江苏板钢筋加工定制
冷拔工艺是一种将钢筋拉伸到所需长度和形状的加工方式。与冷拉工艺相比,冷拔工艺对钢筋的变形更为剧烈,不仅受到拉伸作用,还受到挤压作用。经过一次或多次冷拔后,钢筋的屈服点可提高40%-60%,抗拉强度显著提高,但塑性和韧性会有所降低。冷拔工艺使得钢筋具有硬质钢材的特点,广泛应用于对强度和硬度要求较高的场合。冷轧工艺是将圆钢在轧钢机上轧制成断面形状规则的钢筋,如冷轧带肋钢筋和冷轧扭钢筋。冷轧带肋钢筋在钢筋表面形成肋装条纹,增强了与混凝土的粘结力;冷轧扭钢筋则通过调直、冷轧扁、冷扭转等工序一次成型,具有独特的螺旋状截面,提高了钢筋的锚固强度和延性。冷轧工艺不仅提高了钢筋的强度,还改善了其使用性能,广泛应用于建筑、桥梁等工程领域。钢筋加工是建筑施工中的一项基础工作,它对于整个工程的顺利进行具有重要意义。江苏板钢筋加工定制
钢筋加工
冷钢筋加工作为建筑工程领域的重要环节,对于提高建筑结构的质量和安全性具有不可替代的作用。通过冷拉、冷拔、冷轧等工艺,可以提高钢筋的强度、硬度、韧性和塑性,精确控制钢筋的尺寸和形状,节约材料和降低成本。在冷钢筋加工过程中,应严格控制原材料质量、加工工艺参数和成品质量,加强安全管理,确保加工质量和安全生产。同时,随着科技的不断进步和环保意识的日益增强,冷钢筋加工将不断朝着自动化、智能化、绿色环保的方向发展,为建筑工程的高质量、高效率建设提供更加坚实的支撑。南通D6钢筋加工方法通过对冷钢筋进行科学合理的加工处理,能够提高其使用效率,降低工程成本。
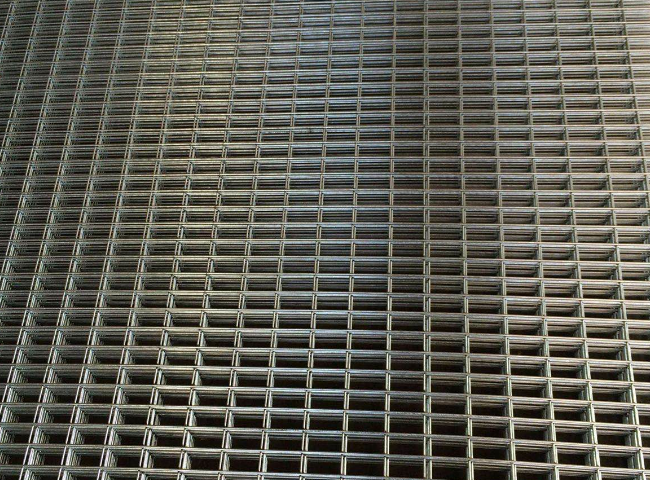
关于板钢筋绑扎安装:板的钢筋在施工前先搭好排架,铺好底模,绑扎前准确测量墙柱轴线及模板控制线并作好标记。平板钢筋网绑扎时,四周钢筋交叉点每点扎牢,绑扎时注意相邻绑点的铁丝要成八字形,以免网片歪斜变形,板的钢筋网绑扎还应注意板上部的负筋位置。板的底部钢筋伸入支座≥10d且不小于120mm。板支座上部钢筋(负筋)两端设直钩,边支座负筋伸入梁内满足锚固长度。双向板的底部钢筋,短跨钢筋置下排,长跨钢筋置上排。跨度大于4米的板,要求板中起拱L/400。
钢筋加工工艺是指将钢筋原材料经过一系列的加工工序,使其成为符合工程要求的钢筋制品的过程。钢筋加工工艺包括钢筋除锈、调直、切断、弯曲、焊接等,这些工序都需要按照规定的工艺参数和操作规程进行,以保证钢筋制品的质量和稳定性。钢筋连接技术钢筋连接技术是指在施工过程中,将两根钢筋牢固地连接在一起的技术。常见的钢筋连接方法有焊接、绑扎、机械连接等。不同的连接方法具有不同的特点和适用范围,应根据实际情况选择合适的连接方法。焊接方法的优点是连接强度高、稳定性好,但易受到操作人员技能水平的影响;绑扎方法的优点是简单易行,但连接强度较低;机械连接方法的优点是操作简便、效率高,但需要使用用的连接套件。钢筋加工质量直接影响到建筑物的质量和安全,因此需要严格按照标准执行。
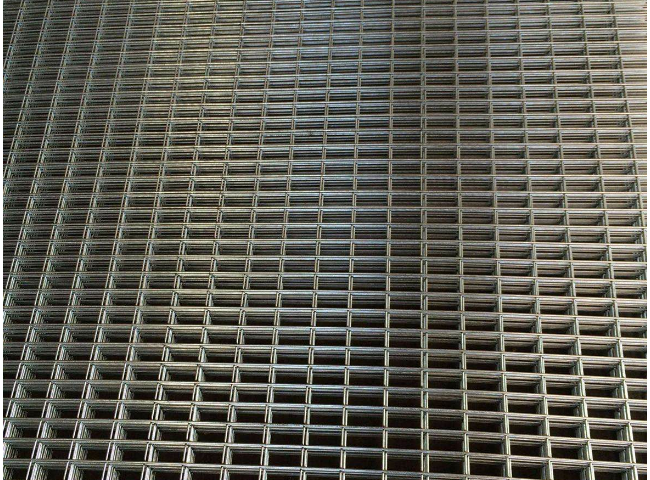
随着建筑工程技术的不断进步和基础设施建设的快速发展,钢筋作为建筑结构中不可或缺的基础材料,其加工质量和效率直接影响到整个工程的质量和进度。数控钢筋加工技术作为现代建筑工业化的重要组成部分,以其高效、精确、自动化等特点,在钢筋加工领域得到了广泛应用。冷加工钢筋加工过程中不需要高温加热,相比热轧工艺具有明显的节能环保优势。在双碳目标的大背景下,冷加工钢筋技术符合绿色发展的要求,有利于推动钢铁行业的可持续发展。随着科技的不断进步和建筑、机械、船舶等行业的快速发展,冷钢筋加工技术将呈现以下发展趋势:随着全球对环境保护的关注增加,钢筋行业也呈现出向绿色环保方向发展的趋势。未来,冷钢筋加工技术将更加注重节能减排和降低环境污染。钢筋加工是建筑施工中的一个重要环节,主要涉及钢筋的切割、弯曲和组装。浙江D12钢筋加工工艺
经验丰富的操作工人,能够熟练掌握热钢筋加工技巧,确保产品合格率。江苏板钢筋加工定制
数控(CNC)技术在钢筋加工中的应用,主要依赖于计算机数字程序控制技术。其重心原理是将设计好的钢筋加工图纸输入计算机,计算机根据图纸生成控制代码,然后通过数控设备将代码转换成机床能识别的指令信号,后面由数控机床按照指令信号进行加工和切割。这一过程实现了从图纸到加工的高度自动化和精确性。数控系统通常由硬件和软件两部分组成,硬件包括数控装置、伺服驱动系统、检测反馈装置等,软件则包括数控编程系统、图形仿真系统等。钢筋的力学性能、化学成分以及不同形状和尺寸对数控加工有着重要影响。在数控加工过程中,需要根据钢筋的材质特性和加工要求,选择合适的加工工艺和参数。例如,对于高强度钢筋,需要采用较大的弯曲力和较慢的弯曲速度,以确保加工质量。同时,还需要对钢筋进行预处理,如调直、除锈等,以提高加工效率和成品质量。江苏板钢筋加工定制
上一篇: 苏州D6钢筋加工供应商
下一篇: 虹口区数控钢筋加工供应