动态测试超声波键合机生产
封装结构双面散热:随着器件功率密度的不断提高,器件封装的热管理变得愈加关键。基于上述总结与分析,优化器件封装散热路径是解决高压大电流高功率密度条件下功率器件散热、降低芯片结温的有效方案。键合线连接器件无法将芯片上表面作为散热通路,采用无键合线封装,充分利用芯片上表面进行散热,热量从芯片上下表面两个路径传递,可增强器件的散热能力,降低芯片结温,提高器件的热性能。为利用芯片上表面散热,研究人员提出了press-pack封装方法,该方法利用压力接触取代键合线和焊料,可降低杂散电感且具有更高的可靠性。该封装使器件具有双面散热的能力。自动化设备的应用促进了新一代IGBT模块的取代旧式双极管,成为电路制造中重要的电子器件。动态测试超声波键合机生产
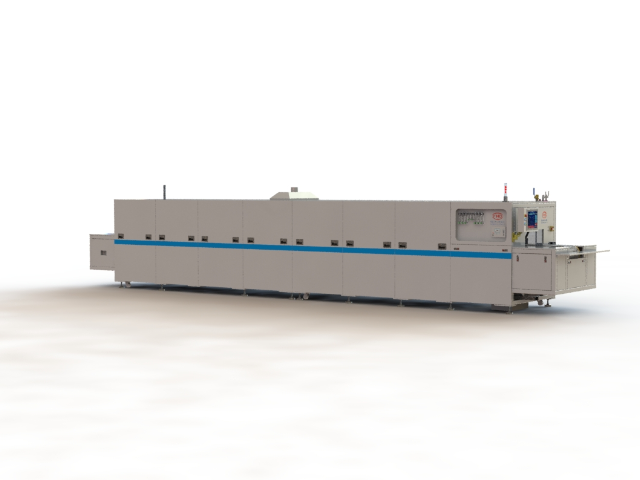
键合线与半导体器件间存在材料热膨胀系数的不匹配,使得线键合处往往成为易失效位点,甚至出现裂纹或者松动,导致接触不良,使键合点处的接触热阻增大,温度升高,加速该点的失效。无键合线单面散热器件芯片与基板的连接与键合线连接器件相同。无键合线面互连封装降低了封装寄生电感和电阻,大的接触面积增强了传热。上述封装结构只能通过由芯片底部的陶瓷基板和底板构成的路径进行散热。目前键合线连接的硅基器件单面散热封装结构已接近其散热极限,硅芯片的工作结温也接近其承受上限,严重影响了器件的性能,更限制了具有更高温度运行能力的SiC器件的性能。从散热的角度看,功率器件产生的热量只能通过底面传递,限制了其散热性能。在目前封装材料性能和封装工艺暂时无法取得较大改善的情况下,通过创新结构布局和设计,优化散热路径,是解决功率器件封装散热的有效方案。专业真空炉厂商动态测试IGBT自动化设备对产品出厂前的检验提供了支持。
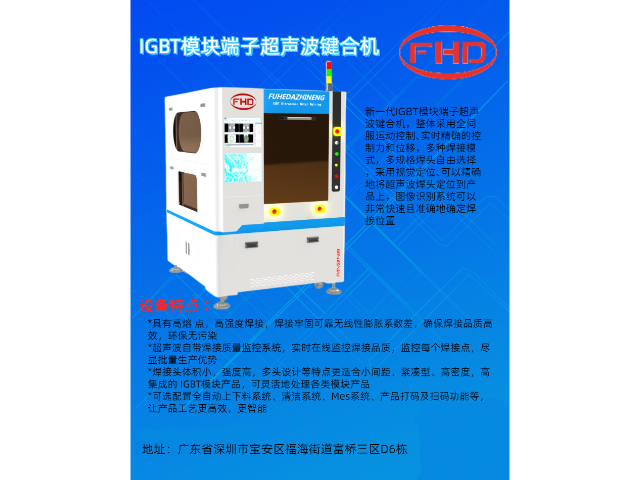
基于面互连原理,SKiN芯片连接采用扩散银颗粒烧结取代传统键合线封装中的焊料连接,芯片烧结到DBC基板上,采用两层柔性板上的可烧结铜箔连接芯片上表面和基板,柔性板的下金属层成为功率侧,承载高功率负载电流,根据材料(铝或者铜)以及所需的电流,该金属层的厚度在100μm范围内更合适。柔性板的上下金属层彼此绝缘,上金属层为逻辑侧,只需相对较薄的厚度(30μm),主要承载栅极、辅助和感应信号。柔性板上开有通孔,可以将芯片的栅极信号引出到柔性板的逻辑侧。不同于键合线的点互连,该柔性铜箔与芯片电极之间可以达到85%的接触,而传统键合线与芯片间的接触只有21%,增大接触面积和金属层厚度可以改善传热,并且可很大程度上提高器件的功率循环能力。
为追求更加优异的散热性能,研究人员提出了嵌入式功率芯片封装的双面液体冷却方案。该嵌入式封装由扁平陶瓷框架、嵌入式芯片、介电夹层和沉积金属化层互连组成[84]。将芯片嵌入到具有开槽的陶瓷框架中,并在固化炉中用粘性聚合物将芯片四周进行粘接并固化,形成的平坦表面为平面加工提供了平台。使用聚合物丝网印刷方法在其上涂上介电夹层。通过通孔与芯片的铝金属焊盘相对应,然后在其上沉积金属层,进行图案化,引出芯片正面的功率电极。IGBT自动化设备在电动汽车主逆变器功率半导体技术方面处于先进水平。
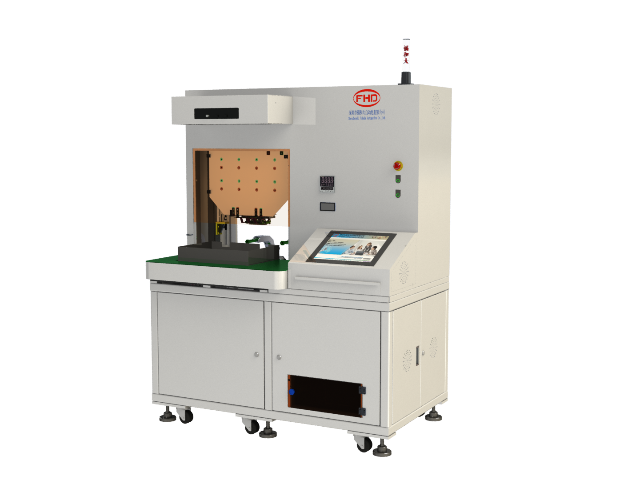
芯片产生的热量会影响载流子迁移率而降低器件性能。此外,高温也会增加封装不同材料间因热膨胀系数不匹配造成的热应力,这将会严重降低器件的可靠性及工作寿命。结温过高将导致器件发生灾难性故障及封装材料因热疲劳和高温加速导致材料退化而造成的故障问题。因此,在非常有限的封装空间内,及时高效的把芯片的耗散热排放到外界环境中以降低芯片结温及器件内部各封装材料的温度,已成为未来功率器件封装设计过程中需要考虑的重要课题。通过自动化设备,IGBT模块的封装过程更加高效、准确。浙江非标网带式气氛烤炉
电动汽车的崛起加速了功率模块封装技术的更新,IGBT自动化设备也得到了迭代升级。动态测试超声波键合机生产
在activemetalbrazing(AMB)基板中有特殊设计的空腔,将芯片嵌入到AMB空腔里,采用定制的铜夹连接芯片和AMB基板,使其与基板上金属层在同一水平面,即在封装上侧形成平面,可以在该表面和AMB基板的下表面分别连接散热器,实现双面散热。嵌入到AMB基板封装的单面散热、双面散热与传统键合线连接封装单面散热的热性能对比。结果显示,芯片嵌入AMB基板单面散热封装模块相比传统键合线连接单面散热模块,结壳热阻降幅可达40%。若在芯片嵌入AMB基板采用双面散热封装,模块的结壳热阻可进一步降低20%。动态测试超声波键合机生产
上一篇: 河南钢片FPC热压自动置料机价位
下一篇: 天津高速CCS点胶机生产厂家