重庆低温球墨铸铁厂家直销
球墨铸铁,也称为球状石墨铸铁、球铁或奥贝球铁,是一种具有球状石墨结构的铸铁材料。它是通过在铸造过程中加入一定量的镁或稀土元素,使铸铁中的石墨形成球状结构而得名。球墨铸铁的主要特点是其球状石墨结构。球状石墨是由石墨片层形成的球状颗粒,与传统的片状石墨相比,具有更好的韧性和抗断裂性能。球状石墨的存在可以有效地阻碍裂纹的扩展,提高材料的强度和韧性。这使得球墨铸铁具有较高的抗冲击性能和抗疲劳性能,适用于一些需要承受冲击和振动负荷的工程应用。经过适当的热处理,球墨铸铁的性能还能进一步优化。 淬火和回火处理可以显著提高其硬度和耐磨性。重庆低温球墨铸铁厂家直销
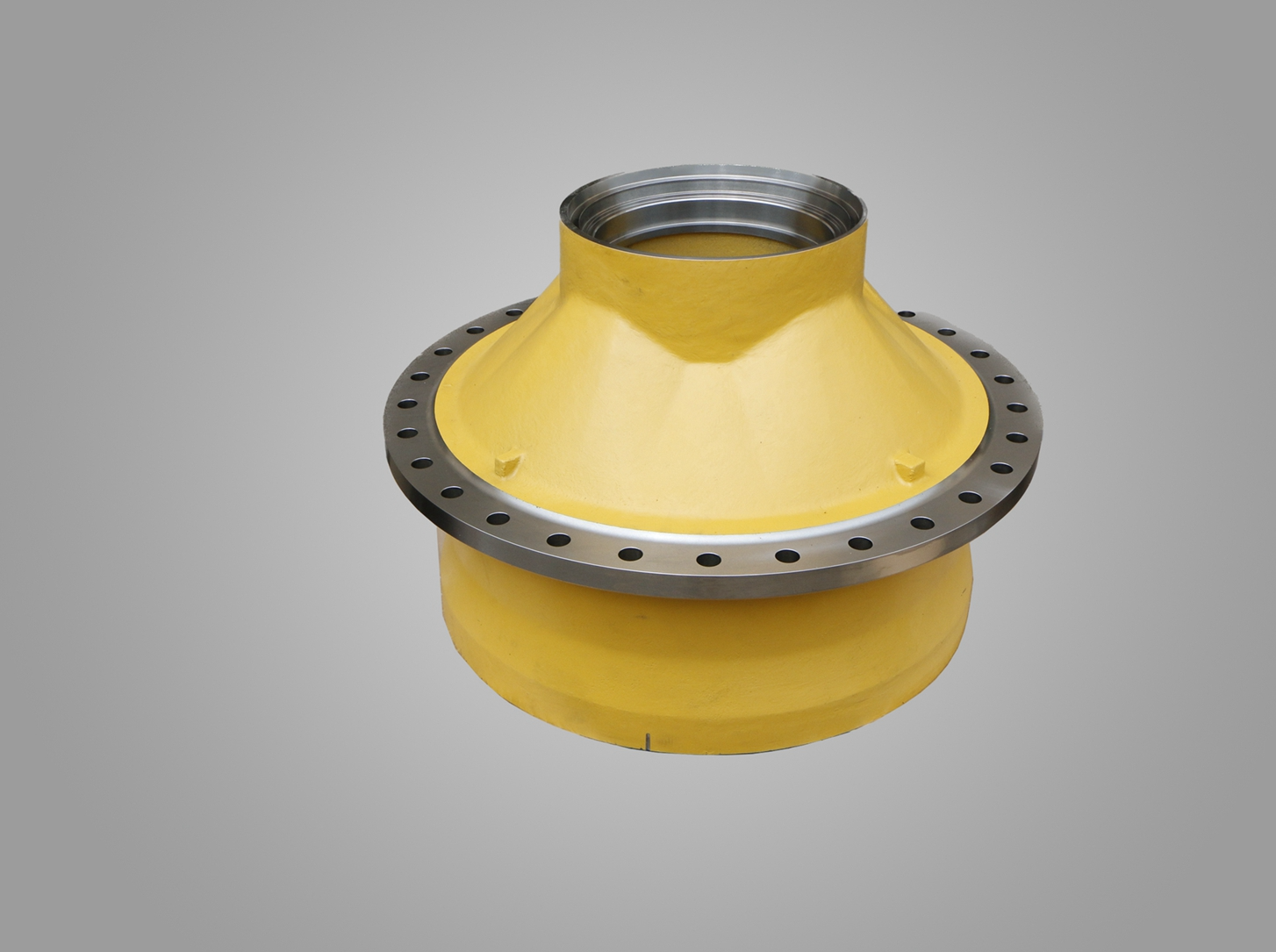
热处理是改善球墨铸铁性能的重要手段之一。常见的热处理方法包括退火、正火、淬火和回火等。退火处理主要用于获得铁素体基体的球墨铸铁,以提高其塑性和韧性。在退火过程中,将铸件加热到一定温度并保温一段时间,然后缓慢冷却。这样可以消除内应力,改善加工性能。正火处理则用于获得珠光体基体的球墨铸铁,提高其强度和硬度。正火时,将铸件加热到较高温度,然后在空气中冷却。淬火和回火处理可以进一步提高球墨铸铁的硬度和耐磨性。淬火是将铸件加热到奥氏体化温度后迅速冷却,使其形成马氏体组织;回火则是将淬火后的铸件加热到一定温度,以消除淬火应力,调整性能。例如,在制造机床导轨时,可以对球墨铸铁进行淬火和回火处理,提高其表面硬度和耐磨性,延长使用寿命。球墨铸铁供应商球墨铸铁具有良好的可加工性,满足不同的设计需求。
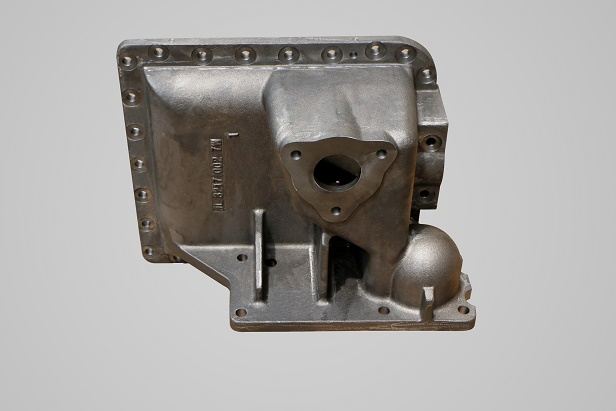
球墨铸铁的硬度通常在HB180-300之间,具体数值取决于球墨铸铁的成分、处理方式和热处理情况。球墨铸铁是一种铸铁材料,其主要成分是铁、碳和硅。球墨铸铁中的碳以球状形式存在,这使得球墨铸铁具有较高的韧性和抗冲击性。硬度是衡量材料抵抗外部力量的能力的指标之一。一般来说,球墨铸铁的硬度要高于普通铸铁。普通铸铁的硬度通常在HB150-230之间,而球墨铸铁的硬度通常在HB180-300之间。这是因为球墨铸铁中的球状碳颗粒比普通铸铁中的片状碳颗粒更有利于提高材料的硬度。需要注意的是,球墨铸铁的硬度可能会因具体的成分、处理方式和热处理情况而有所不同。在实际应用中,可以通过实验测量或参考相关的材料数据手册来获取更准确的硬度数值。此外,根据具体的应用需求,可以通过热处理等方式来调整球墨铸铁的硬度。
球墨铸铁凭借其优异的性能和广泛的应用,具有广阔的市场前景。随着汽车、机械制造等行业的不断发展,对高性能零部件的需求持续增长,为球墨铸铁提供了稳定的市场需求。在新兴领域,如新能源汽车、智能制造等,球墨铸铁也有着潜在的应用机会。例如,新能源汽车的电池包外壳、智能机器人的结构件等,都可以采用球墨铸铁制造。同时,全球基础设施建设的推进,也将带动球墨铸铁在市政工程、建筑等领域的应用。然而,市场竞争也日益激烈,球墨铸铁生产企业需要不断创新,提高产品质量和性能,降低成本,以适应市场的变化和需求。球墨铸铁的疲劳强度优于普通铸铁,适合用于承受交变载荷的部件。 例如桥梁的支座等结构件。
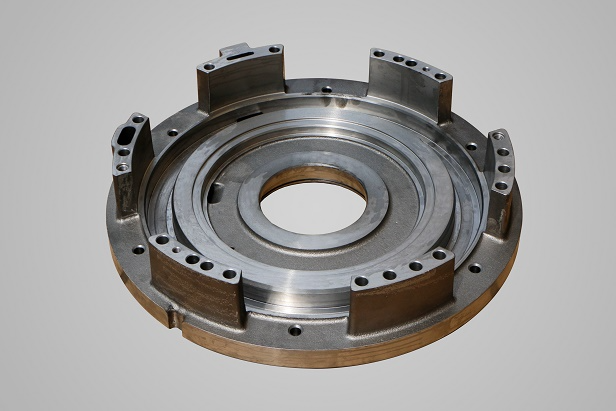
球墨铸铁的铸造工艺也有一定讲究。由于其流动性较差、收缩较大,因此需要较高的浇注温度及较大的浇注系统尺寸。合理应用冒口和冷铁,采用顺序凝固原则,有助于减少缩孔、缩松等缺陷的产生。为进一步提高球墨铸铁的性能,还可进行热处理。例如退火处理可得到铁素体基体,提高塑性、韧性,消除应力并改善切削性能;正火能获得珠光体基体,增强强度和耐磨性;调质则可获得回火索氏体的基体组织,具备良好的综合力学性能。球墨铸铁的发展并非一蹴而就。经过多年的研究和实践,人们对球化剂的成分、加入量以及处理工艺等不断优化,才使其性能逐步提升,应用范围不断扩大。球墨铸铁材质坚固,铸造工艺成熟,常用于制造复杂形状的零部件。安徽小批量球墨铸铁
球墨铸铁,强度高韧性好,广泛应用于机械制造等领域。重庆低温球墨铸铁厂家直销
为了获得高质量的球墨铸铁产品,在生产过程中有六大注意事项。首先要严格要求化学成分,使原铁液的碳硅含量高于灰铸铁,并降低其中锰、磷、硫的含量;其次,球墨铸铁液出炉温度应比灰铸铁更高;然后要进行球化处理,添加球化剂;接着加入孕育剂进行孕育处理;同时,因球墨铸铁流动性较差、收缩较大,需采用较高的浇注温度及较大的浇注系统尺寸,合理设置冒口和冷铁,并遵循顺序凝固原则;后面,还需进行相应的热处理。球墨铸铁的热处理方式多样,包括退火、正火、调质、等温淬火等。退火可得到铁素体基体,能提高塑性、韧性,消应力,改善切削性能;正火能得到珠光体基体,增强强度和耐磨性;调质可获得回火索氏体的基体结构,具备良好的综合力学性能,适用于如主轴、曲轴、连杆等部件;等温淬火则使外形复杂且综合性能要求高的零件获得下贝氏体的基体结构,拥有高硬度、高韧性等综合力学性能,可避免热处理时产生开裂,常用于如主轴、曲轴、齿轮等零件。重庆低温球墨铸铁厂家直销
上一篇: 安徽大型球墨铸铁报价
下一篇: 河南通用型球墨铸铁排行榜