多功能半导体封装载体欢迎选购
功能性半导体封装载体的设计与制造研究是指在半导体封装领域,针对特定功能需求,研究和开发具有特定功能的封装载体,并进行相关制造工艺的研究。
1. 功能集成设计:根据特定功能的要求,设计封装载体中的功能单元、传感器、天线等,实现系统级集成,并与封装载体相连接。
2. 多功能性材料研究:研究和使用具有多功能性能的材料,如高导热材料、低介电常数材料、光学材料等,以满足封装载体在不同功能下的要求。
3. 高性能封装工艺研究:开发适合特定功能要求的封装工艺,并优化工艺参数、工艺流程等,以实现高性能的功能性封装载体。
4. 集成电路与器件优化设计:结合封装载体的具体功能需求,优化集成电路和器件的设计,以实现更好的系统性能和可靠性。
5. 制造工艺控制与质量验证:通过制造工艺的优化和控制,确保功能性封装载体的质量和稳定性。进行相关测试和验证,验证载体的功能性能和可靠性。
功能性半导体封装载体的设计与制造研究对于满足特定功能需求的封装载体的发展具有重要意义。需要综合考虑功能集成设计、多功能性材料研究、高性能封装工艺研究、集成电路与器件优化设计、制造工艺控制与质量验证等方面,进行综合性的研究与开发,以实现功能性封装载体的设计与制造。 蚀刻技术如何实现半导体封装中的微米级加工!多功能半导体封装载体欢迎选购
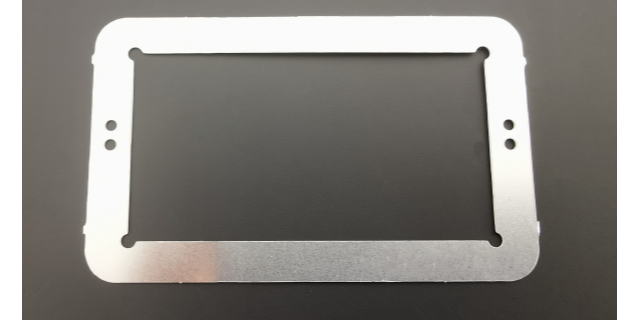
蚀刻技术在半导体封装中用于调控微观结构是非常重要的。下面是一些常用的微观结构调控方法:
蚀刻选择性:蚀刻选择性是指在蚀刻过程中选择性地去除特定的材料。通过调整蚀刻液的成分、浓度、温度和时间等参数,可以实现对特定材料的选择性蚀刻。这样可以在半导体封装中实现微观结构的调控,如开孔、通孔和刻蚀坑等。
掩模技术:掩模技术是通过在待蚀刻的表面上覆盖一层掩膜或掩膜图案来控制蚀刻区域。掩膜可以是光刻胶、金属膜或其他材料。通过光刻工艺制备精细的掩膜图案,可以实现对微观结构的精确定位和形状控制。
物理辅助蚀刻技术:物理辅助蚀刻技术是指在蚀刻过程中通过物理机制来辅助蚀刻过程,从而实现微观结构的调控。例如,通过施加外加电场、磁场或机械力,可以改变蚀刻动力学,达到所需的结构调控效果。
温度控制:蚀刻过程中的温度控制也是微观结构调控的重要因素。通过调整蚀刻液的温度,可以影响蚀刻动力学和表面反应速率,从而实现微观结构的调控。
需要注意的是,在进行微观结构调控时,需要综合考虑多种因素,如蚀刻液的成分和浓度、蚀刻时间、温度、压力等。同时,还需要对蚀刻过程进行严密的控制和监测,以确保所得到的微观结构符合预期要求。 辽宁半导体封装载体私人定做蚀刻技术为半导体封装带来更高的集成度!
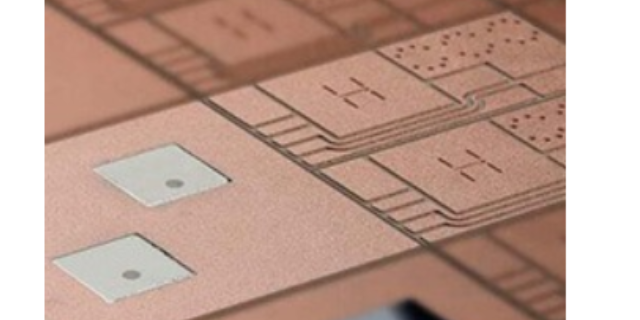
蚀刻工艺在半导体封装器件中的使用可能会对介电特性产生一定影响,具体影响因素包括材料选择、蚀刻剂和蚀刻条件等。
1. 材料选择对介电特性的影响:不同材料的介电特性会受到蚀刻工艺的影响。例如,蚀刻过程中可能引入表面缺陷或氧化层,对材料的介电常数和介电损耗产生影响。因此,研究不同材料的蚀刻工艺对介电特性的影响是重要的。
2. 蚀刻剂和蚀刻条件对介电特性的影响:蚀刻剂的选择和蚀刻条件会直接影响蚀刻过程中的表面形貌和化学成分,从而影响材料的介电特性。研究不同蚀刻剂和蚀刻条件对介电特性的影响,可以为优化蚀刻工艺提供指导。
3. 蚀刻工艺对绝缘材料界面和界面态的影响:在封装器件中,绝缘材料常常扮演重要角色。蚀刻工艺可能引入界面态或改变绝缘材料界面的结构和化学成分,从而影响介电特性。
4. 蚀刻工艺对介电层表面质量的影响:在封装器件中,常常涉及介电层的制备和加工。蚀刻工艺可能影响介电层的表面质量,例如引入表面粗糙度或缺陷。
综上所述,研究蚀刻工艺对半导体封装器件介电特性的影响,需要考虑材料选择、蚀刻剂和蚀刻条件、绝缘材料界面和界面态以及介电层表面质量等因素。这些研究有助于优化蚀刻工艺,提高封装器件的介电性能。
蚀刻技术在半导体封装中的后续工艺优化研究主要关注如何优化蚀刻工艺,以提高封装的制造质量和性能。
首先,需要研究蚀刻过程中的工艺参数对封装质量的影响。蚀刻剂的浓度、温度、蚀刻时间等参数都会对封装质量产生影响,如材料去除速率、表面粗糙度、尺寸控制等。
其次,需要考虑蚀刻过程对封装材料性能的影响。蚀刻过程中的化学溶液或蚀刻剂可能会对封装材料产生损伤或腐蚀,影响封装的可靠性和寿命。可以选择适合的蚀刻剂、优化蚀刻工艺参数,以减少材料损伤。
此外,还可以研究蚀刻后的封装材料表面处理技术。蚀刻后的封装材料表面可能存在粗糙度、异物等问题,影响封装的光学、电学或热学性能。研究表面处理技术,如抛光、蚀刻剂残留物清洁、表面涂层等,可以改善封装材料表面的质量和光学性能。
在研究蚀刻技术的后续工艺优化时,还需要考虑制造过程中的可重复性和一致性。需要确保蚀刻过程在不同的批次和条件下能够产生一致的结果,以提高封装制造的效率和稳定性。
总之,蚀刻技术在半导体封装中的后续工艺优化研究需要综合考虑蚀刻工艺参数、对材料性质的影响、表面处理技术等多个方面。通过实验、优化算法和制造工艺控制等手段,实现高质量、可靠性和一致性的封装制造。 蚀刻技术如何保证半导体封装的一致性!
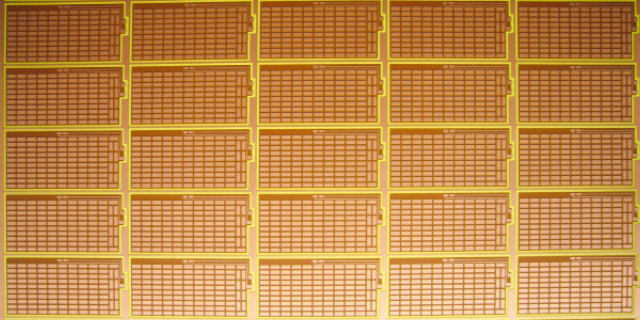
蚀刻是一种制造过程,通过将物质从一个固体材料表面移除来创造出所需的形状和结构。在三维集成封装中,蚀刻可以应用于多个方面,并且面临着一些挑战。
应用:模具制造:蚀刻可以用于制造三维集成封装所需的模具。通过蚀刻,可以以高精度和复杂的结构制造出模具,以满足集成封装的需求。管理散热:在三维集成封装中,散热是一个重要的问题。蚀刻可以用于制造散热器,蚀刻在三维集成封装中的应用与挑战是一个值得探索的领域。
在应用蚀刻技术的同时,也面临着一些挑战。
挑战:首先,蚀刻技术的精确性是一个重要的挑战。因为三维集成封装中的微细结构非常小,所以需要实现精确的蚀刻加工。这涉及到蚀刻工艺的优化和控制,以确保得到设计要求的精确结构。其次,蚀刻过程中可能会产生一些不良影响,如侵蚀和残留物。这可能会对电路板的性能和可靠性产生负面影响。因此,需要开发新的蚀刻工艺和处理方法,以避免这些问题的发生。蚀刻技术还需要与其他工艺相互配合,如电镀和蚀刻后的清洗等。这要求工艺之间的协调和一体化,以确保整个制造过程的质量与效率。
综上所述,只有通过不断地研究和创新,克服这些挑战,才能进一步推动蚀刻技术在三维集成封装中的应用。 新一代封装技术对半导体产业的影响和前景。高科技半导体封装载体联系方式
蚀刻技术推动半导体封装的小型化和轻量化!多功能半导体封装载体欢迎选购
基于蚀刻工艺的半导体封装裂纹与失效机制分析主要研究在蚀刻过程中,可能导致半导体封装结构产生裂纹和失效的原因和机制。
首先,需要分析蚀刻工艺对封装材料的影响。蚀刻过程中使用的化学溶液和蚀刻剂具有一定的腐蚀性,可能对封装材料造成损伤。通过实验和测试,可以评估不同蚀刻工艺对封装材料的腐蚀性能,并分析产生裂纹的潜在原因。
其次,需要考虑封装材料的物理和力学性质。不同材料具有不同的硬度、弹性模量、热膨胀系数等特性,这些特性对蚀刻过程中产生裂纹起到重要的影响。通过材料力学性能测试等手段,可以获取材料性质数据,并结合蚀刻过程的物理参数,如温度和压力,分析裂纹产生的潜在原因。
此外,封装结构的设计和制造过程也会对蚀刻裂纹产生起到关键作用。例如,封装结构的几何形状、厚度不一致性、残余应力等因素,都可能导致在蚀刻过程中产生裂纹。通过对封装结构设计和制造过程的分析,可以发现蚀刻裂纹产生的潜在缺陷和问题。
在分析裂纹与失效机制时,还需要进行显微结构观察和断口分析。通过显微镜观察和断口分析可以获得蚀刻裂纹的形貌、尺寸和分布,进而推断出导致裂纹失效的具体机制,如应力集中、界面剪切等。
多功能半导体封装载体欢迎选购
上一篇: 大规模半导体封装载体金属
下一篇: 新时代VCM弹片私人定做