机械QPQ替代气体渗氮
气体渗氮是在含有活性氮、碳原子的气氛中进行低温氮、碳共渗从而获得以氮为主的氮碳共渗层。气体氮化的常用温度为560-570℃,在该温度下氮化层硬度值高,氮化时间通常为2-3h,随着时间延长,氮化层深度增加缓慢。相较于QPQ处理工艺,虽然气体渗氮在耐磨性方面表现良好,但是它的生产周期太长,且必须采用特殊的渗氮钢,表面生成的Fe2N相脆性较大。工研所QPQ技术成产周期短,适用钢种广,且表面生成韧性较高的Fe2~3N相,同时由于工件几乎不变形,处理后不必进行磨加工。特别是原来以抗蚀为目的的气体渗氮,采用工研所QPQ技术以后,耐蚀性会有很大提高。QPQ表面处理可以减少刀具的摩擦系数,提高切削效率。机械QPQ替代气体渗氮
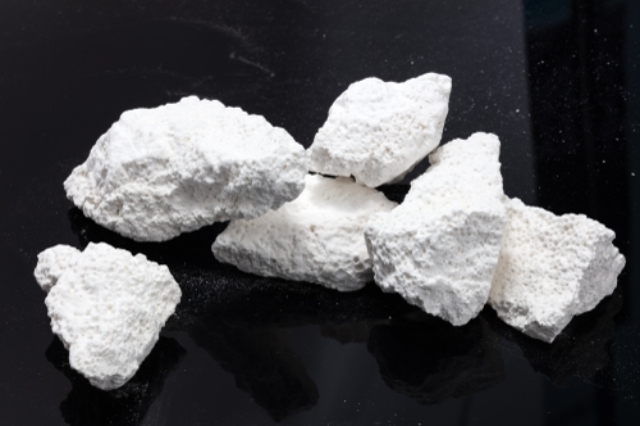
在汽车发动机中,活塞杆是连接活塞和曲轴的关键部位,它承受着活塞往复运动时的巨大力量,并将这些力量转化为旋转动力,驱动汽车前进,因此,它要求有较高的耐磨性和良好的耐蚀性。原来一般采用镀硬铬来增加表面的耐蚀性和耐磨性,但是镀铬的六价铬离子严重污染环境,因此采用环保的工研所QPQ工艺方法,其耐磨性比镀硬铬高2倍,耐蚀性比镀硬铬高20倍,同时通过盐雾试验发现工研所QPQ处理后的活塞杆具有良好的耐蚀性,因此可以用工研所QPQ技术代替镀硬铬。表面改性QPQ磨损量成都工具研究所有限公司利用QPQ表面处理技术,使刀具具有更好的切削稳定性。
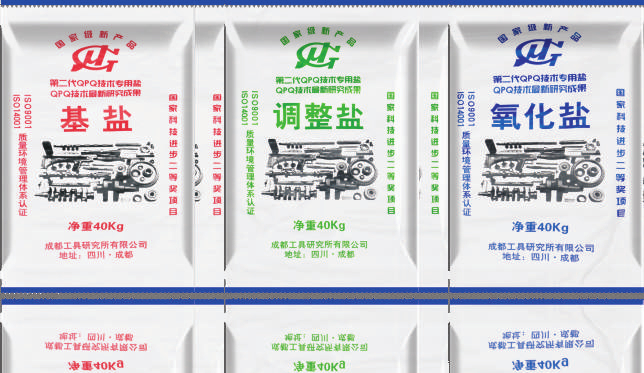
经由工研所的QPQ表面复合处理技术处理后的产品形成的氮化层具有优异的硬度和耐磨性,能有效延长零部件的使用寿命,表面形成致密的氮化层,提供了优异的抗腐蚀性能,适用于恶劣环境下的使用。QPQ处理不仅提高了表面硬度,还有助于改善材料的疲劳强度和耐久性、保持尺寸稳定,与其他表面处理方法相比,QPQ处理对零部件尺寸变化的影响较小,有利于保持高精度要求。相对于其他表面处理方法,QPQ处理的成本相对较低,同时提供了更长的使用寿命,节约了维护和更换成本。QPQ处理过程中不涉及有毒化学物质,减少了对环境的影响,符合环保要求。适用于多种金属材料,如钢铁、铝合金等,可广泛应用于汽车、机械制造等领域。
45钢为碳素结构用钢,硬度不高易切削加工,模具中常用来做模板、梢子、导柱等,但须热处理。45钢本身的硬度大概在197HV左右,工研所常规QPQ处理后硬度值为650HV,深层QPQ处理后的硬度值可达1000HV,45钢本身易生锈,常规QPQ处理后的平均生锈时间是85.3h,深层QPQ处理后的生锈时间延长至151.3h。所以45钢经过工研所QPQ技术处理后,特别是深层QPQ处理后,试样可以获得较高的表面硬度和良好的表面渗氮组织,同时试样具有良好的耐磨性,在较低载荷的试验条件下,随着载荷的增加试样的摩擦系数可以保持一定的稳定性。QPQ表面处理可以使刀具具有更高的切削精度。
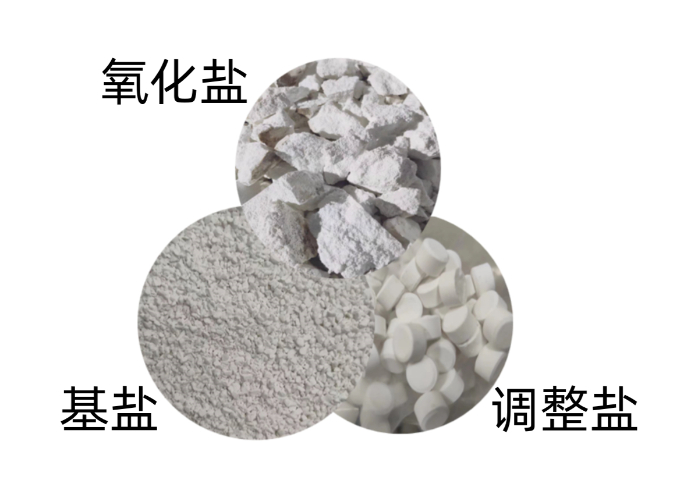
在工研所QPQ技术的日常生产中,QPQ盐的质量对工件表面的化合物层特性,包括深度、硬度以及疏松级别,具有至关重要的影响。其中,基盐中的氰酸根浓度是一个关键指标,其精确控制是QPQ技术质量控制流程中的重要环节。为了准确检测并调整基盐中的氰酸根含量,经典的甲醛定氮法被广泛应用。这一方法需要精心配制甲基红和亚甲基蓝的混合指示剂,以确保在加入酸碱时能够精确控制反应进程。随后,通过加入过量的甲醛,溶液中的氨态氮会被转化为氢离子。在酚酞指示剂的作用下,利用氢氧化钠对转化后的氢离子进行滴定。通过记录滴定过程中消耗的氢氧化钠量,可以精确地推算出基盐中氰酸根的浓度。这一检测与调整过程不仅确保了QPQ处理中盐的质量,也为工件表面形成高质量化合物层提供了有力保障,从而进一步提升了工件的整体性能和使用寿命。QPQ表面处理可以显著提高刀具的切削性能和加工效率。石家庄QPQ
QPQ表面处理可以提高刀具的抗疲劳性能。机械QPQ替代气体渗氮
齿轮在各类机械设备中的使用过程中,常常面临着重载荷、高磨损以及高疲劳的严苛服役特性。这些特性要求齿轮材料必须具备良好的高韧性、高耐磨性和高疲劳强度,以确保其长期稳定运行。经过工研所QPQ表面符合处理技术的处理后,齿轮样件的表面会形成一层由氮化物、碳化物及氧化物组成的混合强化层。这一强化层不仅明显提升了零构件的表面硬度、耐磨性和耐蚀性,而且能够保留芯部原有的良好韧性。更为可贵的是,经过QPQ处理的工件几乎不会发生变形,从而确保了齿轮在复杂工况下的高精度和可靠性。机械QPQ替代气体渗氮