重庆品质管理模具制造管理系统零件进度
在实施过程中,企业需要选择合适的系统供应商和合作伙伴,确保系统的质量和稳定性。同时,企业还需要制定详细的实施计划和时间表,确保系统能够按时交付并投入使用。此外,企业还需要建立相应的管理制度和流程,确保系统能够正常运行并发挥比较大效益。以某有名模具制造企业为例,该企业引入了模具制造管理系统后,实现了生产过程的和方面优化和自动化。通过该系统,企业能够快速响应市场需求并缩短产品开发周期;同时,该系统还帮助企业实现了资源的优化配置和合理利用,降低了库存和浪费。在实施过程中,该企业选择了具有丰富经验和实力的系统供应商和合作伙伴,并制定了详细的实施计划和时间表。经过双方的共同努力和紧密合作,该系统成功上线并投入使用,为企业带来了明显的经济效益和社会效益。模具设计、制造、维护一体化管理。重庆品质管理模具制造管理系统零件进度
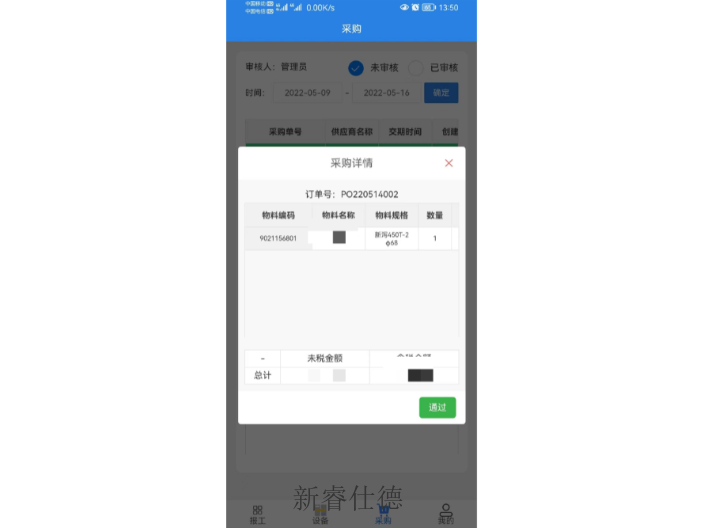
在人力资源管理方面,模具制造管理系统也发挥了重要作用。系统可以实时追踪员工的工作状态、绩效和培训计划等,为企业提供了准确的人力资源信息。企业可以根据系统提供的数据,制定合理的人力资源计划,优化员工配置,提高员工的工作效率和满意度。同时,系统还支持员工的在线培训和考核,提高了员工的技能水平和综合素质。此外,模具制造管理系统还具有良好的可扩展性和灵活性。企业可以根据自身的需求和变化,对系统进行定制和扩展,满足不同的业务需求。同时,系统还支持与其他企业信息系统的集成和对接,实现了信息的共享和协同工作,提高了企业整体的管理效率和竞争力。安徽项目管理模具制造管理系统设计作业管理&BOM清单引入模具制造管理系统,提升客户满意度。
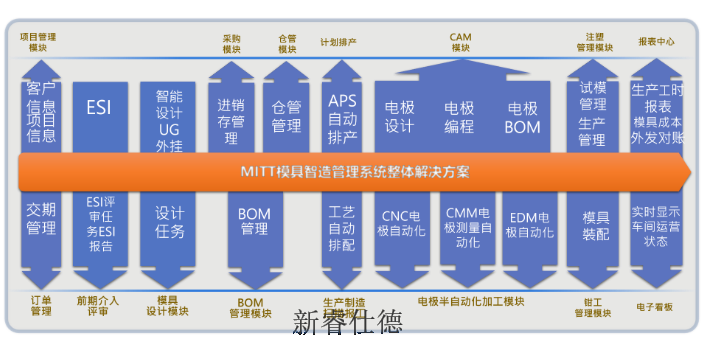
模具智能无线计数器的主要功能之一是实时计数与数据传输。在模具使用过程中,计数器能够准确地记录每一次模具的使用次数,并通过无线网络将数据传输至后台管理系统。这使得生产管理人员能够随时掌握模具的使用状态,合理安排模具的更换与维护,避免生产中断和产品质量问题。此外,模具智能无线计数器还具备数据分析和预警功能。通过对收集到的数据进行深度分析,计数器能够预测模具的寿命和潜在故障,提前发出预警信号,提醒管理人员及时采取措施。这不仅能够降低模具损坏的风险,还能够减少生产中的不确定因素,提高生产效率。
企业模具制造管理系统的主要功能在于其强大的数据处理能力和智能化管理手段。该系统通过引入云计算、大数据、物联网等先进技术,实现了对模具制造全过程的准确控制和智能化管理。在数据处理方面,系统能够实时收集模具制造过程中的各项数据,如设备状态、生产进度、物料消耗等,并通过数据分析技术,对数据进行深入挖掘和分析,为企业提供准确的决策支持。同时,系统还支持数据的可视化展示,使管理人员能够直观地了解生产情况,做出更加科学的决策。模具制造管理系统,让模具制造更智能、更高效。
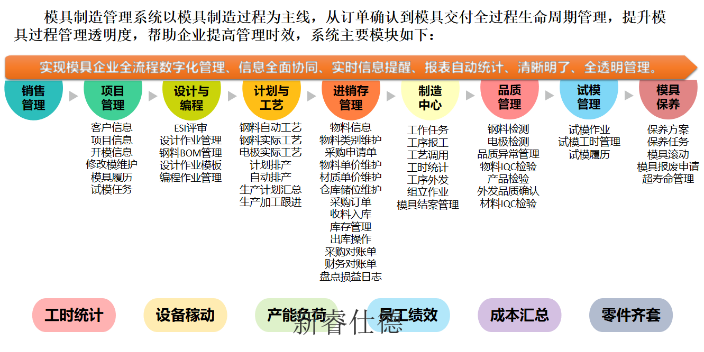
企业模具制造管理系统的实施能够为企业带来明显的经济效益和管理效益。下面以一个具体的案例来展示其实施效果。某汽车零部件制造企业通过引入企业模具制造管理系统,实现了对模具制造全过程的智能化管理。在实施该系统后,企业的模具制造效率得到了明显提升,生产周期缩短了约30%;同时,由于系统能够实时监控设备状态和物料消耗情况,企业能够及时发现并解决生产过程中的问题,降低了生产故障率和成本。此外,系统还提供了丰富的数据分析功能,帮助企业深入了解生产情况,优化生产计划,提高了企业的管理水平和响应速度。除了经济效益外,企业模具制造管理系统的实施还带来了明显的管理效益。通过实现信息的共享和协同工作,企业能够加强与其他部门和供应商的合作,提高整个供应链的协同效率。同时,系统还能够提高模具制造过程的可追溯性和透明度,使企业的生产活动更加规范和可控。引入模具制造管理系统,缩短产品上市周期。辽宁设计中心模具制造管理系统工时报表
系统化数据分析,助力模具制造企业持续改进。重庆品质管理模具制造管理系统零件进度
模具智能无线计数器,以其独特的无线技术和智能算法,正逐渐改变着模具管理的方式,为企业提供了更为便捷、高效的模具计数解决方案。在传统模具管理中,模具计数通常依赖于人工操作或有线计数器,这种方式不仅效率低下,而且容易出错。模具智能无线计数器的出现,彻底解决了这一问题。它采用无线通信技术,实现了模具使用数据的实时传输和自动记录,无需人工干预,提高了计数的准确性和效率。同时,模具智能无线计数器还具备强大的数据处理和分析能力。它可以根据收集到的数据,智能分析模具的使用情况、磨损程度等信息,为企业的模具管理提供有力支持。企业可以根据这些数据,制定更为科学的模具更换和维护计划,降低生产成本,提高生产效率。重庆品质管理模具制造管理系统零件进度
上一篇: 广东报表中心模具制造管理系统模具信息
下一篇: 辽宁计划与工艺模具制造管理系统模具信息