芜湖钣金压铆螺柱方案设计
针对不同的应用场景和需求,可以对压铆方案进行优化和改进。例如,通过调整压铆件的形状和尺寸、改进压铆设备的结构和性能等方式,提高压铆连接的效率和质量。同时,还可以研发新型压铆材料和工艺,以满足更高要求的紧固连接需求。压铆方案的成本包括设备投资、材料成本、人工成本等多个方面。为了降低生产成本,提高产品的竞争力,需要对压铆方案的成本进行深入分析和控制。例如,通过选用合适的压铆件和设备、优化生产工艺、提高生产效率等方式,可以有效降低生产成本。压铆方案的优化有助于减少材料的浪费。芜湖钣金压铆螺柱方案设计
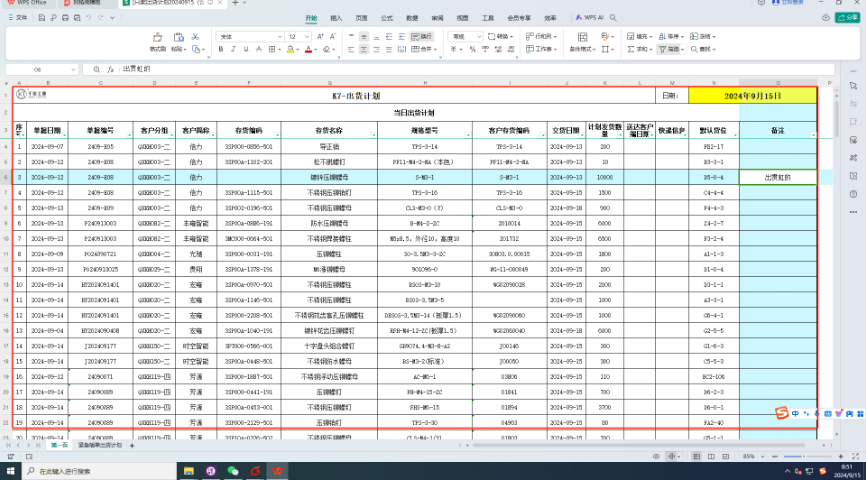
为了满足不同客户的特定需求和应用场景,许多压铆设备制造商和供应商提供定制化服务。他们可以根据客户的具体要求和工件规格定制压铆设备、压铆件和压铆工艺方案;同时,他们还可以提供现场安装、调试和培训等服务支持,确保客户能够顺利使用和维护压铆设备并达到预期的生产效果。压铆方案作为一种高效、可靠、环保的连接技术,在现代制造业中具有普遍的应用前景和发展潜力。为了充分发挥压铆方案的优势并实现较佳的生产效果和经济效益,建议企业在选择压铆设备和压铆件时充分考虑实际需求和应用场景;同时加强人员培训和技术支持力度;并关注行业动态和技术发展趋势以便及时调整和优化压铆方案以适应市场需求的变化。安庆压铆方案设计压铆方案的选择应考虑环境因素的影响。
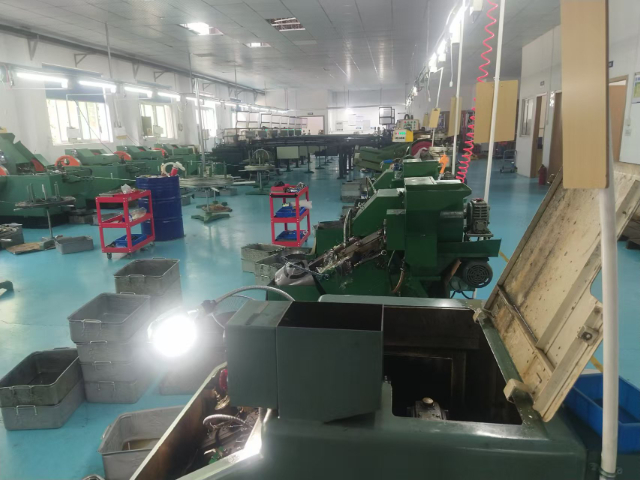
实施压铆方案通常包括以下步骤:确定连接点位置、预钻孔、插入铆钉、施加压力使基材变形固定。每一步都需要严格按照工艺要求进行,以确保之后连接效果。为保证压铆质量,需要在各个环节进行严格控制。首先是原材料检验,确保所有材料符合标准;其次是工艺参数设定,包括压力值、变形量等;之后是成品检测,通过目测、测量等方法检查连接部位是否达到预期效果。虽然压铆技术初期投资较小,但在长期使用过程中仍需考虑维护成本、能耗等因素。因此,在制定压铆方案时应综合考虑各项成本,寻找较优平衡点。此外,通过优化设计、提高生产效率等方式也能进一步降低成本。
压铆底孔的设计是压铆方案中的关键环节之一。底孔的尺寸、形状和位置需根据压铆件的规格和工件的材质进行精确计算和设计,以确保压铆过程中压铆件能够顺利嵌入并形成良好的机械连接。压铆力的大小直接影响压铆连接的质量和稳定性。在压铆过程中,需要根据工件的材质、厚度以及压铆件的规格等因素对压铆力进行精确控制和调节。过大或过小的压铆力都可能导致连接不良或工件损坏等问题。压铆方案具有多种优点,如连接强度高、可靠性好、安装简便、节省空间等。与传统的焊接、螺栓连接等方式相比,压铆方案无需预热、钻孔、攻丝等繁琐工序,有效提高了生产效率和产品质量。通过压铆方案可以提高产能。
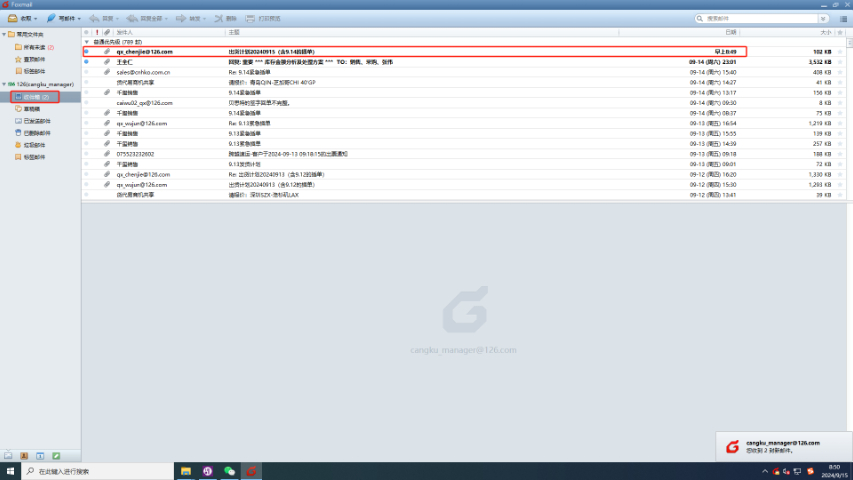
为保证压铆质量,需要根据具体情况设定合适的工艺参数,如铆接压力、铆接速度等。这些参数的合理设置对提高连接强度、防止零件损伤至关重要。通过改进压铆工艺,可以进一步提升连接质量和生产效率。例如,采用多点同步压铆技术可以减小工件变形;选择合适尺寸的铆钉则有助于提高连接部位的密封性能。航空航天制造业对零部件连接要求极高,压铆因其独特的优点被普遍应用于该领域。飞机机身、发动机组件等部位常见到压铆连接的身影。这些连接部位需承受剧烈振动、高温高压等恶劣条件考验,压铆技术恰好满足了这些需求。压铆方案的实施需要对设备进行定期维护。马鞍山花齿类压铆方案设计
压铆方案的实施需考虑材料的导电性。芜湖钣金压铆螺柱方案设计
与传统的焊接、螺栓连接等方式相比,压铆方案具有明显的环保优势。压铆过程中无需使用焊接材料或产生有害物质,减少了环境污染的风险。同时,压铆件可以重复使用或回收再利用,降低了资源浪费。随着自动化技术的不断发展,压铆方案也逐步向自动化、智能化方向发展。自动化压铆设备可以有效提高生产效率和质量稳定性,降低人工成本。同时,通过集成先进的传感器和控制系统,还可以实现压铆过程的实时监控和远程操控。压铆方案在特定行业中的应用尤为普遍。例如,在汽车制造领域,压铆方案被用于连接车身结构件、悬挂系统等关键部件;在航空航天领域,压铆方案则用于连接飞机蒙皮、翼梁等强度高的部件。这些应用充分展示了压铆方案在复杂结构连接中的可靠性和高效性。芜湖钣金压铆螺柱方案设计
上一篇: 徐州钣金压铆螺柱方案介绍
下一篇: 无锡压铆螺柱推扭力多大