储罐检测在线腐蚀监测设备排名
目前,大气腐蚀在线监测技术已经取得了很大的进步,但还存在以下问题:(1) 现有的在线监测方法虽然丰富,但还存在数据采集不够稳定、数据分析方法不够多样、建立的模型不够准确等问题,有待进一步研究完善。(2) 各种新型材料的出现和对各种严酷环境的探索,使材料大气腐蚀的情况更加复杂,对以往的在线监测方法提出了新要求。(3) 现代科技的发展为腐蚀在线监测提供了新的思路和方法。例如图像识别技术的发展,让我们可以直接对试样的腐蚀表面进行信息提取,希望通过一张宏观照片便可以对腐蚀情况进行定性与定量分析。腐蚀监测设备需要定期校准,以确保数据的准确性。储罐检测在线腐蚀监测设备排名
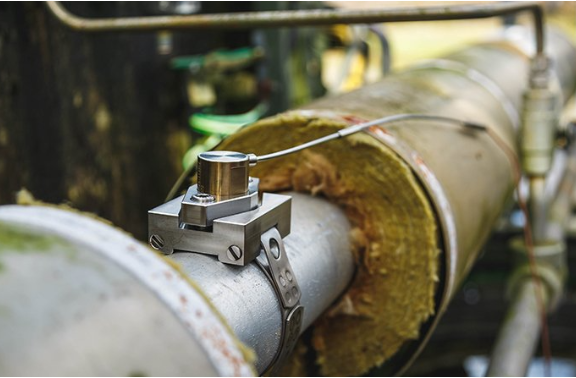
我们开发出了一种可以用于钢筋腐蚀损伤监测的嵌入式压电超声监测仪,并且进行了不同腐蚀实验来验证该仪器的腐蚀监测能力,实验结果表明:腐蚀初期的超声振幅和峰值会随着腐蚀时间的增加而减少,当出现腐蚀损伤时,超声波谱中会出现与其对应的波包,频域谱中的峰值幅度随着腐蚀速率的增加而减小。但是随着腐蚀进行,损伤越来越多,超声波的传输规律变得更加复杂,得到的波谱变得难以分析。超声波测厚是超声波技术的一个重要分支,通过超声波测量材料的厚度变化来监测材料的腐蚀情况,普遍地应用于管道腐蚀中,该方法存在的主要问题是误判率高、运算量巨大。黑龙江保温层在线腐蚀监测设备在线腐蚀监测系统能够确保工业设备的安全运行。
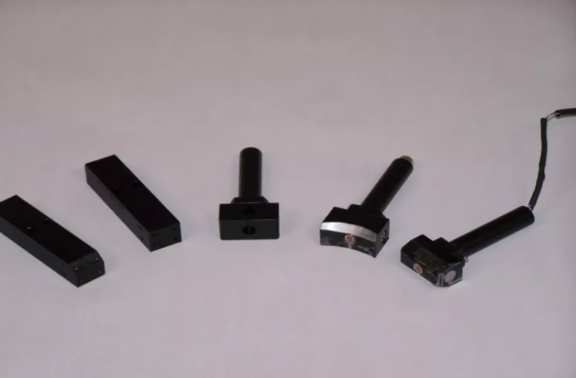
除此之外,将电化学阻抗谱和其他实验和方法结合起来是发展趋势,一是可以提高EIS的结果准确性,二是能够应用于更多样的腐蚀环境。提出了一种将电化学阻抗谱测试与腐蚀疲劳实验结合起来同时进行的新型装置,用相位角的变化可以用来监测腐蚀疲劳裂纹的形成,建立了腐蚀疲劳裂纹阻抗模型,该模型结果与人工裂纹试验十分吻合。这种方法相较于单纯的电化学阻抗谱,能够得到更多的疲劳腐蚀信息。同时用电化学阻抗技术和薄膜电阻探针技术对高速列车的高速动载工况进行了腐蚀监测,并利用了无线通讯技术实现了对高速动车组的长期腐蚀监测,更全方面的掌握车辆的关键材料服役情况。
采用Fe/Ag双电极的ACM对耐候性钢桥不同部位进行了监测,表明试样的厚度减少和ACM的平均电量有着对应的关系,由此对不同部位的耐蚀性进行了寿命预测。但ACM的缺点也是显而易见的:一是得到的材料腐蚀结果不够真实,需要验证准确性;二是随着监测的进行,锈层变厚之后,监测的灵敏度会降低,不适合进行长期监测。通过大气暴晒试验和ACM技术研究了碳钢在湖南大气环境中的腐蚀行为,测得的ACM累计电量与Q235钢大气腐蚀速率之间符合线性关系,认为ACM技术可用于碳钢大气腐蚀的行为预测,成功验证了ACM的准确性。腐蚀监测数据可用于评估设备的维修和更换时机。
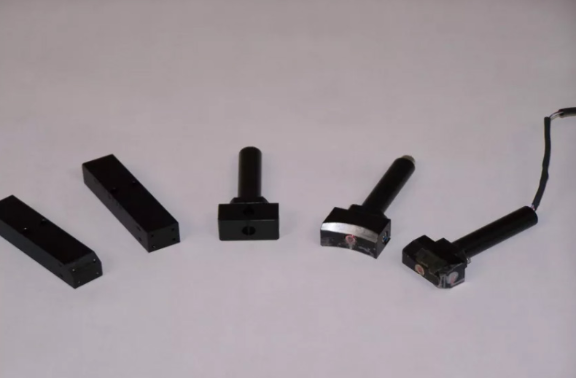
主要监测数据及功能:监测矿脂保护下的悬索不同位置点的腐蚀速率;新设计涂层腐蚀监测探头、电阻探针腐蚀监测探头,方便固定在现场;对涂层/金属基体的界面电容、电荷传递电阻和基体腐蚀速率的在线监测,进而推断出涂层的介电常数、含水率和孔隙 率和老化系数等参数;结合恒流激励技术和高精度电桥原理,具有极高的金属减薄分辨率(Inm),应用差分补偿原理能自动补偿环境温度漂移,保证测量结果的稳定性和可靠性。采用设备:CST480AS大气腐蚀监测仪、CST1808涂层腐蚀监测仪、CST610无线数据收发器,采用探头:涂层腐蚀监测探头、平面型电阻探针,数据传输方式:无线数据传输,与监测软件组成无线数据远程监测网络。在线腐蚀监测系统能够减少企业的运营风险。江苏管道在线腐蚀监测设备行价
在线监测技术能及时发现腐蚀热点区域。储罐检测在线腐蚀监测设备排名
电指纹,电指纹(FSM)技术是将传感针或电极呈矩阵式焊接在管道表面(探针间距一般为壁厚的2~3倍),通过监测电极上采集电压与初始值的变化来检测由于腐蚀引起的金属损失、脆裂和凹坑。矩阵分布电极可以进行大面积腐蚀监测分析,判断凹坑和脆裂的位置和严重程度,计算腐蚀速率及趋势,敏感性是剩余壁厚的0.1%。由于其非插入式大面积监测的模式,其优点表现为:① 没有泄漏的危险,提高在硫化氢环境中的安全性,适用于困难的位置;② 不需耗材(探针、挂片),不需取放工具;③ 可以大面积测量,能够测量均匀腐蚀、局部腐蚀;④ 测量不受导电性硫化亚铁膜的影响,适用于无线、在线测量。FSM技术也存在自身的不足:① 监测时需要在管壁表面焊接矩阵电极,技术水平要求高,操作复杂;② 监测操作及数据分析复杂,设备昂贵。目前FSM的设备、监测技术和数据解析技术仍被国外公司所垄断。国内油气田以及炼化厂使用时仍以从国外进口设备为主,不只成本很高,而且后续的复杂数据解析还要依靠国外公司的技术服务。储罐检测在线腐蚀监测设备排名
上一篇: 吴江巡检工业无人机研发
下一篇: 江苏柔性保温系统生产厂家