电池包测试系统
Optoquick让操作变得更高效。Optoquick减少了生产过程中,浪费在零件验证上的时间。Optoquick的操作不但快速,而且可将它直接安装在生产机床旁,消除了昂贵的工件物流成本。使用Optoquick提高了生产率,并可对生产高峰进行管理。因此,可在数月之内获取投资回报。除此之外,还可以提高生产质量水平。Optoquick在生产机床旁安装,从而可更加频繁进行工件的测量验证与确认。因此,Optoquick可提升质量保障,在一定程度减少废件的生产。局部放电绝缘测试是一种更复杂的技术,对外部电磁干扰不敏感,因此更适合在生产环境中使用。电池包测试系统
检测设备
在单啮和变速箱(减速机)偏差分析方面,2速或1速变速箱(减速机)零件加工必须满足高精度要求,以确保零件装配后不会对车辆造成额外的噪音。SF测试是齿轮加工后的啮合旋转测试。测试时,标准齿轮至于适当的安装位置:其与待测齿轮齿隙适当,且单面啮合。然后光学编码器测量其相对于标准齿轮的角位移。SF测试结果包括变速箱(减速机)偏差数据的采集和噪音分析。Marposs还开发了一种特殊的单啮测试方案,用于在实验室测试原型零件,以改善齿轮设计过程。哪里有检测设备马波斯在泄漏测试方案领域拥有丰富的经验,方案可集成不同技术,确保可以为整个电驱动产品组件提供解决方案。
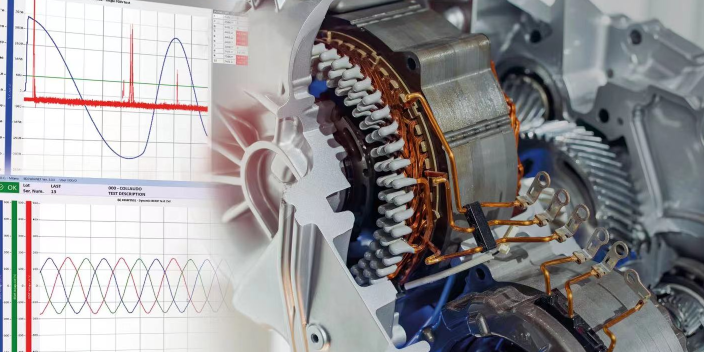
描述
凡是使用有机电解液的电芯,均可通过这项技术来检测(纽扣电芯、圆柱电芯、方形电芯或软包电芯)。这项技术可跟踪锂离子电芯中常用的多种不同成分,例如碳酸二甲酯(DMC),碳酸二乙酯(DEC),碳酸甲乙酯(EMC),丙酸丙酯(PP)等。这项技术可在不同工艺阶段检测电芯:如,注液和密封后检测,化成后检测,degassing和**终密封后检测,还可在EOL测试中检测。测试期间电芯置于真空箱内。如果电芯外壳泄漏,电解液部分成分将气化,逸出电芯进入真空箱内。这项检测的基本原理就是:用四极质谱仪示踪电解液蒸汽,以此测量泄漏情况。此检测方法可用于大批量生产的生产线,检测速度快且全程自动化,满足电芯生产的高节拍要求。我们针对这项检测开发了一系列不同的工艺方式(专利申请中),可以有效缩短周期。根据电芯的类型(纽扣、圆柱、方形或软包)及尺寸不同,可对真空箱的尺寸和形状、真空箱内的电芯数量、测试周期等进行定制化设计。首页图片为采用电解液示踪技术自动检测电芯泄漏的方案,,该方案运用于纽扣电芯的自动化高节拍量产。为避免电芯污染真空箱,首先需要进行了一次大漏测试,以排除有明显泄漏缺陷的电芯。
电机及其组件的质量保证一代电机面临的挑战是如优化部件生产和组装的效率、质量和成本。电机技术在全球范围内的空前增长,特别是在汽车领域,使制造商和终用户对组件可靠性产生了全新的认知。这一新趋势对生产链的质量控制和过程控制提出了新的要求。因此,汽车行业越来越重视电机的可靠性,并开始转向生产更高质量的零部件和总成。Marposs开发一整套方案,致力于电动车电机及其组件的过程控制、在线和离线质量检测。MARPOSS是一如既往的合作伙伴迎接新的电动汽车挑战。Marposs可以提供测试方案,用于在线或离线的定子绝缘质量检测。
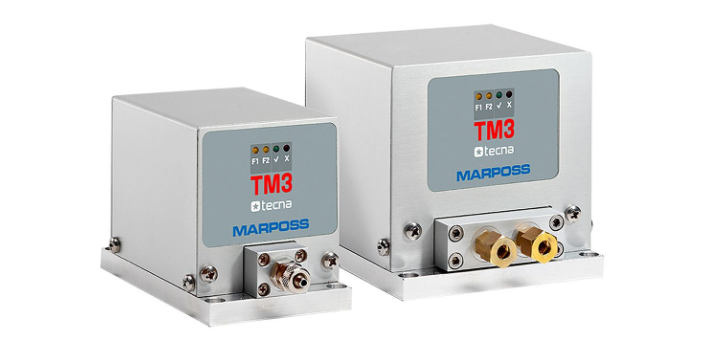
MARPOSS可以用累积室中的氦气对电池PACK进行泄漏测试,待测零件在环境压力下被放入密封室,然后充入氦气,通过氦质谱仪检测是否有示踪气体从待测零件流到密封室里。这种零部件半成品和pack成品的泄漏测试技术是一种非常可靠的方法,可以确保产品整体密封性良好,从而防止水进入电池pack内部。使用示踪气体的泄漏测试方法可确保比较大的测试灵敏度,其可以识别极低的泄漏情况,适用于大容积部件和任何环境条件。我们在累积室氦气泄漏测试方案可以测量10-2-10-4SCC/sec的泄漏。马波斯集团Hetech品牌一直致力于泄漏检测系统领域的研究,也是这一崭新市场生产商的有力战略合作伙伴。全自动激光测径仪
马波斯Hetech一直致力于电动汽车发动机压铸外壳的泄漏检测系统的研发与制造,并获得了市场认可。电池包测试系统
玻璃容器加工尺寸控制的方法:
加工尺寸控制包括:•总高度•垂直度•嘴平行度
•外径,或长/短边,以及瓶身的对角线•颈部外径•各种表面处理的许多不同参数(例如直径、高度、半径、角度……)
这些尺寸控制可以通过go-no-go通止规在生产线附近实现,也可以在实验室使用手动量规或半自动/自动计量系统在样件上进行。但使用通止规进行尺寸控制会有一些问题:它不提供定量信息,而且依赖于操作员的技能。持续使用通止规成本高昂,因为每件产品都需要一套**的通止规,这些硬规需要日常管理并定期重新校准。此外,这种方法不可能收集所有测量数据并进行统计分析以改进加工工艺和过程。 电池包测试系统