山东金属管材金相检验
选择物理性能检测服务的好处是什么?选择物理性能检测服务有以下几个好处:1.确保产品质量:物理性能检测可以帮助确保产品在使用过程中具有足够的强度、硬度和耐久性等特性,从而提高产品质量和性能。2.安全保障:通过物理性能检测可以评估材料或零部件在受到力量、压力或冲击时的表现,有助于预测和避免潜在的安全问题和事故。3.产品改进和优化:物理性能检测可以提供对产品材料和结构的详细评估,可以帮助生产商发现潜在的问题,并进行相应的改进和优化,提高产品的性能和可靠性。4.合规要求满足:某些行业和应用领域对产品的物理性能有严格的要求和标准,进行物理性能检测可以确保产品符合相关的法规和标准,满足合规要求。5.市场竞争优势:通过进行物理性能检测,企业可以证明其产品具有良好的性能和质量,从而在市场上建立竞争优势,吸引更多的客户和合作伙伴。金相检验可以帮助确定金属材料的晶粒大小、晶界分布、相含量等重要参数。山东金属管材金相检验
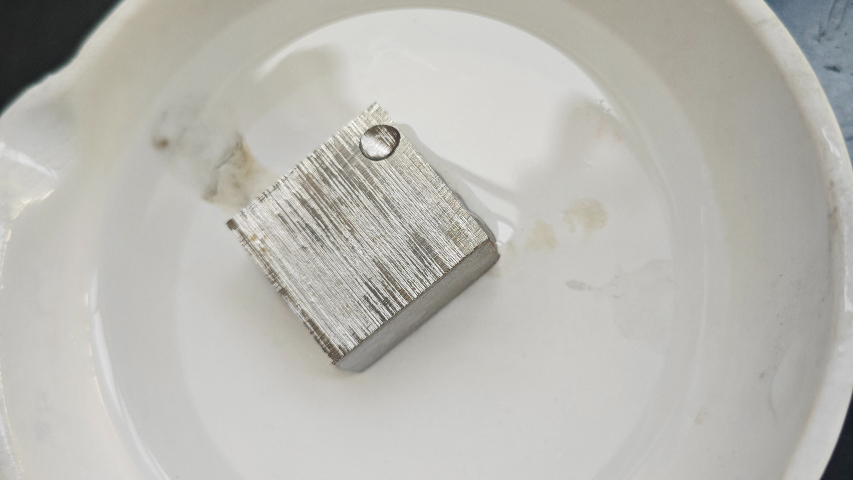
金属低倍组织检验中,如何判断材料在加工过程中是否发生了变形?在金属低倍组织检验中,判断材料在加工过程中是否发生了变形,可以从以下几个方面进行观察和分析:1、观察晶粒形状和大小:如果材料的晶粒形状和大小不均匀,或者出现了明显的拉伸、扭曲等变形,那么就可以判断材料在加工过程中发生了变形。2、观察晶界和相界:如果材料的晶界和相界出现了明显的拉伸、扭曲等变形,那么也可以判断材料在加工过程中发生了变形。3、观察组织中的夹杂物和缺陷:如果材料中出现了明显的夹杂物和缺陷,特别是沿着加工方向分布的夹杂物和缺陷,那么也可以判断材料在加工过程中发生了变形。4、观察材料的硬度和强度:如果材料的硬度和强度与原材料相比有明显的提高,那么也可以判断材料在加工过程中发生了变形。金属材料晶粒度检验服务厂家推荐机械零部件的物理性能检测通常涉及多个方面的测试方法。

金属物理性能检测的特点是什么?金属物理性能检测的特点包括以下几个方面:1、非破坏性检测:金属物理性能检测通常采用非破坏性检测方法,不会对被测物体造成损伤,保证了被测物体的完整性和可用性。2、高精度:金属物理性能检测技术具有高精度、高灵敏度、高分辨率等特点,能够检测出微小的变化和缺陷。3、多参数检测:金属物理性能检测可以对多个参数进行检测,如硬度、强度、延展性、磁性等,能够全方面了解被测物体的物理性能。4、快速检测:金属物理性能检测通常采用自动化、智能化的检测设备,能够快速、准确地完成检测任务。
金属金相检验中如何处理显微组织中的杂质?1、化学清洗:使用化学试剂将杂质从样品表面或内部清理。例如,使用酸或碱溶液清洗样品表面的氧化物或其他化学物质。2、机械处理:使用机械方法将杂质从样品表面或内部清理。例如,使用研磨机或切割机将样品表面的氧化物或其他杂质去除。3、热处理:通过加热样品将杂质从样品中清理。例如,使用高温热处理将样品中的氧化物或其他杂质分解或挥发出来。4、磁选:使用磁性材料将样品中的磁性杂质分离出来。例如,使用磁性材料将样品中的铁磁性杂质分离出来。5、氧化还原处理:通过氧化还原反应将样品中的杂质清理。例如,使用还原剂将样品中的氧化物还原为金属。黑色金属低倍组织检验是一种常用的物理性能检测方法。
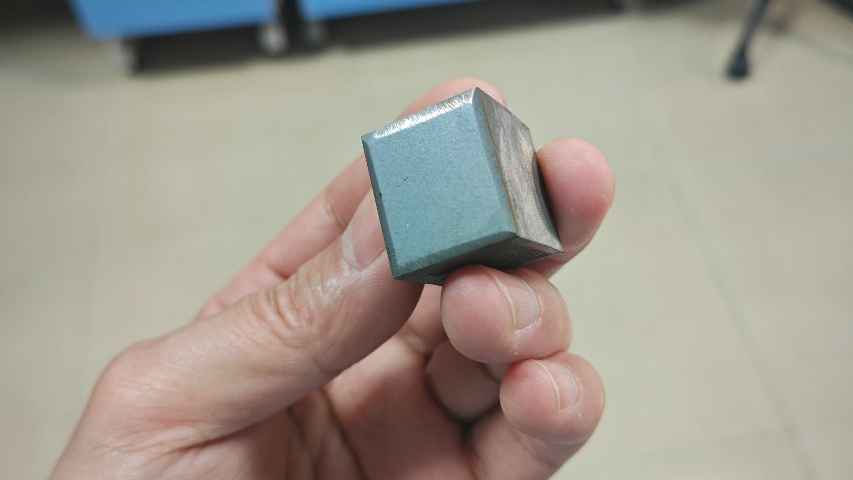
金属金相检验是对金属材料的显微组织进行观察和评估的一种方法。其作用包括以下几个方面:1、评估材料性能:金相检验可以评估金属材料的物理性能,如硬度、强度、韧性、塑性、疲劳性等等。通过观察晶粒大小、晶粒形态和分布等因素来判断材料的性能优劣。2、检测材料质量:金相检验可以检测材料中的缺陷和夹杂物等微观结构,评估材料的质量和可靠性。3、预测材料寿命:金相检验可以评估金属材料的耐久性,预测材料在实际使用过程中的寿命和维护周期。4、指导材料加工:金相检验可以为金属材料的加工提供参考,指导材料的热处理工艺以及加工工艺。金属物理性能检测可以帮助工程师和科学家了解材料的性能,指导材料选择和加工工艺的优化。山东金属管材金相检验
金相检验可以用于评估金属材料的硬度、韧性、强度等力学性能。山东金属管材金相检验
金属低倍组织检验中,晶粒大小对材料性能有何影响?1、机械性能差:晶粒较大时,材料的强度、韧性和延展性等机械性能会降低。这是因为一个晶粒内部存在较多的晶界和微缺陷,这些缺陷易于成为断裂的起点,从而降低材料的断裂强度和延展性。2、耐蚀性差:晶粒较大时,材料的耐蚀性也会变差。晶界是材料中腐蚀的敏感区域,晶粒较大时,晶界的比例也会增加,从而导致材料的耐蚀性变差。3、信号差:晶粒较大时,材料中的组织结构不规则,信号的传递也会受到阻碍。对于一些特殊的材料,例如电子器件中使用的半导体材料,晶粒大小对信号的传递和响应也有着重要的影响。山东金属管材金相检验
上一篇: 郑州金属板材渗透探伤检测
下一篇: 苏州金属管材无损探伤测试