高温合金锻件生产厂家
不锈钢锻件怎么锻造?材料的利用率高。金属塑性成形主要是靠金属的形体组织相对位置重新排列,而不需要切除金属。较高的生产率。锻造加工一般是利用压力机和锻锤进行成形加工的。不适合成形形状较复杂的不锈钢锻件。锻造加工是在固态下成形的,与铸造相比,金属的流动受到限制,一般需要采取加热等工艺措施才能实现。对制造形状复杂,特别是具有复杂内腔的零件或毛坯较困难。由于锻造具有上述特点,因此承受冲击或交变应力的重要零件(如传动主轴、齿圈、连杆、轨道轮等),都应采用不锈钢锻件毛坯加工,所以锻造加工在机械制造、矿山、轻工、重工等行业得到广泛应用。锻造是机械制造中毛坯和零件生产的主要方法之一,常分为自由锻、模锻等。锻件历经岁月洗礼而愈显珍贵独特,成为工业历史的见证者。高温合金锻件生产厂家
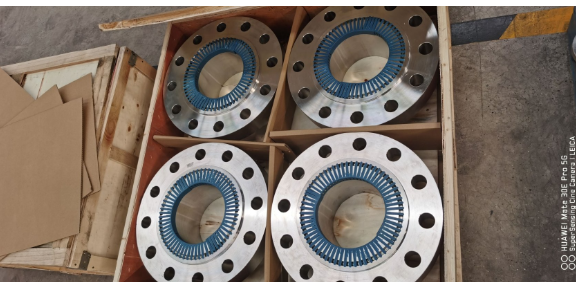
挤压锻件和模锻件区别:成型方式:挤压锻件是通过将加热后的金属坯料放入挤压机的料筒中,借助挤压杆推动坯料通过模具的孔口或缝隙挤出成型。挤压过程中,金属在模具内受到三向压应力,这使得金属可以流动并填充模具的型腔。模锻件则是使用专一用的模具进行成型。金属坯料被放置在模具的型腔内,通过施加压力(通常由锻锤或压力机提供)使其发生塑性变形,从而填充模具的型腔并获得所需的形状和尺寸。形状和尺寸精度:挤压锻件通常具有较高的形状和尺寸精度,尤其是对于那些截面形状复杂且连续的锻件。挤压工艺能够提供连续的金属流线和较少的飞边,从而减少了后续的机械加工量。模锻件也能实现较高的形状和尺寸精度,但可能需要通过多道工序和复杂的模具设计来实现。对于形状特别复杂或尺寸精度要求极高的零件,模锻可能不是Zui佳选择。甘肃双相钢锻件销售价格锻件之美在于其独特的形态与质感,令人过目难忘。
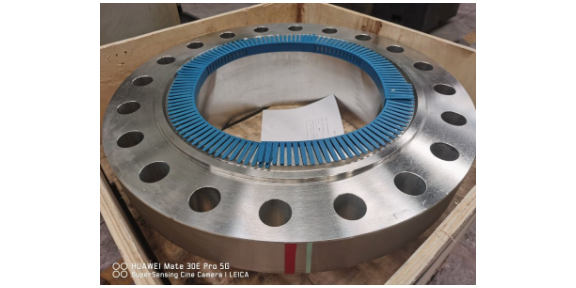
大型锻件经淬火、正火处理后,还需进行回火处理,回火是后一道热处理工艺,大型锻件回火的目的是:1、消除或降低淬火、正火冷却过程中产生的内应力;2、获得稳定的回火组织,达到所要求的力学性能技术指标;3、进一步去除锻件中的氢气或使其分布为合理;4、如前所述进一步完成冷却过程中的心部组织转变。为满足大型锻件不同的硬度等力学性能的要求,淬火后需要选用不同的温度回火。根据回火温度的不同,在生产中往往将回火过程分为低温回火,回火温度在150-250℃之间,其目的是稳定或降低淬火应力,减少钢的脆性并保持钢的高硬度,如要求HS90以上的高硬冷轧工作辊,表面淬火后应进行低温回火(130-140℃)。中温回火时回火温度一般选择在350-500℃,可以获得高的弹性极限,同时有高的韧性。在500-650℃的回火称为高温回火,主要是为获得强度,塑性和韧性良配合的综合力学性能,所以一般结构钢大型锻件经淬火或正火后都进行高温回火处理。
关于锻件,它是一种通过锻造工艺成型的金属件。锻造是一种利用锻压机械对金属坯料施加压力,使其产生塑性变形以获得具有一定机械性能、一定形状和尺寸锻件的加工方法。锻件的性能和质量通常优于铸件,因为它们经过塑性变形后,金属内部的晶粒得到细化,提高了金属的力学性能和物理性能。锻件被广泛应用于各个工业领域,如航空航天、汽车制造、石油化工、电力、矿山等。在这些领域中,锻件通常用于承受重载、冲击或高温高压等恶劣工作条件的部件制造。锻件承载着工匠的热情与执着,是工业制造领域的动人篇章。
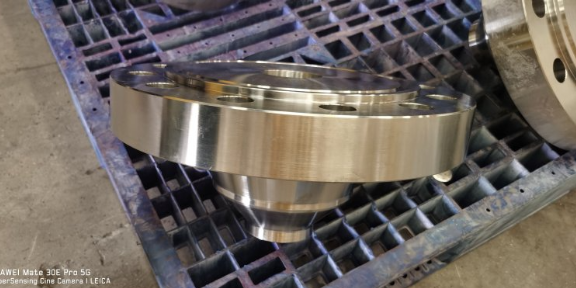
模锻件是利用模具使毛坯变形而获得锻件的锻造方法制成的金属件。这种方法生产的锻件尺寸精确,加工余量较小,结构也比较复杂,且生产效率高。模锻件的特点是与自由锻相比,其锻件的形状可以比较复杂,且能控制产品的尺寸公差,减少车加工量。模锻件适用于批量生产,但模具成本高,需有专一用的模锻设备,不适合于单件或小批量生产。模锻工艺过程包括制坯、预锻和终锻,其中制坯是将原始坯料进行加工,使其具备模锻所需的形状和尺寸;预锻是将制坯后的坯料进行初步锻造,使其接近Zui终锻件的形状;终锻则是将预锻后的坯料放入模具中进行Zui终锻造,获得所需的模锻件。锻件坚实耐用、性能稳定且安全可靠,是工业领域的放心之选。甘肃双相钢锻件销售价格
锻件历经千锤百炼而愈加坚韧有力,成为工业领域的力量象征。高温合金锻件生产厂家
模锻件广泛应用于各个工业领域,如机械、汽车、航空航天、石油化工等。在这些领域中,模锻件常用于制造承受重载、冲击或高温高压等恶劣工作条件的部件,如齿轮、曲轴、连杆、叶片、轴承等。模锻件的质量和性能对产品的使用寿命和可靠性有着重要的影响,因此在生产过程中需要进行严格的检验和控制。总之,模锻件是一种重要的锻造产品,具有高精度、高复杂度和高生产效率等优点,被广泛应用于各个工业领域。随着工业技术的不断发展,模锻工艺也将不断创新和改进,为制造业的发展做出更大的贡献。高温合金锻件生产厂家
上一篇: 黑龙江双相钢法兰生产厂家
下一篇: 江西镍基法兰生产厂家