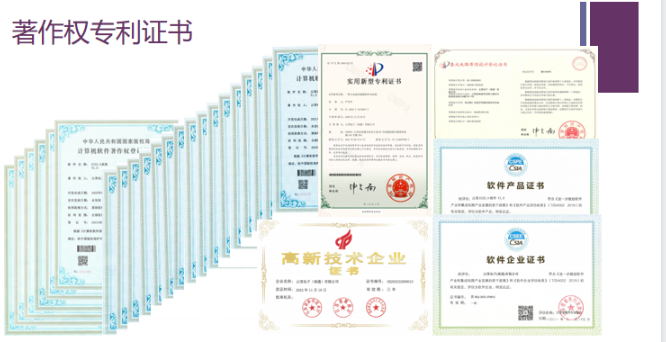
芯片、半导体行业MES系统应用介绍,北京天思天心助力企业信息化,智慧化,可视化,数字化,半导体制造工艺流程较为复杂,专业性要求较高,因此拥有一套与企业情况相匹配的、具有扩展性、可靠性的MES的生产控制管理系统显得尤为重要。如今随着5G技术的应用发展,通过利用该技术实施MES系统的优化改造,使得移动EMS系统成为可能,这对于推动半导体生产企业实现可持续发展具有重要的意义。MES系统与半导体制造行业,MES系统属于一种制造执行管理系统,是企业实施敏捷制造战略与实现车间生产敏捷化的一种重要的技术手段。
WMS模板为仓库管理提供了一系列强大的功能,包括了来料管理、拣配管理、成品管理和日常管理等方面。来料管理:采购订单:通过系统生成采购订单,记录需要采购的订单、数量、价格等信息。能够实现采购需求的计划和控制,方便订单采购的跟踪和管理。供应商发货单:当供应商将货物送达仓库时,系统可记录发货单信息,包括发货日期、数量、质量状态等。实现供应链中库存流动的可追溯性。采购收货收货单:在收到货时,系统可生成收货单,记录实际到货情况,同时支持收货单的生成和管理,以应对可能出现的质量问题或供需变化。MES系统可以帮助企业创建和管理工单,确保生产按照计划进行。
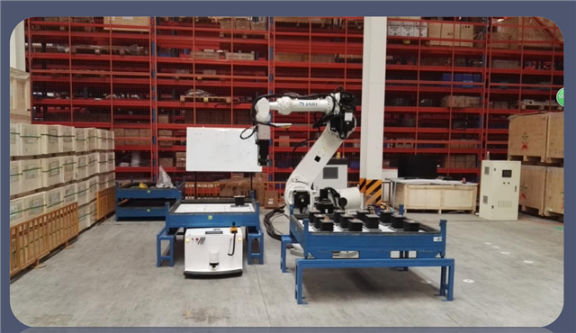
WMS的类型有哪些?下面我们来介绍仓库管理软件有多种类型和实施方法,类型通常取决于组织的规模和性质。它们可以是单独的系统,也可以是更大的ERP系统或供应链执行套件中的模块。WMS的复杂性也可能有很大差异。一些小型组织可能使用一系列简单的硬拷贝文档或电子表格文件,但大多数大型组织(从中小型企业(SMB)到企业公司)都使用复杂的WMS软件。某些WMS设置是专门为组织规模而设计的,许多供应商都有可扩展到不同组织规模的WMS产品WMS 通过管理从接收原材料到运输成品的订单履行流程,在供应链管理中发挥着至关重要的作用。湖南芯片设计公司WMS系统开发商
MES系统可以帮助半导体厂商实现全方面的生产过程管理,从而提高产品的一致性和稳定性。深圳PCBA贴片厂WMS系统功能
半导体制造精细化程度较高,流程较为复杂,要确保上千道工序中的人、机、料、法、环协同顺畅不是件易事。在这个过程中,就需要MES这样的制造软件,像一个“超级大脑”般指挥和控制着从晶圆在不同设备间流转,完成近千道工序,到封装测试的全过程。半导体行业MES解决方案,云茂电子作为在制造软件领域积淀深厚的企业,基于对半导体行业的深刻洞察和研究,打造出有针对性的半导体行业MES解决方案。直击生产调度统筹难、现场信息反馈难、设备运行监控难、生产过程不透明等诸多痛点,围绕计划排程、工艺流程管理、质量管控、在制品管理、设备管理、生产技术管理、掩膜晶舟管理、数据统计分析、工程数据采集等方向,构建柔性高效的生产模式,实现生产、计划、设备、人员的高度调配,减少成品的返工率和废品率,从而降低生产成本及周期,提高生产效率及质量。深圳PCBA贴片厂WMS系统功能
上一篇: 山东IPM封装定制
下一篇: 福建PCBA板特种封装方式