江苏数控机床维修价格
机床是制造业中不可或缺的重要设备,其稳定运行对于生产效率和产品质量有着至关重要的影响。然而,由于机床的复杂性和长期使用,故障是难以避免的。对于频繁出现的故障,机床维修人员需要进行深入分析,找出根本原因并解决,以确保机床的稳定运行。首先,机床维修人员需要对故障进行分类和记录。通过对故障的分类和记录,可以更好地了解机床的故障类型和频率,以及故障发生的时间和地点等信息。这些信息可以为后续的故障分析和解决提供有力的支持。其次,机床维修人员需要进行故障分析。故障分析是找出故障根本原因的关键步骤。机床维修人员需要对故障进行多方面的分析,包括机床的结构、工作原理、控制系统等方面。通过对故障的分析,可以找出故障的根本原因,从而采取相应的措施进行解决。然后,机床维修人员需要采取相应的措施进行解决。根据故障分析的结果,机床维修人员可以采取不同的措施进行解决,包括更换部件、调整参数、改进程序等方面。机床维修要关注机床的软件系统,确保其正常运行和更新。江苏数控机床维修价格
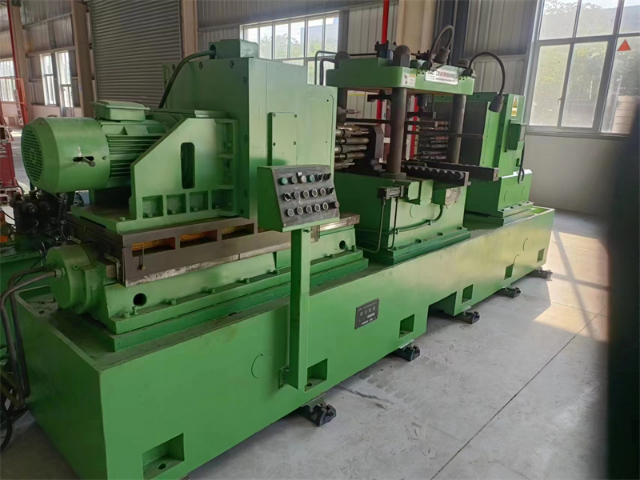
定期维修可以帮助维修人员及时发现和解决设备的潜在问题,减少设备故障的发生频率,提高设备的可靠性和稳定性。首先,定期维修可以检查设备的各个部件和系统的工作状态。通过观察设备的运行情况、检查设备的运行数据和记录设备的故障情况,可以了解设备的工作状态是否正常。如果发现设备存在异常情况,可以及时采取措施进行修复或更换,避免设备故障的发生。例如,定期检查设备的润滑系统,可以及时发现润滑油的污染或耗尽,并及时更换润滑油,保证设备的正常运转。折弯机大修报价对于精密机床的维修,要特别注意机床的几何精度和运动精度。
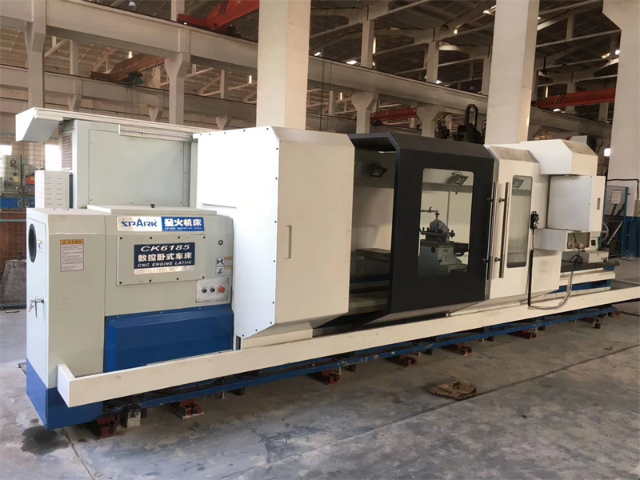
机床维修人员需要配备各种测量仪器。这些测量仪器包括千分尺、微米表、测厚仪、扭矩扳手等,用于对机床的各个部件进行精确的尺寸测量和调整。例如,在更换轴承时,维修人员需要使用千分尺来测量轴承的内外径和厚度,以确保新轴承与原轴承相匹配;在调整丝杠间隙时,维修人员需要使用微米表来测量丝杠的轴向窜动量,以确保丝杠的运动精度。通过使用这些测量仪器,维修人员可以确保机床的各个部件都符合设计要求,从而提高机床的运行稳定性和加工精度。
清洁工作包括清理机床表面的灰尘和油污,清理导轨和丝杠上的金属屑,清洗齿轮和轴承等。清洁时应注意使用适当的清洁剂和工具,避免对机床造成损坏。其次,定期润滑是机床维修中另一个重要的环节。机床的各个部件在运行过程中会产生摩擦和磨损,如果不及时进行润滑,会导致部件的过早损坏和机床的停机。因此,定期润滑是保持机床正常运行的关键。润滑工作包括给导轨、丝杠、齿轮等部件涂抹适量的润滑油或润滑脂,以减少摩擦和磨损。润滑时应注意选择合适的润滑油或润滑脂,并按照规定的周期进行润滑。机床维修要定期对维修记录进行分析,总结经验,提高维修水平。
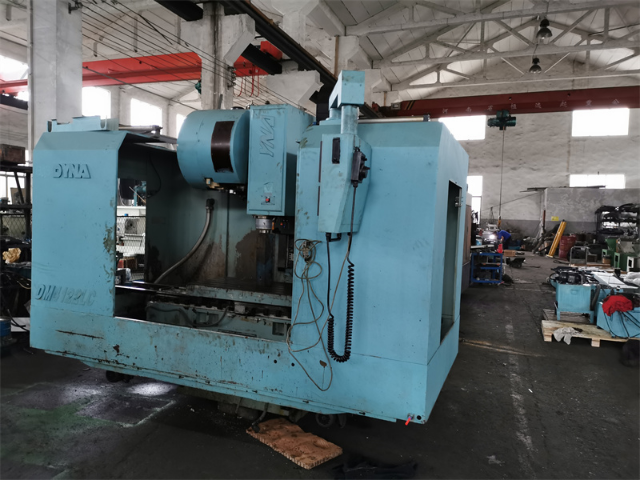
加工中心大修可以解决机器的故障问题。在长时间的使用过程中,加工中心的各个部件可能会因为磨损、老化或者外力的作用而出现故障。这些故障可能会导致机器无法正常运转,影响生产效率和产品质量。通过进行大修,可以对机器进行多方面的检查和维修,及时发现并解决故障问题,确保机器能够正常运行。加工中心大修可以提高机器的性能和效率。随着科技的不断进步,新的加工技术和设备不断涌现,旧的加工中心可能无法满足生产要求。通过进行大修,可以将机器升级为新的型号或者更换新的部件,提高其性能和效率。这样不仅可以提高生产效率,还可以降低生产成本,提高企业的竞争力。使用专业维修工具和仪器,能够提高机床维修的效率和准确性。cnc数控机床维修哪家服务好
机床维修包括日常保养、故障排除和设备升级等多个方面。江苏数控机床维修价格
加工中心大修是指对机器进行多方面的检修、维护和更换部件的工作。一般来说,加工中心大修的周期为3-5年,具体周期根据机器的使用情况、使用环境、维护情况等因素而定。加工中心大修包括以下几个方面的工作:1.机器的多方面检查:对机器的各个部件进行检查,包括机床床身、导轨、滑块、主轴、伺服电机、液压系统、气动系统等。检查的目的是发现机器存在的问题,为后续的维护工作提供依据。2.机器的清洗和润滑:对机器进行多方面的清洗和润滑,清理机器表面的污垢和油渍,保证机器的清洁度和润滑性。清洗和润滑的目的是减少机器的摩擦和磨损,提高机器的精度和稳定性。3.机器的更换部件:根据机器的检查结果,对机器的部件进行更换。更换的部件包括机床床身、导轨、滑块、主轴、伺服电机、液压系统、气动系统等。更换部件的目的是保证机器的正常运转,提高机器的精度和稳定性。4.机器的调试和校准:对机器进行多方面的调试和校准,包括机器的机械调试、电气调试、液压调试等。调试和校准的目的是保证机器的精度和稳定性,使机器能够达到设计要求。江苏数控机床维修价格
上一篇: 吉林小型油水分离设备
下一篇: 工业机床油水分离机直销