横沥表面电解抛光方法
不锈钢电解抛光工艺是一种常用的表面处理方法,用于提高不锈钢制品的光洁度和美观度。该工艺通过电解作用,将不锈钢表面的氧化物和杂质去除,使其表面光滑、亮丽。不锈钢电解抛光工艺需要一定的设备和材料。通常,一个电解抛光系统包括电解槽、电源、阳极和阴极等组成部分。电解槽是用来容纳电解液的容器,电源则提供所需的电流。阳极和阴极则分别连接到电源的正负极,用来完成电解过程。在进行不锈钢电解抛光之前,首先需要对不锈钢制品进行清洗,以去除表面的油污和杂质。将清洗后的不锈钢制品放入电解槽中,确保其与阳极和阴极之间有一定的距离。接下来,将电解液注入电解槽中,通常使用的电解液是硫酸和硝酸的混合物。一旦电解槽准备就绪,开始施加电流。电流的大小和时间的长短取决于不锈钢制品的尺寸和要求的抛光效果。不锈钢电解抛光是一种先进的表面处理技术,能够赋予产品的表面质量和持久的光泽。横沥表面电解抛光方法
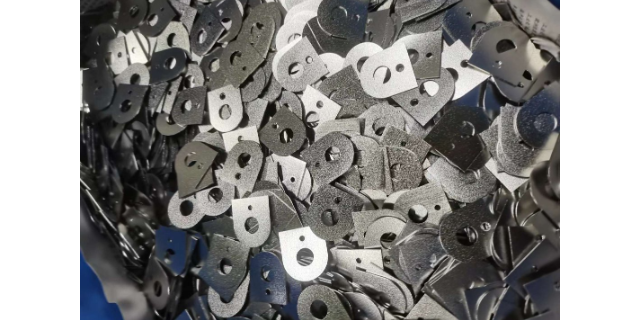
提高硬度:经过电解处理后,不锈钢表面的硬度会有所上升,使其更加坚固,不易受到外来冲击、刮擦等因素的损害。这有助于提高产品的性能表现和可靠性。环保可持续:不锈钢电解技术使用环保型电解液,减少了废液处理和环境污染的问题。这种可持续的生产方式符合现代商业发展的趋势,为企业树立了绿色、环保的形象。综上所述,不锈钢电解可以解决表面质量、耐腐蚀性、降低摩擦系数、修复表面缺陷、提高硬度以及环保可持续等问题。这些问题的解决使得不锈钢电解技术在各个行业中得到了广泛的应用,并为企业创造了更多的商业机会和价值。肇庆304不锈钢电解抛光加工工艺不锈钢电解抛光过程中,电流密度、电解液温度和抛光时间等参数的控制至关重要。
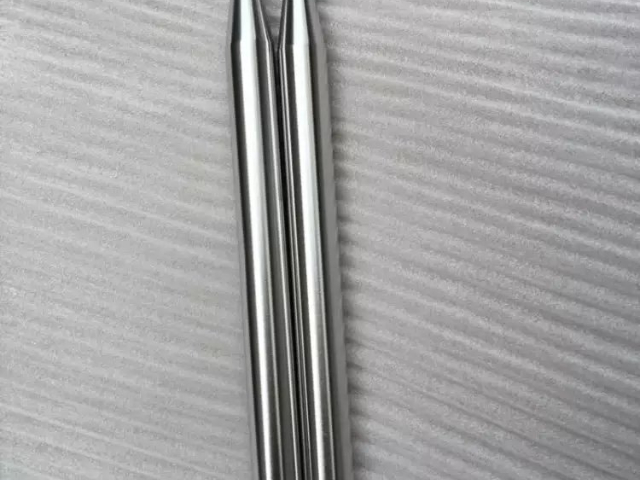
酸洗:将金属放入酸洗液中,去除表面的氧化层和锈蚀。酸洗时间约为5-10分钟,温度控制在20-40℃。这一步骤可根据工件实际情况选择是否进行。如氧化皮或焊斑较为严重,酸洗可去除,为后续的电解抛光打下良好的基础。水洗:用清水将酸洗液冲洗干净,确保无残留物。清洗时间约为2-3分钟,常温下进行。电解抛光:将金属作为阳极放入电解抛光液中,施加电流进行抛光处理。抛光时间根据实际需求而定,一般为3-15分钟,温度控制在40-60℃。水洗:用清水将电解抛光液冲洗干净,确保无残留物。清洗时间约为2-3分钟,常温下进行。干燥:采用烘干或吹干,将表面残留水分处理干净,确保表面干燥。
不锈钢电解抛光需要专业设备和技术,成本较高,对操作人员的要求也较高。相比之下,传统机械抛光是一种通过机械力和磨料对不锈钢表面进行磨削和抛光的方法。它通常使用砂轮、砂纸等磨料材料,通过旋转或摩擦的方式对不锈钢表面进行加工。传统机械抛光的优点是设备简单、成本低廉,操作相对容易。同时,传统机械抛光也可以适应不同的表面形状和尺寸,具有较大的灵活性。然而,传统机械抛光需要较长的加工时间,而且容易产生划痕和不均匀的表面效果。综上所述,不锈钢电解抛光和传统机械抛光各有优劣。不锈钢电解抛光具有高效、快速、可控的特点,适用于对表面质量要求较高的场合,但需要专业设备和技术。传统机械抛光设备简单、成本低廉,适用于一般要求的表面处理,但加工时间较长且容易产生划痕。在未来,不锈钢电解抛光技术的应用前景将更加广阔,为工业生产和表面处理行业带来更多的机遇和发展空间。
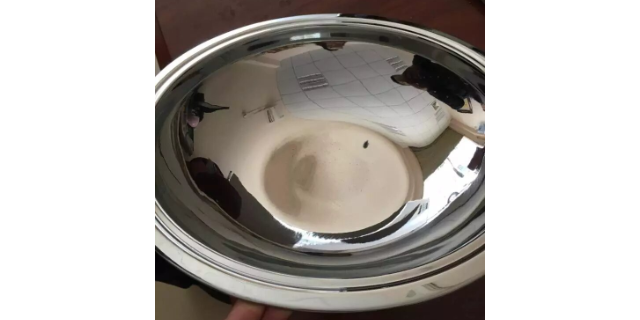
自动化程度高:电解抛光工艺可以实现自动化生产,减少了人工干预和操作失误的可能性。通过引入智能化技术和设备,可以实现电解抛光过程的实时监控和调整,提高生产效率和产品质量。二、电解抛光工艺的应用不锈钢制品:电解抛光在不锈钢制品的表面处理中广泛应用。通过去除不锈钢表面的氧化层和划痕等缺陷,可以提高其表面质量和美观度,延长产品使用寿命。适用于医疗器械、餐具、装饰品等领域。铜制品:电解抛光在铜制品的表面处理中也具有重要意义。铜制品在长期使用过程中容易氧化变色,通过电解抛光可以恢复其原有的光泽和美观度。此外,电解抛光还可以提高铜制品的表面硬度和耐磨性能,适用于雕塑、艺术品等领域不锈钢电解抛光后表面的硬度和耐磨性得到显著提高,延长了产品的使用寿命。江门不锈电解抛光原理
在医疗、航空、食品等行业,不锈钢电解抛光技术的应用尤为重要,可确保产品的卫生安全和可靠性。横沥表面电解抛光方法
在电解抛光完成后,需要对不锈钢制品进行中和处理,以去除电解液残留和中和电解液的酸碱度。可以使用中和剂进行处理,同时进行冲洗,确保表面干净。将抛光完成的不锈钢制品进行清洗,去除中和剂和残留的电解液。可以使用清水进行冲洗,也可以使用酒精进行擦拭,确保表面干净。然后将制品进行干燥,可以通过自然风干或者烘干的方式进行。通过以上的工艺流程,不锈钢电解抛光可以提高不锈钢制品的光洁度和美观度。同时,还可以去除表面的氧化物和污染物,提高不锈钢制品的耐腐蚀性能。横沥表面电解抛光方法
上一篇: 江门不锈电解抛光多少钱
下一篇: 江门医疗器械电解抛光设备