一体化活化设备生产过程
炭化终温和升温速率是炭化工艺控制的主要操作条件.炭化升温速率对炭化产物的产率有较大影响。高升温速率能使物料析出更多的焦油和煤气,降低炭化料产率。降低升温速率时,物料在低温区受热时间长,热解反应的选择性较强,初期热解使物料分子中较弱的键断开,发生了平行的和顺序的热缩聚反应,形成具有较高热稳定性的结构,从而减少高温阶段热解析出物的挥发分产率,获得更高的固体炭化产物(即炭化料)产率。炭化工艺中炭化料的质量主要通过挥发分、水容量和强度来进行评价。合格的炭化料的挥发分为12%-16%,水容量为15%-25%,球盘强度为90%.在使用产品活化设备前,确保设备处于正常工作状态。一体化活化设备生产过程
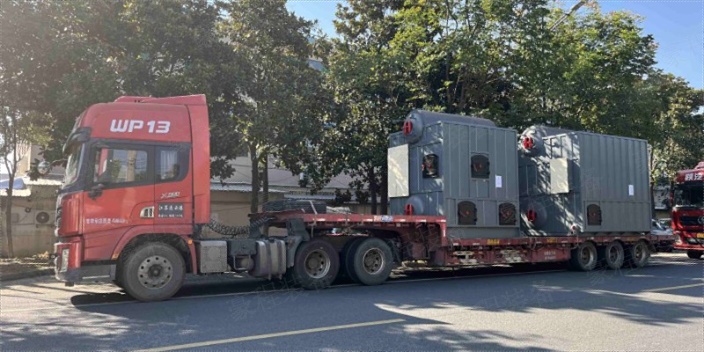
化学活化法是通过将化学试剂嵌入炭颗粒内部结构,经历一系列的交联缩聚反应形成微孔。化学活化可一步进行,即直接升温到 700℃左右进行活化。在活化前,先将活化剂水溶液与原料以一定比例浸渍一段时间,烘干后再放入惰性气氛中升温进行活化。活化剂与原料的浸渍比是影响活性炭性能的一个重要因素,因此可以通过控制浸渍比以及不同的活化温度来制备所需的活性炭。化学活化法制得的活性炭产率高,而且其孔隙结构比物理活化法更加发达。湖北省电活化设备生产过程拥有我们的活化设备,让您的生产线更加稳定、高效!
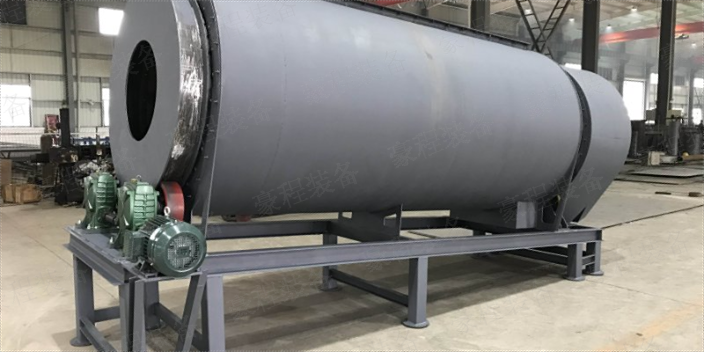
量需要一定时间,而在生产现场调试过程中常常需要根据炭化料质量迅速调节工艺参数,因此也可以通过感官对炭化料质量进行粗略评价。合格的炭化料应具有平整、无裂纹的表面,较高的强度,物料断面色泽一致。炭化尾气处理及利用余热产生蒸汽物料的炭化过程产生炭化尾气,其组成主要为两部分:一部分为炭化时外加燃料热源燃烧产生的高温加热气体,主要成分为CO2.H20,N2及少量的SO2和CO;另一部分为物料炭化热分解时所产生的挥发物组分,如CO,H2,CH4、烷烃、烯烃、焦油等。炭化尾气中含有少量有毒有害物质,这些气体直接排入大气将给周围环境造成污染,因此炭化尾气需要经过处理才能直接排入大气。
还原出的海绵铁经过回转冷却筒冷却到150℃排料。把混合的剩余碳和吸硫的石灰处理后,得到产品。回转窑海绵铁产量在1980年占直接还原铁的15%。中国曾于40年代初在四川綦江进行了日产10吨规模的海绵铁生产试验,金属化率可达90%以上,但因铁矿脉石无法分离,未能正常生产。把回转窑的出料温度提高到1250℃左右,固体料呈半熔化状态,已还原的铁滴在滚动中聚合成小的铁粒,出窑后水淬冷却可与脉石杂质磁选分离,得到粒铁。此法称为泰达回转窑粒铁法(Krupp-Renn法),它能处理选矿困难的贫铁矿。活化设备使用时,根据产品的要求,调整设备的工作时间和周期。
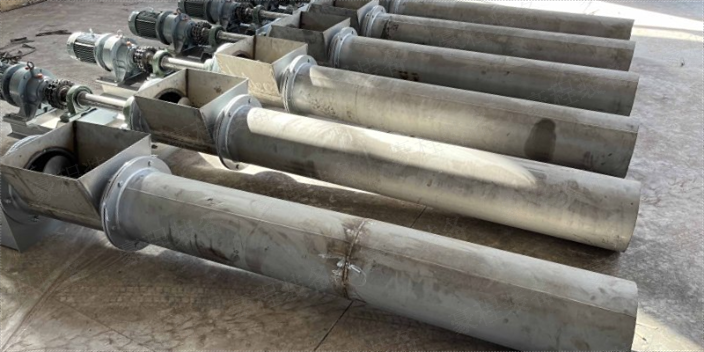
要使回转窑运转平稳,必须把大齿圈正确地安装在窑筒体上,齿圈的中心线应与窑体中心线同心,并尽量减少温度应力对它的影响。一般情况采用切线弹簧板连接。是切线弹簧板连接方式。切向安装的弹簧板的板厚为20~30毫米,一般有12—16块。一端用铆钉(焊接)安装在筒体上,另一端用螺栓固定在齿圈特有的凸缘2上。这种结构,使齿圈悬挂在窑体上,既能减少窑体本身弯曲对大齿圈和小齿轮啮合的影响,又能减轻开、停窑时大齿圈和小齿轮的撞击,使传动较为平稳。其缺点是大齿圈的制造和加工都较困难,安装时也不容易对中。切线弹簧板连接的另一种结构,它与前一种结构不同之处是弹簧板与齿圈用销钉连接。此种结构的齿圈,制造加工较方便,采用较多。另有纵向弹簧板连接方式,但在水泥回转窑中应用较少。活化设备使用后,注意设备的保养和维护,延长设备的使用寿命。山东自动化活化设备价格走势
活化设备使用后,及时清洁设备,保持设备的良好状态。一体化活化设备生产过程
回转窑具有物料输送功能作为输送设备,回转窑具有更大的潜力,因为物料在回转窑断面内的填充率、窑斜度和转速都很低。可以满足不同行业生产及输送的需要。 品质决定成败-回转窑窑内材料应精挑细选 一般回转窑窑内砌筑的耐火材料应有很好的耐火,耐高温,耐磨的特质,本篇泰达回转窑专业厂家分享回转窑砌筑耐火材料应如何精挑细选,首先,回转窑窑口用钢纤维增强刚玉质和高铝质耐火浇注料,在多年使用中易发生开裂剥落,即抗热震性不好,使用寿命较低。现在回转窑用耐火砖加以改善。一体化活化设备生产过程
上一篇: 北京活化设备什么价格
下一篇: 上海一体化活性炭设备有哪些