成都氧化锌脱硫反应器运营成本
沼气生物脱硫中的Sulfothane采用广泛应用并行之有效的技术,整个过程无含硫化物废水产生,可处理含H2S达50000 ppm的气体。沼气洗涤塔在逆向流模式下运行,因此能够高效去除沼气中的H2S。处理后的沼气中H2S含量甚至低于25ppm,去除率达99%。该工艺能在未稀释沼气的情况下很大降低沼气的臭味、毒性和腐蚀性,因在该工艺中,沼气洗涤与曝气阶段是严格分离的。该系统采用自动化控制,且足够环保安全,对电力需求低的特性也使得企业可进一步减少能源消耗。作为工艺流程重要组成单元之一的洗涤塔无阻塞问题且基本无需维护。该工艺适合于在正常的环境温度和压力下运行,且几乎无需投加化学药剂(只需补充少量的含硫排出液中损失的化学药剂)。回收的硫易于被处置或实现回用,如用于硫酸生产或作为肥料。生物脱硫包含沼气输送系统、冷却系统、生物脱硫塔系统等多个系统。成都氧化锌脱硫反应器运营成本
脱硫反应器
沼气生物脱硫生物洗涤塔中填料的选择:
填料的作用是为填料塔内气液两相进行接触时提供表面,因此填料是填料塔的主要部件,是决定脱硫效率大小的主要因素之一。理想的填料不仅耐热和耐腐蚀性高,对液体的浸润性好,同时便于制造、价格低廉。一般常用的填料有实体填料(拉西环、鲍尔环、共轭环、矩鞍环等)和网体填料(网鞍填料、波纹网填料、格栅填料等)。
鲍尔环由普通拉西环改进而成,具有通量大,阻力小、分离效率高及操作弹性大等优点。同时塑料与金属和陶瓷相比,成本低廉、性能稳定、耐腐蚀。这些性质使得塑料鲍尔环成为好的填料选择。 湖南脱硫反应器沼气生物脱硫设备:一种使用生物菌株从沼气中去除高腐蚀性和高毒性硫化氢气体的方法。
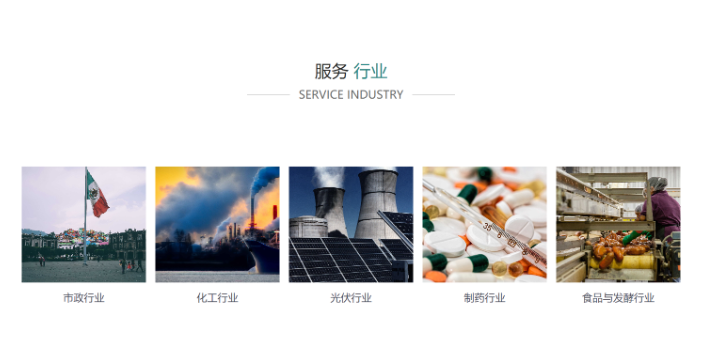
沼气生物脱硫中生物反应器的工作原理:
生物反应器也是沼气生物脱硫的一个重要组成部分,它主要用来完成硫化物的吸附降解过程。其工作过程主要是当含有硫化物的吸收液进入生物反应器后,活性污泥中的脱硫细菌将硫化物吸收氧化,硫化物首先被氧化成S单质,同时生成OH,作为碱液在吸收塔中吸收H₂S。部分单质S进一步被氧化成SO²,生成H,需要补充部分碱中和这部分氢离子。氧化产物经沉淀池沉淀后,离开生物反应器,再生的碱性液体在碱液循环泵的作用下被送至吸收塔的顶部。生物反应器内装有曝气装置为反应器内的脱硫细菌提供所需要的氧气,同时增加脱硫细菌和硫化物的接触面积,以增加脱硫效率。为了调节落液的pH值和为脱硫细菌提供所需的营养物质,通过补料管为生物反应器补充碱液和所需的营养盐。
脱硫塔,也叫烟气脱硫器,是一种用于减少烟气中二氧化硫(SO2)排放的设备。在热电厂、钢铁厂、炼油厂、水泥厂等工业生产中,由于燃烧煤、油、气等燃料会产生二氧化硫等有害气体,会对环境和人体健康造成影响,需要进行处理。脱硫塔的工作原理是利用碱性吸收液(例如石灰石浆、氨水等)与烟气进行接触反应,将其中的二氧化硫吸收转化为硫酸盐或硬脂酸盐等物质,以达到减少二氧化硫排放的目的。脱硫塔通常由吸收塔、喷雾器、控制器等部件组成。当烟气通过吸收塔时,会与喷雾器所喷洒的碱性吸收液接触,二氧化硫会被吸附,而氧化物、颗粒物等物质则会被过滤掉。通过这种方式,可以有效减少二氧化硫的排放。湿法脱硫可以归纳分为物理吸收法、化学吸收法和氧化法三种。
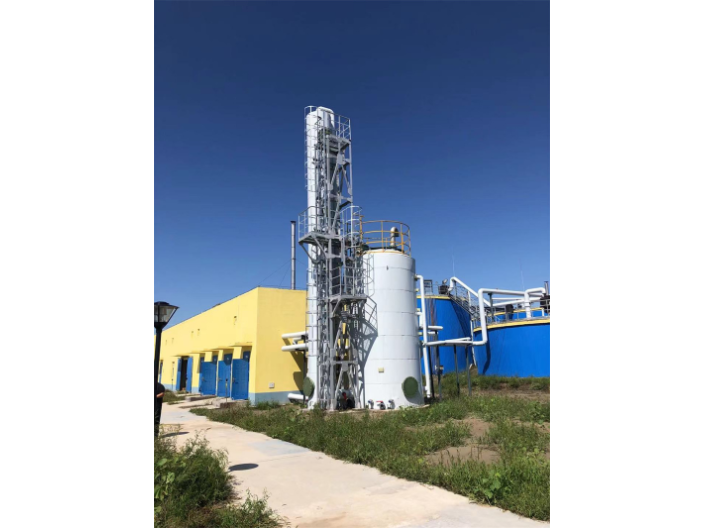
沼气生物脱硫的化能自养型微生物脱硫原理:化能自养型微生物以CO2为碳源,一起在氧化S2-的进程中获得能量。在有机碳源存在的情况下,部分品种的自养微生物可以运用有机体碳源进行异养代谢。化能自养型微生物将S2-转化为单质硫,既可以在有氧的条件下进行,也可以在无氧的条件下进行。在有氧的情况下氧作为电子受体,而在无氧的情况下可以运用硝化物作为电子受体。碧州环保很多化能自养型微生物都能以单质硫、H2S、硫代硫酸盐以及有机硫化物为电子供体,其间具有代表性的微生物是氧化亚铁硫杆菌、脱氮硫杆菌、排硫硫杆菌、氧化硫硫杆菌。沼气一体化生物脱硫反应器运行管理方便。北京氧化锌脱硫反应器系统
沼气一体化生物脱硫反应器耗能很低。成都氧化锌脱硫反应器运营成本
沼气脱硫的方法可以分为物理、化学和生物法。物理就是利用活性炭进行吸附,化学方法多用干法的氧化铁脱硫以及湿法络合铁脱硫。生物法这是利用活性菌进行硫元素的吸收转化。在选择脱硫脱水设备时应结合沼气中硫化氢的含量、所需达到的脱硫程度以及该工程的产气量和工程预算进行选择。在对沼气进行净化处理时,应按照以下要求进行:1,一级脱硫达不到要求的,应增设二级脱硫设备;2,生物和湿法脱硫设备须位于脱水设备前,干法脱硫应在脱水设备之后;3,脱硫设备应配有备用系统;4,脱硫设备前后都应设置阀门;5,脱硫设备前后都要设置抽样检查装置;6,淘汰下来的脱硫剂及污泥的处理应符合环保要求;7,脱硫和污泥必须符合环保要求。成都氧化锌脱硫反应器运营成本
上一篇: 湖北超重力脱硫反应器定制加工
下一篇: 石家庄AMX脱氮反应器设备