河南系统级封装
此外,在电源、车载通讯方面也开始进行了 SiP 探索和开发实践。随着电子硬件不断演进,过去产品的成本随着电子硬件不断演进,性能优势面临发展瓶颈,而先进的半导体封装技术不只可以增加功能、提升产品价值,还有效降低成本。SiP 兼具低成本、低功耗、高性能、小型化和多元化的优势。2021 年,全球 SiP 市场规模约为 150 亿美元;预计 2021-2026 年,全球 SiP 市场年均复合增长率将在 5.8% 左右,到 2026 年市场规模将达到 199 亿美元左右。受益于人工智能、物联网、5G 等产业快速发展,预计未来 5 年,可穿戴智能设备、IoT 物联网设备将会是推动全球 SiP 市场增长的重要动力。目前全世界封装的产值只占集成电路总值的 10%,当 SiP 技术被封装企业掌握后,产业格局就要开始调整,封装业的产值将会出现一个跳跃式的提高。SiP 在应用终端产品领域(智能手表、TWS、手机、穿戴式产品、5G 模组、AI 模组、智能汽车)的爆发点也将愈来愈近。SiP封装是将多个半导体及一些必要的辅助零件,做成一个相对单独的产品。河南系统级封装
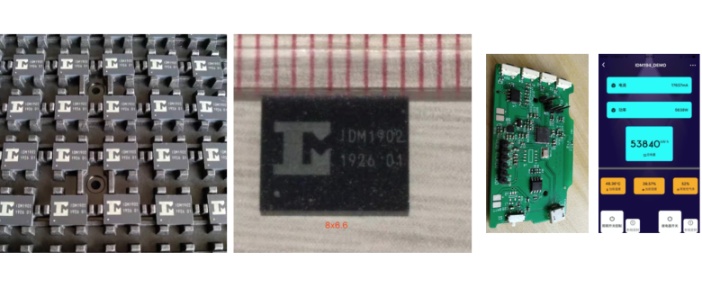
系统级封装(SiP)是将多个集成电路(IC)和无源元件捆绑到单个封装中,在单个封装下它们协同工作的方法。这与片上系统(SoC)形成鲜明对比,功能则集成到同一个芯片中。将基于各种工艺节点(CMOS,SiGe,BiCMOS)的不同电路的硅芯片可以垂直或并排堆叠在衬底上。该封装由内部接线进行连接,将所有芯片连接在一起形成一个功能系统。系统级封装类似于片上系统(SOC),但它的集成度较低,并且使用的不是单一半导体制造工艺。常见的SiP解决方案可以利用多种封装技术,例如倒装芯片、引线键合、晶圆级封装等。封装在系统中的集成电路和其他组件的数量可变,理论上是无限的,因此,工程师基本上可以将整个系统集成到单个封装中。江苏COB封装供应SiP是使用成熟的组装和互连技术,把各种集成电路器件集成到一个封装体内,实现整机系统的功能。
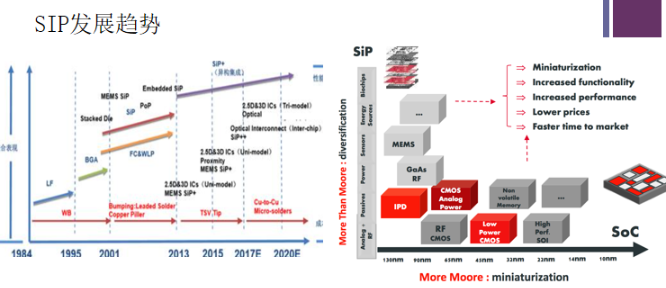
PiP封装的优点:1)外形高度较低;2)可以采用标准的SMT电路板装配工艺;3)单个器件的装配成本较低。PiP封装的局限性:(1)由于在封装之前单个芯片不可以单独测试,所以总成本会高(封装良率问题);(2)事先需要确定存储器结构,器件只能有设计服务公司决定,没有终端使用者选择的自由。TSV,W2W的堆叠是将完成扩散的晶圆研磨成薄片,逐层堆叠而成。层与层之间通过直径在10µm以下的细微通孔而实现连接。此种技术称为TSV(Through silicon via)。与常见IC封装的引线键合或凸点键合技术不同,TSV能够使芯片在三维方向堆叠的密度更大、外形尺寸更小,并且较大程度上改善芯片速度和降低功耗,成为3D芯片新的发展方向。
SiP是使用成熟的组装和互连技术,把各种集成电路器件(IC、MOS等)以及各类无源元件如电阻、电容等集成到一个封装体内,实现整机系统的功能。由于SiP电子产品向高密度集成、功能多样化、小尺寸等方向发展,传统的失效分析方法已不能完全适应当前技术发展的需要。为了满足SiP产品的失效分析,实现内部互连结构和芯片内部结构中失效点的定位,分析技术必须向高空间分辨率、高电热测试灵敏度以及高频率的方向发展。典型的SiP延用COB工艺,将电路板的主要器件塑封(COB),再把COB器件以元器件贴片到FPC软板上。据报告,2022年,SiP系统级封装市场总收入达到212亿美元。
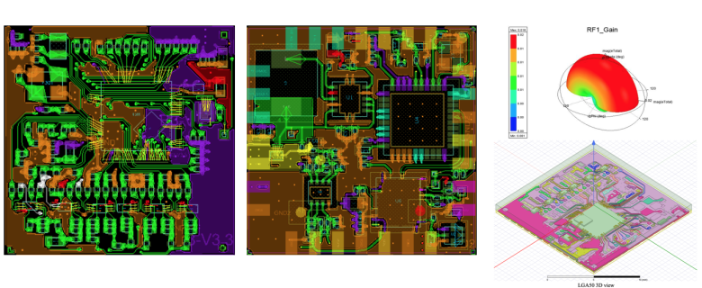
SiP 封装优势。在IC封装领域,是一种先进的封装,其内涵丰富,优点突出,已有若干重要突破,架构上将芯片平面放置改为堆叠式封装,使密度增加,性能较大程度上提高,表示着技术的发展趋势,在多方面存在极大的优势特性,体现在以下几个方面。SiP 实现是系统的集成。采用要给封装体来完成一个系统目标产品的全部互联以及功能和性能参数,可同时利用引线键合与倒装焊互连技术以及别的IC芯片堆叠等直接内连技术,将多个IC芯片与分立有源和无源器件封装在一个管壳内。汽车汽车电子是 SiP 的重要应用场景。江苏COB封装供应
SiP涉及许多类型的封装技术,如超精密表面贴装技术(SMT)、封装堆叠技术,封装嵌入式技术等。河南系统级封装
合封电子的功能,性能提升,合封电子:通过将多个芯片或模块封装在一起,云茂电子可以明显提高数据处理速度和效率。由于芯片之间的连接更紧密,数据传输速度更快,从而提高了整体性能。稳定性增强,合封电子:由于多个芯片共享一些共同的功能模块,以及更紧密的集成方式,云茂电子可以减少故障率。功耗降低、开发简单,合封电子:由于多个芯片共享一些共同的功能模块,以及更紧密的集成方式,云茂电子可以降低整个系统的功耗。此外,通过优化内部连接和布局,可以进一步降低功耗。防抄袭,多个芯片和元器件模块等合封在一起,就算被采购,也无法模仿抄袭。河南系统级封装
上一篇: 天津多用途信号采集控制盒产品方案市价
下一篇: 南通IPM封装流程