原料药中间体萃取塔答疑解惑
江苏正分科技有限公司是一家专业的转盘萃取塔,涡轮萃取塔,填料萃取塔等设备的生产厂家,提供高性能的产品和优惠的价格.我们致力于为客户提供质优的服务,让您的生产更加高效,稳定,专业从事连续化化工设备研发、设计、生产和销售的高科技企业。目前主要产品有连续化混合设备、精馏塔、分子蒸馏、萃取塔(转盘萃取塔,涡轮萃取塔,填料萃取塔)、缠绕式换热器、压力容器以及其它定制类化工设备。公司主要服务于精细化工(医药、农药、化工中间体、原料药)、石油化工、湿法冶金、发酵、环保等领域,公司拥有专业的研发、销售、生产、售前和售后服务团队。 较于传统的分离方法减少了很多极端繁琐的过程,降低了能源的使用,也减小了环境污染。原料药中间体萃取塔答疑解惑
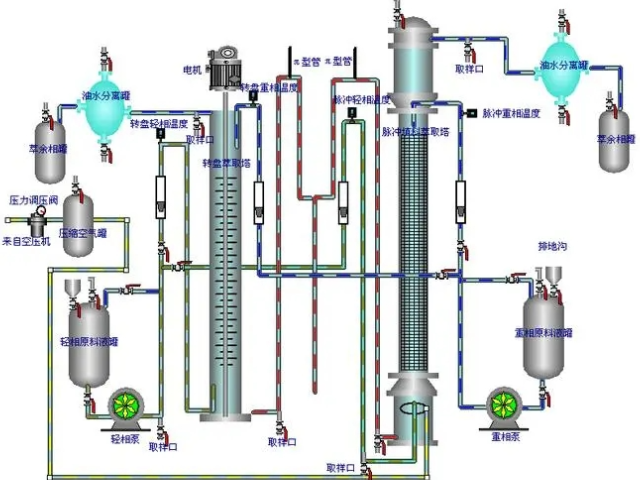
萃取塔是一种液-液质量传递设备,广泛应用于化学工业、石油炼制和环境保护等领域。在这种设备中,混合物溶液中的一种或几种化合物组分被另一种液体(称为溶剂)提取出来,以实现分离、富集和提纯的目的。为了保持萃取塔内溶液的温度,通常会使用电伴热保温。电伴热系统是一种有效的加热方法主要利用电能转化为热能来提高管道或设备内流体的温度,以维持流体在工艺操作所需的温度范围内。在萃取塔中,电伴热系统主要用于以下几个方面:1.改善传热效果:通过提高萃取塔内流体的温度,电伴热系统可以增加传热面积,提高传热效率从而加速萃取过程。2.提高分离效率:适当的温度可以提高萃取塔的分离效率通过电伴热系统,可以将萃取塔的内部温度控制在更佳分离条件下从而实现更好的分离效果。3.防止结晶和固化:在某些工艺操作中萃取塔内可能会出现结晶或固化的物质。电伴热系统可以防止这种情况发生保持萃取塔内流体的流动性降低能耗:相比传统的蒸汽加热或热水加热方法电伴热系统可以更有效地利用电能,降低能源消耗和运行成本。江苏正分科技是一家专业从事于连续化化工设备研发、设计、生产和销售的一体化高科技企业,致力于为客户提供连续化化工设备解决方案。 DMAC连续逆流萃取萃取塔设备连续萃取塔连续萃取塔采用持续不断的萃取方式,适合于大规模工业化生产。
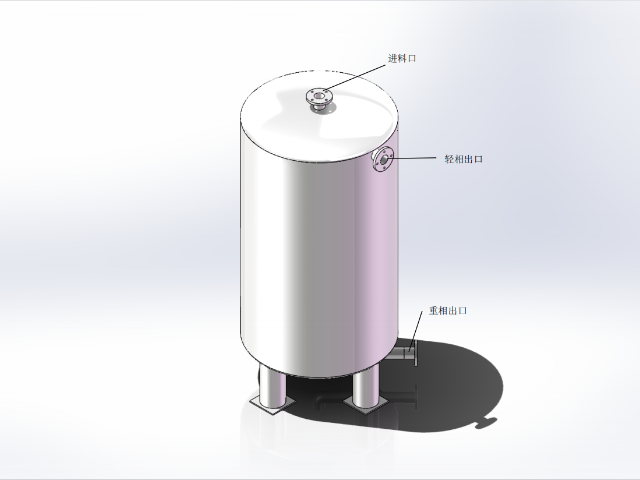
正分转盘筛板萃取塔工作原理:转盘萃取塔属于机械搅拌的塔式萃取设备,它由三部分组成:上澄清段、混合段,下澄清段。其中混合段为一圆筒形状,内部被静环挡板分割成一系列萃取室,两个静环挡板中间为固定转盘,且随着搅拌轴一起旋转。工作时,重相(水相)和轻相(有机相)分别从塔顶和塔底进入,在塔内呈逆流接触。在固定转盘的搅动下,分散相形成小液滴,使传质面积增加,完成萃取过程后,轻相和重相分别从塔顶和塔底的出口流出。
萃取塔是石油炼制、化学工业和环境保护等部门广泛应用的一种萃取设备,具有结构简单、便于安装和制造等特点。塔内填料的作用是增大两种物料的接触面积,使各物料充分接触,可以使分散相液滴不断破碎与聚合,以使液滴的表面不断更新,还可以减少连续相的轴向混合。在普通填料萃取塔内,两相依靠密度旅而逆向流动,相对速度较小,界面湍动程度低,限制了传质速率的进一步提高。为了防止分散相液滴过多聚结,增加塔内流体的湍动,可采用连续通入或断续通入压缩空气(脉冲方式)向填抖塔提供外加能量,增加液体湍动。当然湍动太厉害,会导致液液两相乳化,难以分离。 控制液位和气速萃取塔中的液位和气速对操作效果具有影响。
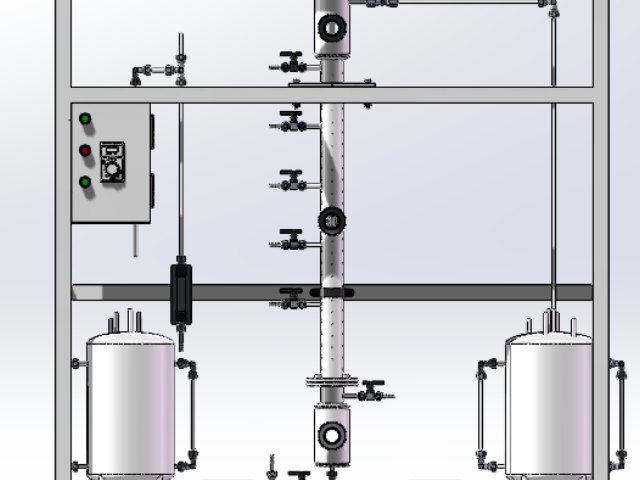
液液萃取法又称溶剂萃取或抽提。用溶剂分离和提取液体混合物中的组清穗分的过程。在液体混合物中加入与其不相混溶(或稍相混溶)的选定的溶剂,利用其组分在溶剂中的不同溶解度而达到分离或提取目的。例如用苯为溶剂从煤焦油中分离酚,用异丙醚为溶剂从稀乙酸溶液中回收乙酸等。实验室中用分液漏斗等仪器进行。工业上在填料塔、筛板塔、离心式萃取器、喷洒式萃取器等中进行。应用于有机化学、石油、食品、制药、稀有元素、原子能等工业方面。江苏正分科技是一家专业从事于连续化化工设备研发、设计、生产和销售的一体化高科技企业,致力于为客户提供连续化化工设备解决方案,欢迎广大客户咨询。 填料的空隙大小和密度可以根据需要进行调整,以控制湍流程度和流动速度。化工水洗萃取塔工业化
定期维护和检修定期对萃取塔进行维护和检修是确保塔体安全运行的必要措施。原料药中间体萃取塔答疑解惑
正分筛板萃取塔是一种液-液萃取设备,塔内主要结构是筛板。筛板萃取塔塔底引入轻相(分散相)经筛孔分散后,在重相(连续相)中上升,到上一层筛板下部聚成一层轻液,再分散,再聚集。分散的过程即萃取传质过程,塔顶和塔底分别得到萃取相和萃余相。江苏正分科技是一家专业从事于连续化化工设备研发、设计、生产和销售的一体化高科技企业,以及工艺咨询验证到售后的完整服务体系,致力于为客户提供连续化化工设备解决方案,欢迎广大客户咨询。
原料药中间体萃取塔答疑解惑
上一篇: 分层萃取塔型号
下一篇: 连续液液萃取萃取塔常见问题