PA3003-PCC10A加热板总代理
本发明半导体加工领域,尤其涉及一种晶圆加热器。背景技术:现有的晶圆加热设备,加热丝呈螺旋状从中心向**旋转,加热丝在热盘中的分布不够均匀,无法达到均匀加热的目的,无法满足晶圆的高精度加热,而高精度加热对半导体的工艺至关重要。如中国发明专利cna所公开的一种能够提高照射效率的加热器。实施方式所涉及的加热器具备发光管、发热体及反射膜。发光管呈筒状,且所述发光管透光。发热体设置在发光管的内部,且发热体以碳作为主要成分。反射膜设置在发光管的外周面,并对光进行反射。上述现有技术的晶圆加热器无法恒温的均匀加热。技术实现要素:一、要解决的技术问题本发明的目的是针对现有技术所存在的上述问题,特提供一种晶圆加热器,解决现有加热器无法恒温的均匀加热的问题。二、技术方案为解决上述技术问题,本发明提供一种晶圆加热器,包括:加热盘、底板和若干垫柱;加热盘上设有七个加热区域,分别为***加热区域、第二加热区域、第三加热区域、第四加热区域、第五加热区域、第六加热区域和第七加热区域;***加热区域设置于中心区域,第二加热区域和第三加热区域设置于***加热区域外圆周。在半圆形热片2的自由端是分别接着电源的左电极和右电极。PA3003-PCC10A加热板总代理
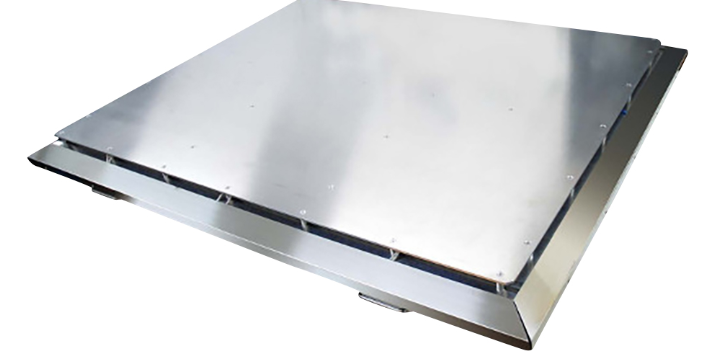
MR)等在高温中气相化学反应(热分解,氢还原、氧化、替换反应等)在基板上形成氮化物、氧化物、碳化物、硅化物、硼化物、高熔点金属、金属、半导体等薄膜方法。因只在高温下反应故用途被限制,但由于其可用领域中,则可得致密高纯度物质膜,且附着强度很强,若用心控制,则可得安定薄膜即可轻易制得触须(短纤维)等,故其应用范围极广。热CVD法也可分成常压和低压。低压CVD适用于同时进行多片基片的处理,压力一般控制在。作为栅电极的多晶硅通常利用HCVD法将SiH4或Si2H。气体热分解(约650oC)淀积而成。采用选择氧化进行器件隔离时所使用的氮化硅薄膜也是用低压CVD法,利用氨和SiH4或Si2H6反应面生成的,作为层间绝缘的SiO2薄膜是用SiH4和O2在400--4500oC的温度下形成SiH4+O2-SiO2+2H2或是用Si(OC2H5)4(TEOS:tetraethoxysilanc)和O2在750oC左右的高温下反应生成的,后者即采用TEOS形成的SiO2膜具有台阶侧面部被覆性能好的优点。前者,在淀积的同时导入PH3气体,就形成磷硅玻璃(PSG:phosphorsilicateglass)再导入B2H6气体就形成BPSG(borro?phosphorsilicateglass)膜。这两种薄膜材料,高温下的流动性好,***用来作为表面平坦性好的层间绝缘膜。PA10005-PCC10A加热板一级代理防止工质进入过渡沸腾区,从而导致传热恶化,壁温过热。
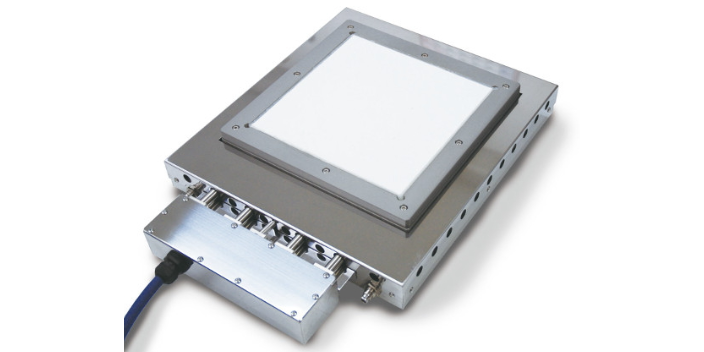
沉积掺杂硼磷的氧化层含有硼磷杂质的SiO2层,有较低的熔点,硼磷氧化层(BPSG)加热到800oC时会软化并有流动特性,可使晶圆表面初级平坦化。深处理溅镀***层金属利用光刻技术留出金属接触洞,溅镀钛+氮化钛+铝+氮化钛等多层金属膜。离子刻蚀出布线结构,并用PECVD在上面沉积一层SiO2介电质。并用SOG(spinonglass)使表面平坦,加热去除SOG中的溶剂。然后再沉积一层介电质,为沉积第二层金属作准备。(1)薄膜的沉积方法根据其用途的不同而不同,厚度通常小于1um。有绝缘膜、半导体薄膜、金属薄膜等各种各样的薄膜。薄膜的沉积法主要有利用化学反应的CVD(chemicalvapordeposition)法以及物理现象的PVD(physicalvapordeposition)法两大类。CVD法有外延生长法、HCVD,PECVD等。PVD有溅射法和真空蒸发法。一般而言,PVD温度低,没有毒气问题;CVD温度高,需达到1000oC以上将气体解离,来产生化学作用。PVD沉积到材料表面的附着力较CVD差一些,PVD适用于在光电产业,而半导体制程中的金属导电膜大多使用PVD来沉积,而其他绝缘膜则大多数采用要求较严谨的CVD技术。以PVD被覆硬质薄膜具有**度,耐腐蚀等特点。(2)真空蒸发法。
晶圆测试是对晶片上的每个晶粒进行针测,在检测头装上以金线制成细如毛发之探针(probe),与晶粒上的接点(pad)接触,测试其电气特性,不合格的晶粒会被标上记号,而后当晶片依晶粒为单位切割成**的晶粒时,标有记号的不合格晶粒会被洮汰,不再进行下一个制程,以免徒增制造成本。在晶圆制造完成之后,晶圆测试是一步非常重要的测试。这步测试是晶圆生产过程的成绩单。在测试过程中,每一个芯片的电性能力和电路机能都被检测到。晶圆测试也就是芯片测试(diesort)或晶圆电测(wafersort)。在测试时,晶圆被固定在真空吸力的卡盘上,并与很薄的探针电测器对准,同时探针与芯片的每一个焊接垫相接触(图)。电测器在电源的驱动下测试电路并记录下结果。测试的数量、顺序和类型由计算机程序控制。测试机是自动化的,所以在探针电测器与***片晶圆对准后(人工对准或使用自动视觉系统)的测试工作无须操作员的辅助。测试是为了以下三个目标。***,在晶圆送到封装工厂之前,鉴别出合格的芯片。第二,器件/电路的电性参数进行特性评估。工程师们需要监测参数的分布状态来保持工艺的质量水平。第三,芯片的合格品与不良品的核算会给晶圆生产人员提供***业绩的反馈。每组加热片的自由端分别连结电源的两极。
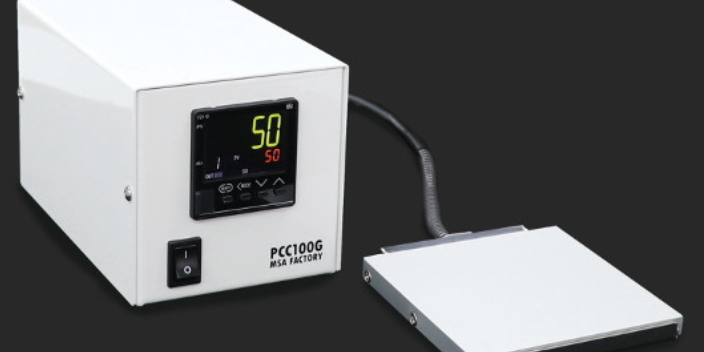
3-1.研磨盘主体;3-2.数显深度测量指示表;4.安装支架;5.晶圆加热器。具体实施方式为了使本实用新型的发明目的、技术方案及其有益技术效果更加清晰,以下结合附图和具体实施方式,对本实用新型进行进一步详细说明;在附图中:一种等离子体cvd晶圆加热器用表面修磨装置,其特征在于:从下至上依次设置有安装支架4、旋转装置2、加热器支撑圆盘1、研磨盘3,晶圆加热器5设置在加热器支撑圆盘1和研磨盘3之间;研磨盘3包括研磨盘主体3-1,研磨盘主体3-1底部设置有研磨块3-5、调节支撑圆柱3-4,研磨盘主体3-1通过调节螺栓3-3与研磨块3-5相连接固定,调节螺栓3-3的上端设置有数显深度测量指示表3-2;所述的安装支架4包括安装支撑柱4-3,安装支撑柱4-3上端设置有安装平板4-2,安装支撑柱4-3下端设置有高度调节块4-4,安装平板4-2上设置有安装主体4-1,安装主体4-1内部设置有台阶孔,装有旋转电机2-2的固定座2-1下部与台阶孔相配合固定,旋转电机2-2的上表面设置有连接圆盘2-3,连接圆盘2-3上端设置有支撑圆盘本体1-1,支撑圆盘本体1-1上端通过螺丝1-3固定有圆环1-2;所述的调节支撑圆柱3-4与圆环1-2相连接。所述的高度调节块4-4与安装支撑柱4-3之间设置为螺纹连接。控制模块降低温度较高的分区的功率继电器的输出功率。上海 PA3025-WP-PCC20A加热板价格
膜厚与时间的平方根成正比。因而,要形成较厚SiO2膜,需要较长的氧化时间。PA3003-PCC10A加热板总代理
使得同心圆圆弧上的位置温场分布较差。但是传统构造的加热片在采用时候会存在很多疑问:1.中间ω形状的热弧板1在持续加热工作后会有变形,这种变形又会更进一步引致加热片的总体变形,这种总体变形又会让两组加热片之间彼此相近(易于放电打火甚至短路)或上翘,这种远离或相近也会导致左电极3和右电极4,如附图2中相片的黑色箭头指示位置处。2.为了确保加热安定,其加热片的构造相同,这使得直线对称构造的加热片,其左电极3和右电极4在同一侧,会存在短路隐患,更是是总体变形后还会存在挤碎底部陶瓷的高风险。3.为了防范每组加热片之间短路,在每个包抄的加热片之间都会留有空隙22,而传统两组加热片之间存在的空隙22(主要在直线对称轴附近)空间分布不合理,迂回拐点相对处较近,其他地方较宽,会导致提供给芯片发育的热源不安定;同时,这种间隔较大,由于存在较大的温差,故此也致使拱形热片2的迂回拐点特别容易发生变形,附图3中的相片所示;相反,如果在直线对称轴附近留有的空隙较小,又会因为疑问1的缘故特别易于引致短路。目前的解决办法是:对传统加热片频繁的检查,做到早发现,早更换。但是这会增加加热片的使用成本。PA3003-PCC10A加热板总代理
上海九展自动化技术有限公司汇集了大量的优秀人才,集企业奇思,创经济奇迹,一群有梦想有朝气的团队不断在前进的道路上开创新天地,绘画新蓝图,在上海市等地区的机械及行业设备中始终保持良好的信誉,信奉着“争取每一个客户不容易,失去每一个用户很简单”的理念,市场是企业的方向,质量是企业的生命,在公司有效方针的领导下,全体上下,团结一致,共同进退,**协力把各方面工作做得更好,努力开创工作的新局面,公司的新高度,未来上海九展自动化供应和您一起奔向更美好的未来,即使现在有一点小小的成绩,也不足以骄傲,过去的种种都已成为昨日我们只有总结经验,才能继续上路,让我们一起点燃新的希望,放飞新的梦想!