上海旋压轮毂制造
旋压与低压铸造的区别:
1、低压铸造是将金属液体通过设备施加压力灌注到铸模之中,在这个过程中一直保持一个恒定压力,在保证了金属液体的密度同时,也保证了凝固后金属的强度。并且低压铸造的过程全部由机械完成,并且铸造成型的良品率高,非常适合大批量生产,所以目前汽车厂商指定的铸造铝合金轮毂都是由这种工艺生产出来的。
旋压铸造技术则是在铸造技术上演变而来,在铸造后的毛坯轮毂进行在加工处理,主要是对轮辋部分行旋转冲压,这个过程中轮辋部分被加热同时旋刀进行旋转,将轮辋逐渐拉长变薄。此时轮辋内部金属分子排列更为紧密,所以此处的金属强度更高。
上海旋压轮毂有三片式旋压轮毂、两片式旋压轮毂和整体锻旋式旋压轮毂三类。上海旋压轮毂制造
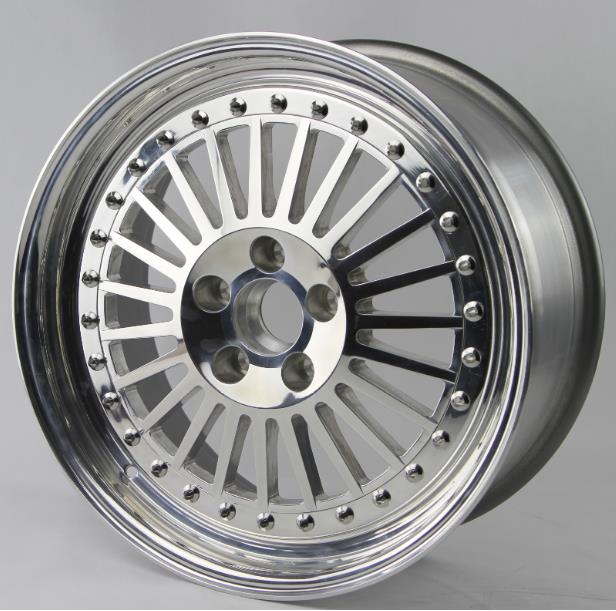
轮毂改装误区(四)
忽视轮毂安装环节,轮毂没有正确安装
很多初改轮毂的朋友,买好轮毂后,怀揣激动心情立马就开车到店安装,也不认真验货匆匆看了一眼,就对安装小哥说:装!装!装!。但是现实往往很打脸。
由于目前改装店家良莠不齐,本来觉得So easy 的轮毂安装如果没有注意以下安装细节,还是会出幺蛾子。。。
1)没有安装变径圈:车辆日常行驶时可能会有抖动问题。
2)动平衡配重没有归零:车辆高速行驶时,可能会抖动问题。
3)没有使用扭力板手紧固轮毂:太松轮毂可能会有脱落危险,太紧可能会损伤螺母/螺栓。
4)轮胎规格与轮毂不匹配:轮胎磨损异常,甚至轮毂无法装胎或有剐蹭问题。
上海旋压轮毂制造什么是旋压轮毂?它是怎么制作的?

三片式旋压轮毂的优势:三片式旋压轮毂是由前片和后片还有轮辐三部分组成,前片和后片属于轮辋的部分。三片式轮毂的轮辐与轮辋连接方式现在有两种形式,一种是使用专业的螺栓或螺母做好连接,还有-种是使用焊接的方式做好连接,由于三片式轮毂要保障轮毂的气密性,组装后以后,需要做好封胶,确保气密性防止漏气。三片式的轮毂除了考虑轮毂的性能之外,大部分考虑的是轮毂的外观,而且三片式轮毂的轮辋部分是可以共用的,要想改变轮毂的造型,只要替换不同款式的中盘就可以了。
旋压工艺方式一般可采用取板材劈开式旋压或用铸(锻)件毛坯进行强力旋压成型两种工艺方式。劈开式旋压工艺是将圆盘状板坯用劈开轮通过分层工艺,使毛坯在中部被劈成两个等分,之后,再用成型轮渐进普旋成型即可;强旋工艺是将铸铝毛坯或锻造毛坯进行若干道次的强旋成型工艺,旋压达到轮毂型面尺寸要求,强旋工艺生产出来的轮毂重量比锻造轮毂重量可减轻大约25%,这是因为强旋工艺可旋制出变截面厚度,在满足车轮强度指标
要求的前提下,可适当减薄轮毂厚度。
旋压轮毂的厂家有哪些?

轮毂不同制造工艺的区别:重力铸造非常简单,将液态的金属倒进轮毂模具中冷却成型。这种铸造方式效率非常高,成本也低,但是质量比较差,由于轮毂的各部分分布不是很均匀,而且金属内部分子的密度比较低,所以轮毂的强度不高,碰撞后很容易出现断裂的情况;低压铸造是在重力铸造的基础上进行了一个升级,将液态的金属倒入模具之后,给它施加一个恒定的压力,使金属的分子密度增高,轮毂成型之后会有更高的强度,且低压铸造的工艺也非常成熟,所以目前大部分车型上的轮毂采用的都是低压铸造工艺;旋压铸造是将铸造后的轮毂进行一个二次加工,将轮毂一边加热一边进行旋压加工,这样可使轮毂内的金属分子更加紧密,强度也更高。所以,这三种工艺的轮毂重量,旋压轮毂<低压铸造轮毂<重力铸造轮毂。 怎样才能识别旋压轮毂?怎么选旋压轮毂
旋压轮毂的优点有哪些?上海旋压轮毂制造
尚晞数控科技研发和生产的旋压轮毂,根据组装方式可分为三片式旋压轮毂、两片式旋压轮毂和整体式锻旋轮毂。三片式旋压轮毂,顾名思义,即指轮毂可分为三片:前片、后片和中片。前片和后片是指组成轮毂轮圈的较窄和较宽的两圈圆片,轮毂中片就是轮毂的轮辐,就是我们经常用来评判一个轮毂好不好看的有花色的那片。前片、中片和后片由一组特 制的**螺栓组合而成。这种组装方式的优点就是组装灵活性大,车主们可根据自己的喜好选择规格、轮辐花型、色彩、亮度等等,组合出十 分具有个性的轮毂。 上海旋压轮毂制造
上海尚晞数控科技有限公司是一家有着先进的发展理念,先进的管理经验,在发展过程中不断完善自己,要求自己,不断创新,时刻准备着迎接更多挑战的活力公司,在上海市等地区的机械及行业设备中汇聚了大量的人脉以及**,在业界也收获了很多良好的评价,这些都源自于自身的努力和大家共同进步的结果,这些评价对我们而言是比较好的前进动力,也促使我们在以后的道路上保持奋发图强、一往无前的进取创新精神,努力把公司发展战略推向一个新高度,在全体员工共同努力之下,全力拼搏将共同上海尚晞数控科技供应和您一起携手走向更好的未来,创造更有价值的产品,我们将以更好的状态,更认真的态度,更饱满的精力去创造,去拼搏,去努力,让我们一起更好更快的成长!