辽宁重型低温球铁能锻造吗
低温球铁在石油、天然气、化工等领域的设备制造中得到普遍应用。在极寒地区的管道、阀门、压力容器等设备中,低温球铁能够有效提高设备的可靠性和安全性。低温球铁和普通球墨铸铁相比,具有更低的碳当量和更多的球状石墨。这使得低温球铁的抗蠕变性、抗疲劳性能和耐低温性都优于普通球墨铸铁,适用于更苛刻的工况。低温球铁具有良好的耐腐蚀性能,尤其在一些腐蚀性介质中表现出色。这使得它在化工、海洋等领域中用于制造耐腐蚀设备成为可行选择。低温球铁的焊接性能:低温球铁的焊接性能较好,可以采用常规的焊接方法进行连接和修复。这在使用过程中出现损坏或需要改装时非常有用。低温球铁的化学成分经过精心调配,以获得良好的低温综合性能。辽宁重型低温球铁能锻造吗
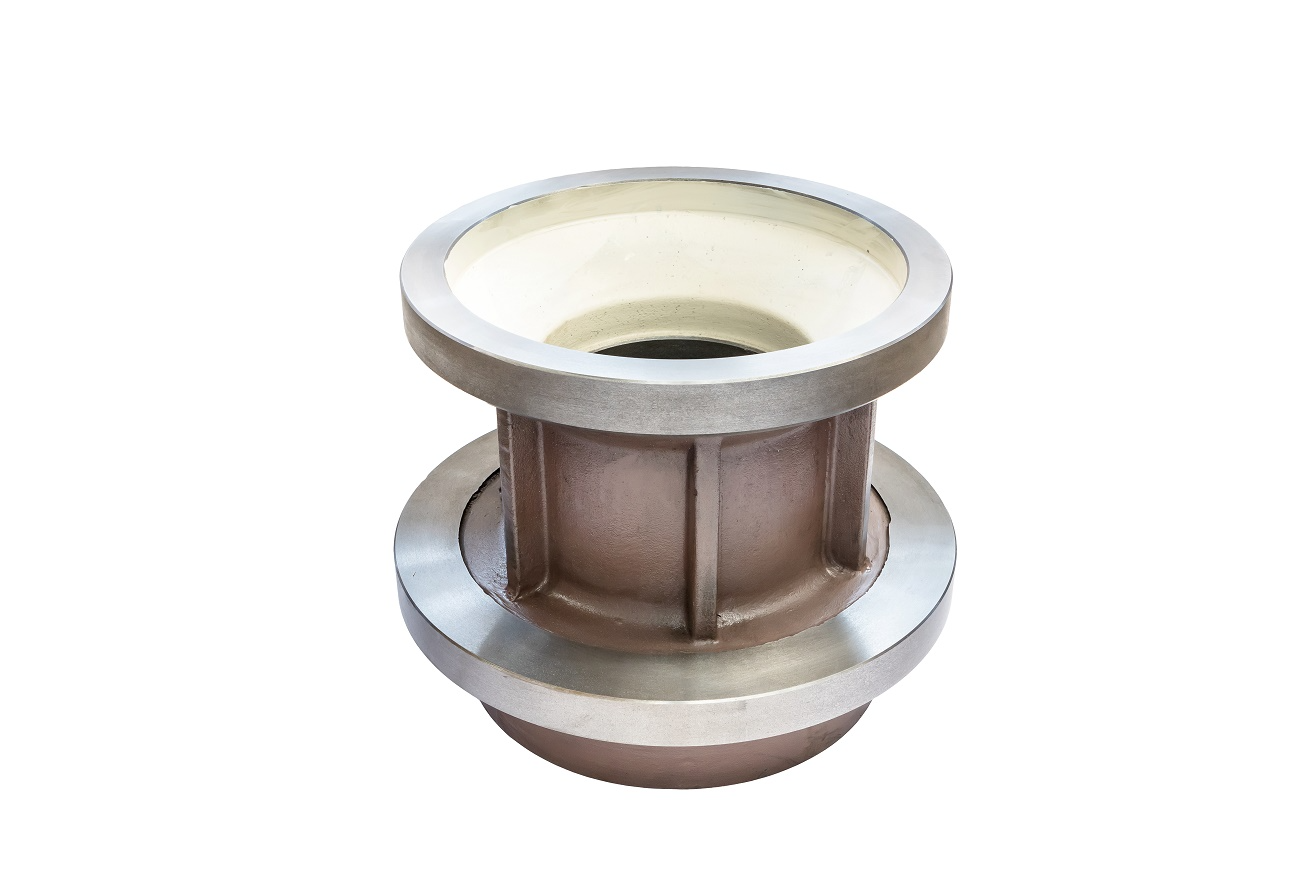
热处理工艺:适当的热处理工艺可以改善低温球铁的韧性。例如,通过淬火和回火等热处理工艺可以改变低温球铁的组织结构,减少渗碳体的含量,从而提高其韧性。添加合金元素:添加适量的合金元素可以改善低温球铁的韧性。例如,添加镍、铜等合金元素可以提高低温球铁的韧性。设计和使用注意事项:在设计和使用低温球铁制品时,需要考虑其韧性问题。例如,在受到冲击或振动的情况下,应尽量避免低温球铁制品发生塑性变形,以减少韧性破坏的风险。此外,可以采用其他材料或合金来替代低温球铁,以提高韧性。总的来说,低温球铁具有良好的韧性,这是由其组织结构、碳含量、热处理工艺和合金元素等因素所决定的。在使用低温球铁时,需要注意其韧性问题,并采取相应的措施来提高其韧性。广西低温球铁品牌低温球铁的强度和延展性在低温环境中得以保持,是其明显的优势之一。
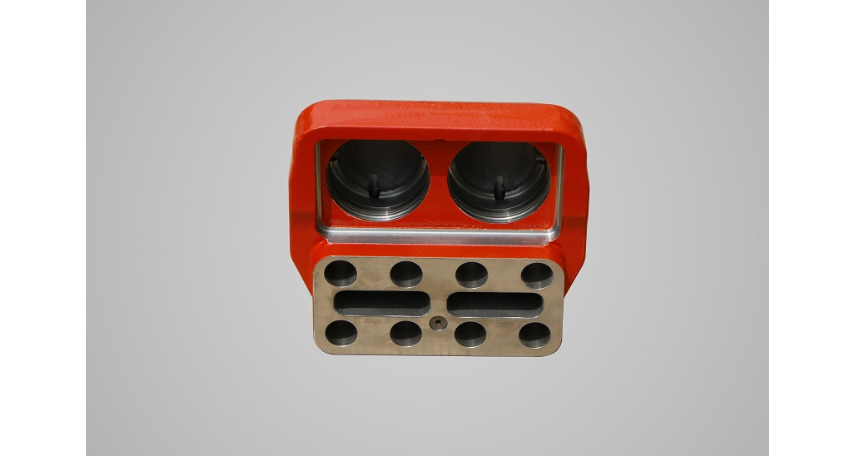
在低温环境下,低温球铁的组织结构会发生相变,使得其变得更加脆性。因此,在低温条件下使用低温球铁时需要特别注意其脆性问题。化学成分:低温球铁的化学成分也会对其脆性产生影响。例如,硅、磷等元素的含量过高会增加低温球铁的脆性。因此,在制备低温球铁时需要控制其化学成分,以减少脆性的发生。热处理工艺:适当的热处理工艺可以改善低温球铁的脆性问题。例如,通过淬火和回火等热处理工艺可以改变低温球铁的组织结构,减少渗碳体的含量,从而降低其脆性。设计和使用注意事项:在设计和使用低温球铁制品时,需要考虑其脆性问题。例如,在低温环境下,应尽量避免低温球铁制品受到冲击或振动,以减少脆性断裂的风险。此外,可以采用其他材料或合金来替代低温球铁,以降低脆性的影响。总的来说,低温球铁在低温环境下存在一定的脆性问题,这是由其组织结构、温度效应、化学成分等因素所决定的。在使用低温球铁时,需要注意其脆性问题,并采取相应的措施来减少脆性断裂的风险。
低温球铁的特殊热处理过程通常包括固溶退火、水淬和回火等步骤。在固溶退火阶段,将低温球铁加热到一定温度,使其成分均匀溶解,并消除内部应力。在固溶退火后,低温球铁需要迅速冷却,通常采用水淬的方法。水淬能够使材料迅速固化,形成高硬度的马氏体组织,并提高材料的强度和硬度。经过水淬后,低温球铁通常会出现过硬和脆化的问题。为了解决这个问题,需要进行回火处理。回火是将材料加热到一定温度,持续一段时间后冷却,目的是降低材料的硬度和脆性,提高其韧性和塑性。回火过程中,温度和时间的选择将根据材料的具体要求来确定。高温回火能够使材料中的残余应力得到释放,提高其韧性和抗冲击性能。而低温回火则能够获得更高的硬度和耐磨性。低温球铁的铸造工艺要求严格,以确保其出色的低温特性。
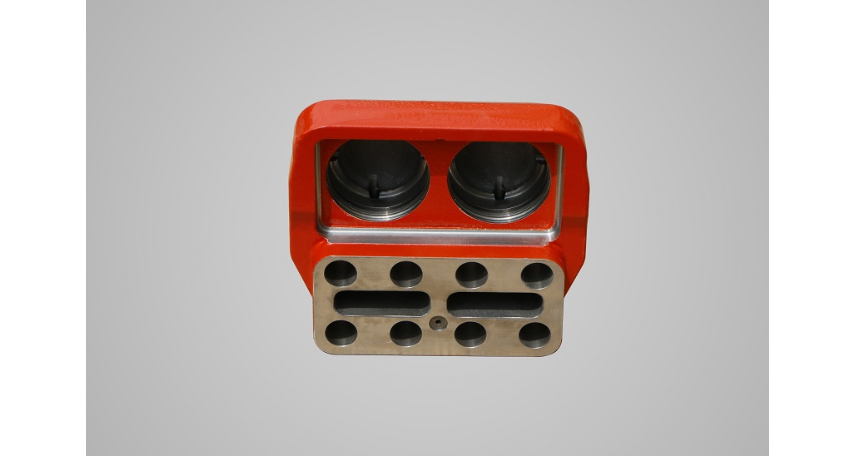
低温球铁特殊热处理过程中的回火阶段是为了调控材料的硬度和韧性。适当的回火温度和时间可以提高材料的韧性,降低脆性,从而提高低温球铁的可靠性。低温球铁特殊热处理过程对低温球铁的组织结构有着明显影响。通过控制处理温度和时间,可以得到细小的马氏体组织和均匀的碳化物分布,从而提高材料的耐磨性和疲劳强度。低温球铁特殊热处理过程中的温度梯度对低温球铁的相变行为有重要影响。较大的温度梯度能够促使相变快速进行,形成致密的马氏体组织,提高材料的硬度和强度。相比普通球铁,低温球铁在抵御低温脆性断裂方面有着明显的进步。上海通用型低温球铁厂
随着对低温球铁研究的深入,其在更多低温相关产业中的应用前景十分广阔。辽宁重型低温球铁能锻造吗
这些表面处理技术可以在低温球铁的表面形成一层耐腐蚀的保护层,提高其耐腐蚀性能。环境适应性:低温球铁具有较好的环境适应性,能够适应多种腐蚀性环境。它可以在酸性、碱性、盐性等各种腐蚀介质中工作,具有较广泛的应用范围。总的来说,低温球铁具有较好的耐腐蚀性能,这得益于球墨铸铁的基础特性、合金元素的添加、热处理工艺的优化、表面处理技术的应用以及其自身的环境适应性。低温球铁的耐腐蚀性使其在化工、石油、海洋工程等领域中得到广泛应用,为各种设备提供了可靠的耐腐蚀保护。辽宁重型低温球铁能锻造吗
上一篇: 江苏通用型低温球铁品牌
下一篇: 广州小批量低温球铁排名