龙岩爱步精益生产流程标准化
在全球竞争日益激烈的***,精益生产已经成为企业提升竞争力、赢得市场优势的重要战略手段。通过实施精益生产,企业能够降低成本、提高效率、优化质量,从而在市场中获得更大的竞争优势。首先,精益生产有助于企业降低成本。通过消除生产过程中的浪费、提高设备利用率和降低库存水平等方式,企业可以***降低生产成本,提高盈利能力。其次,精益生产能够提高企业的生产效率。通过优化生产流程、提高员工技能和采用先进的生产技术等方式,企业可以缩短生产周期、提高生产效率,从而更快地响应市场需求。***,精益生产有助于企业提升产品质量。通过加强质量控制、实施标准化作业和持续改进等方式,企业可以确保产品质量的稳定性和可靠性,提高客户满意度和忠诚度。综上所述,精益生产在全球竞争中具有举足轻重的战略地位。企业应积极引入并实施精益生产理念和方法,以不断提升自身的竞争力和市场地位。精益生产主张进行持续改进,不断优化生产过程,从而实现效率和质量的提升。龙岩爱步精益生产流程标准化
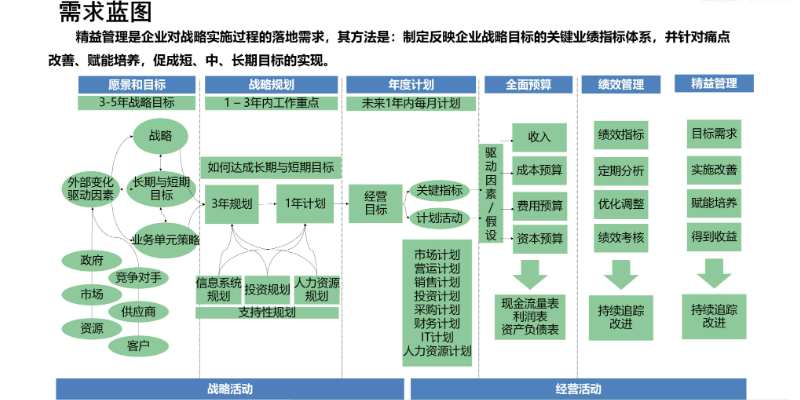
库存浪费也是企业在生产过程中需要关注的重要问题。过高的库存水平意味着资金的沉淀和风险的增加。同时,库存的保管和维护也需要消耗大量的资源和人力。为了减少库存浪费,企业可以通过精确预测市场需求、优化供应链管理、提高库存周转率等方式来降低库存水平。不合理的动作和操作方法也是浪费的重要来源。在生产过程中,员工可能因为操作习惯不当或设备设计不合理而导致动作浪费。这不仅增加了人力和时间的消耗,还可能影响员工的工作效率和质量。为了改善这种情况,企业可以通过引入标准化作业流程、开展员工培训和技能提升计划、优化设备布局等方式来降低动作浪费。湛江厦门爱步精益咨询有限公司精益生产降本增效推行精益主要改善活动之一,是提案建议制度,保障全员积极参与改善。
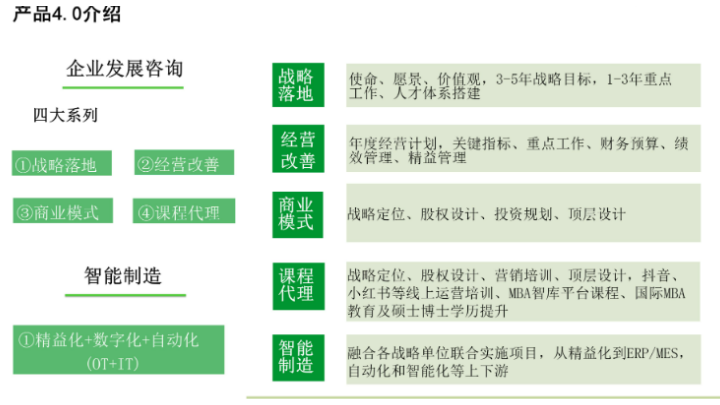
过量生产是七大浪费中的首要问题。企业往往为了追求产量而忽视实际需求,导致产品积压、库存增加。这不仅占用了大量的资金,还增加了仓储、维护和管理的成本。此外,过量生产还可能导致产品过期、损坏等风险,进一步加剧浪费。因此,企业在生产过程中应严格按照市场需求进行生产规划,避免过量生产带来的浪费。等待时间也是企业常常忽视的浪费之一。在生产线上,员工或设备可能因为前道工序未完成、物料供应不及时等原因而处于等待状态。这种等待不仅造成了生产力的闲置,还可能导致员工的不满和质量的波动。为了减少等待时间,企业可以通过优化生产流程、提高物料供应的准时率、引入自动化设备等方式来降低等待浪费。
确定看板的类型和数量根据生产流程和需求,确定需要使用的看板类型,如生产看板、取货看板等。计算每种看板的合理数量,以确保生产过程的顺畅进行,同时避免过多的看板造成浪费。设计看板的格式和内容设计看板的格式,使其易于识别和理解。看板上应包含必要的信息,如产品型号、数量、生产时间、供应地点等。确保看板的内容准确、清晰,避免产生误解。建立看板的运行规则制定看板的使用规则,包括看板的发放、传递、回收等环节的操作流程。明确各部门在看板管理中的职责和权限,确保看板管理的有效实施。培训员工对员工进行看板管理的培训,使他们了解看板的作用、类型、使用方法和运行规则。确保员工能够正确地使用看板,及时传递信息,遵守看板管理的规定。实施看板管理按照设计好的看板管理方案,开始实施看板管理。在实施过程中,要密切关注看板的运行情况,及时发现问题并进行调整。定期对看板管理的效果进行评估,不断改进和完善看板管理体系。帮助人们积极参与改善,是推行精益的根本。
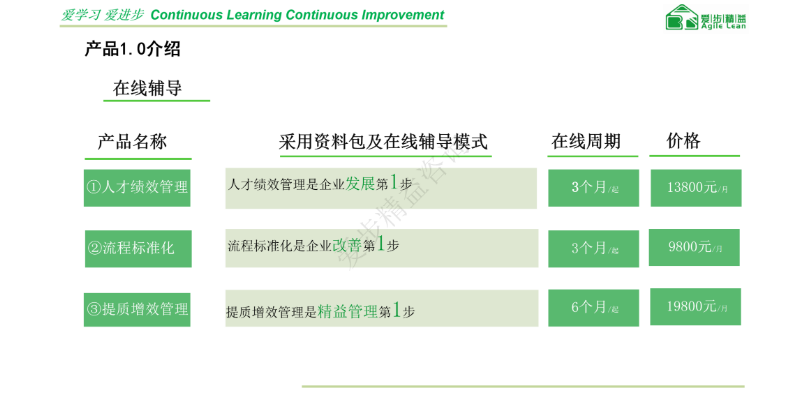
在实施七大浪费管理的过程中,企业需要建立一套完善的管理制度和监督机制。这包括制定明确的浪费识别标准、建立持续改进的文化氛围、开展定期的浪费检查和评估等。通过这些措施,企业可以及时发现和消除浪费现象,确保生产过程的效率和效益。七大浪费管理是企业实现精益生产的重要一环。通过识别并消除这些浪费,企业不仅可以降低成本、提高效率,还可以提升产品质量和客户满意度。然而,浪费管理并非一蹴而就的过程,需要企业长期坚持并不断改进。因此,企业应将七大浪费管理纳入日常管理中,使其成为企业文化的一部分,从而推动企业持续、稳健的发展。生产管理包括时间表、预算和生产过程所需的材料等。三明爱步精益咨询精益生产精益管理
保质保量,完成任务。龙岩爱步精益生产流程标准化
看板管理是一种以看板为主要工具,实现生产过程中信息传递和控制的管理方法。看板通常是一种卡片、标识牌或电子显示屏等,上面记录着生产指令、物料需求、生产进度等信息。作用信息传递:看板作为信息载体,将生产指令、物料需求等信息从一个环节传递到另一个环节,确保生产过程的顺畅进行。生产控制:通过看板的数量和流动,可以控制生产的节奏和进度,避免过度生产或生产不足。减少浪费:看板管理有助于实现准时化生产,减少库存、等待时间和搬运等浪费。提高透明度:使生产过程中的信息更加透明,便于管理人员和员工了解生产情况,及时发现问题并采取措施。龙岩爱步精益生产流程标准化
上一篇: 中山如何开展6s价格
下一篇: 三明从事企业管理做的怎么样