江西医疗外壳厚板吸塑定制
厚板吸塑概念及应用领域,厚板吸塑或者称厚片吸塑,指成型材料厚度超过2毫米(一般范围为2-12毫米,甚至更厚),无法自动吸塑成型,需要在专门使用半自动吸塑成型机加工的一种工艺。按材质看,厚板吸塑成品包括ABS吸塑、PS吸塑、PMMA吸塑等,主要用于医疗行业设备外壳、广告灯箱、大型种植托盘、智能机器人外壳、玩具车车身车壳、电子仪器设备外壳、冰箱内胆、汽车内外饰等领域。尤其要重点说一下,厚板吸塑在汽车领域的应用占比正在持续增加,如汽车的内饰、保险杠、挡泥板等等,其中以ABS或者ABS+合金材料居多。厚板吸塑主要优势,厚板吸塑具有省原辅材料、重量轻、运输便捷、外观精美、密封性能好等优点,能节省人力、提高效率。在安全环保性上也是不遑多让,食品级厚板吸塑产品越随处都是。厚板吸塑加工工艺,是将定位好的板材通过烘箱加热到软化的状态,吸塑模具再和其周边形成密闭空间而将模腔内空气瞬间吸走,将板材紧紧贴覆在模具表面,冷却定型而取得制品的工艺过程吸塑成型是一个循环的过程。一个周期包括:上料-软化-反吹预拉-吸塑-冷却定型-脱模-裁切,以此循环,周而复始,再生产出一个个标准合格精美的厚板吸塑制品。厚片吸塑过程可能是能源密集型的,特别是需要高热量和维持真空水平。江西医疗外壳厚板吸塑定制
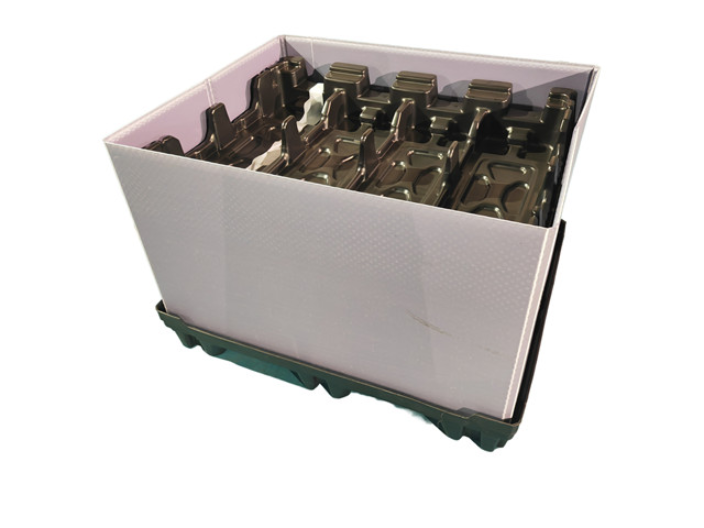
厚板吸塑特性及常见分类,厚板吸塑又称厚板吸塑,是指所用主要原材料的厚度可以超过2mm,不能在一个全自动智能机器上进行吸塑,由专门使用于建筑厚板的半自动吸塑成型机加工产品生产。厚板吸塑、厚板吸塑的特点和常见分类,吸塑包装的薄片吸塑生产方法相似,主要是真空吸塑。厚板吸塑是指所用主要原材料的厚度可以超过2mm,不能在一个全自动智能机器上进行吸塑,由专门使用于厚片的半自动吸塑成型机加工产品生产。厚板吸塑的一般流程:塑片--裁切--片材固定--加热--成型--脱模--去边--成品。江西单层厚板吸塑供应厚片吸塑商品既可以替代注塑模具加工,节约高昂的塑料模具成本费。
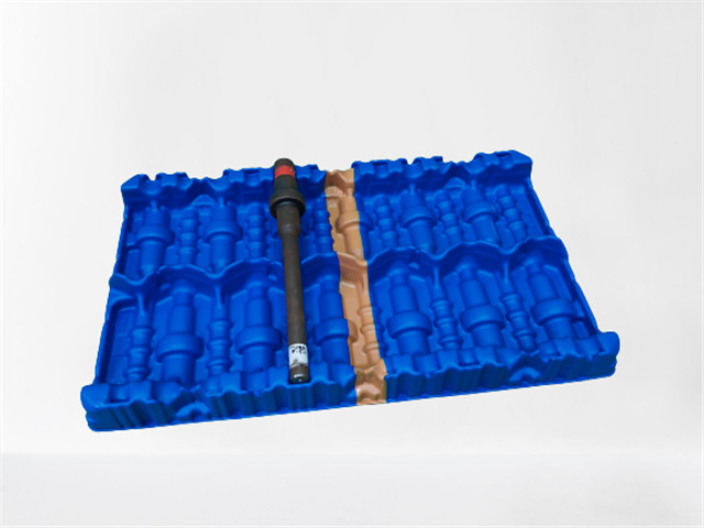
厚泡孔工艺制作的产品在我们周围是比较常见的,有些是日常生活用品,比如模压门板、塑料地板等;另一部分可用于机械设备,如机器挡板、防护罩外壳等。只从外观上看,模压门就可以用精致、方便来形容,还呈现出色彩丰富、造型独特的优点。没想到这样的产品也是采用厚吸塑工艺制作的,只需要将PVC已刻字和铣花纹粘贴在中密度板基材上,然后热压吸塑成型。通过这种技术加工后,门板四边可以密封成一个整体,即使不密封边也不用担心将来会出现脱胶等问题,因此得到消费者的青睐。
优点:厚片吸塑加工具有工程经济性在包装消费制造业中,除非你是用纸板作为包装资料,否则厚片吸塑加工技术是没有其他加工办法能与之相竞争的。 厚片吸塑加工成型主要的优点是它的工程经济性。成型复合片材、发泡片材和印刷片材的制品,以恰当改动模具来替代变化厚片吸塑加工成型机械。壁很薄的制品能够用高熔体黏度的片材厚片吸塑加工,而注射相同壁厚的则需求低熔体黏度的粒料。关于少量的塑件,有利的模具本钱是厚片吸塑加工的又一优点,而对大批量的制件,制品能到达十分 薄的壁厚及吸塑成型机器的高产出比则十分有利。高模具成本可能成为小规模制造商或低产量产品的障碍。
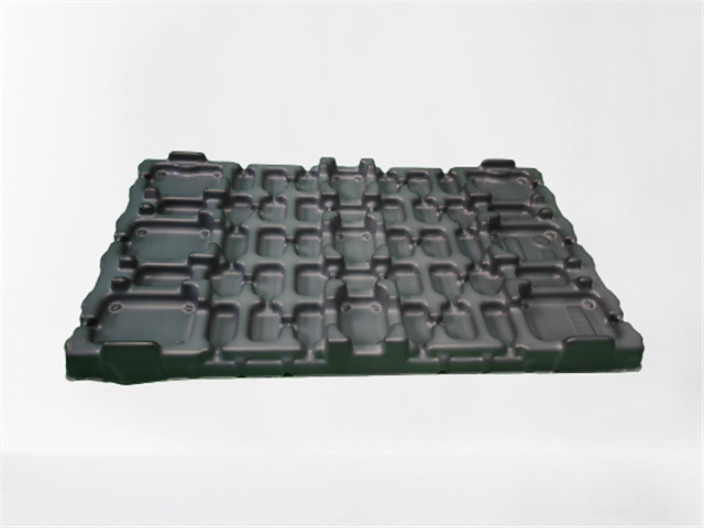
厚板吸塑常见问题及解决方案:01吸塑不完整,是因为吸塑板过薄或者模具表面太粗糙引起的。我们可以将吸塑板厚度适当增加,或者在模具表面打磨光滑。02表面出现气泡,这是因为温度控制不当或者模具未排气引起的。我们可以调整温度,或者在模具上安装排气孔来消除气泡。03模具破裂,是因为吸塑板太厚或者压力过大引起的。我们可以适当降低吸塑板厚度或者减少压力,以避免模具破裂。04表面不够光滑,是因为吸塑材料的问题或者加工设备的问题导致的。我们可以选择优良的吸塑材料或者更换更先进的加工设备来解决问题。为了提高能源效率,制造商可以投资现代化、节能的加热器和真空泵。无锡厚板吸塑制品
厚片吸塑在生产,使用的厚度大,可以达到10毫米以上,可以保护产品,抵御外界的影响。江西医疗外壳厚板吸塑定制
厚片吸塑与薄片吸塑有什么区别?1、材料上不同:厚片吸塑一般使用ABS、PP、HDPE、PMMA、PVC等,薄片吸塑常用PVC、PET、PP、PS、PETG等材料。2、产品应用方面不同:厚片吸塑通常用以机器人外壳吸塑,广告吸塑、美容美体设备吸塑、医疗设备外壳吸塑、高尔夫球车、玩具车壳,船体外壳吸塑,塑料托盘吸塑等,薄片一般用以硬件设备、电子器件、化妆品、食品、医疗卫生保健产品、玩具、日用品等。3、工艺上不同:厚片吸塑加工过程比薄片吸塑更复杂,后加工方式不相同,厚片吸塑相较于薄片吸塑成本更高一些。4、厚度不同:厚片吸塑所用材料为片材,1-15毫米,而薄片吸塑所用的材料为卷材,厚度为0.2-1毫米。江西医疗外壳厚板吸塑定制
上一篇: 天津HIPS厚板吸塑
下一篇: 浙江大型厚板吸塑厂家