福建直销跑合机
“本实用新型涉及一种轴承设备,特别是轴承跑合机;该机包括床身、电机、变速箱、主轴,其特征在于主轴安装在床身上的主轴箱上,在主轴尾端安装有一用于装卡的压力缸,该压力缸通过安装在空心主轴中的拉杆控制安装在主轴前端的装卡装置,在主轴箱上部的床身上固定有施压装置,施压装置由压力缸和压力缸活塞杆端部安装的施压头组成,施压头上安装有温度检测装置;施压装置的压力缸和装卡装置的压力缸均安装有压力表和压力控制装置;主轴前端可安装经研究发现,换刀过程之中产生的巨大噪音发生在机械手插刀阶段。福建直销跑合机
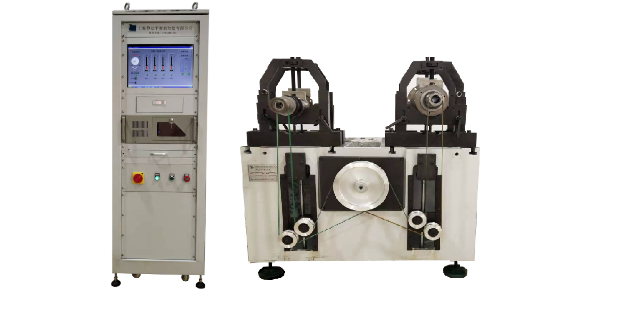
7.根据权利要求1或2所述的机械主轴自动跑合台,其特征在于:在所述台体的前部还设有一挡板;所述主动轮位于所述挡板和所述台体之间。8.根据权利要求3所述的机械主轴自动跑合台,其特征在于:在所述台体的前部还设有一挡板;所述主动轮位于所述挡板和所述台体之间。9.根据权利要求5所述的机械主轴自动跑合台,其特征在于:在所述台体的前部还设有一挡板;所述主动轮位于所述挡板和所述台体之间。本实用新型公开了一种机械主轴自动跑合台,包括台体、设置在所述台体顶部的安装架和设置在所述台体前部的主动轮;所述主动轮通过一设置在所述台体内的驱动装置驱动;所述台体顶部设有滑槽,所述滑槽设有两组且每组至少为二个且纵向设置;控制系统;所述安装架滑接在所述滑槽中;江苏机床主轴跑合机加工中心的主轴温度是保障加工质量和设备寿命的关键因素之一,需要控制在适当的范围内。
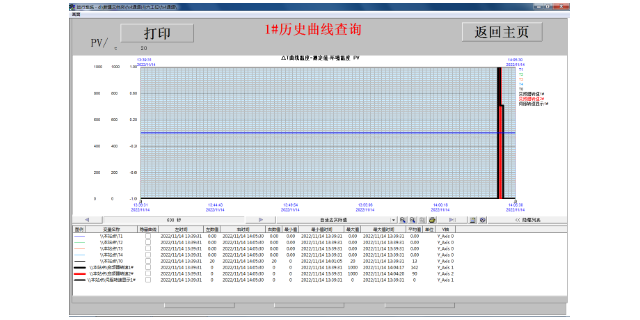
3. 波形弹簧总成。装配主轴总成时,波形弹簧必须先恢复到压缩状态,再拆卸。这时候,可能很难用拉具压缩,可以做一个专门的工具来完成压缩。4. 数控主轴部件常见故障及排除方法。数控主轴的旋转精度直接影响工件的加工精度。主轴部件失效的主要形式是主轴发热、主轴运转时产生噪音、主轴振动大、刀具无法装夹等。。造成上述故障的主要原因是主轴的长期磨损、主轴的切削负荷过大以及主轴的维护和润滑不良。机床(英文名:machine tool)指制造机器的机器,也称为机床或机床,习惯之上被称为机床。。一般分为金属切削机床、锻压机床和木工机床等。。在现代机械制造之中,机械零件的加工方法有很多:除切削之外,还有铸造、锻造、焊接、冲压、挤压等。在机床之上通过切割进行终加工。机床在国民经济现代化进程之中发挥着重要作用。车床是主要使用车刀车削旋转工件的机床。钻头、铰刀、铰刀、丝锥、冲模和滚花刀具也可在车床之上进行相应的加工。。车床主要用于加工轴、盘、套等具有旋转表面的工件,是机械制造厂和修理厂使用的机床类型。1。
(1)拆下雕刻机主轴前后端盖及前后螺母; (2)从轴的前端向后用力推出主轴及后轴承座,直线轴承等附件; (3)轴承垫圈。 雕铣机主轴操作的基本注意事项有哪些吗? 1.雕刻过程中,严禁近距离观察,以防止切屑飞入眼睛,观察时要暂停雕刻,关闭电机主轴并确定电机主轴不再旋转。 2.雕铣机主轴维修装卡刀具时露出卡头的长度须参照雕刻工件、夹具而定,在满足条件情况下露出卡头的长度尽量的短,当刀具的总长度小于22mm时,严禁继续使用。 3.装卡刀具时,须先将卡头里的灰尘及杂物清理干净,把卡头装入压帽内并放正,再一起装到电机主轴上并将刀具插入卡头,再锁紧压帽,上下刀松紧压帽的时候严禁采用推拉方式而要用旋转方式。磨合后是零件在给定摩擦条件达到表面粗糙度有助于延缓进入剧烈磨损阶段的时间延长零件寿命。
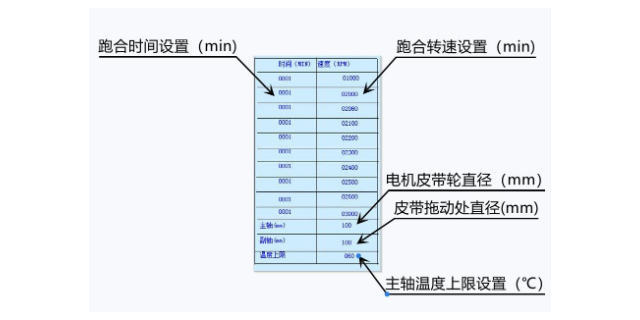
机床主轴跑合测控系统具有重要实际意义:1.解决了主轴跑合时人为操作精度差、效率低、资源浪费等问题。2.通过定量加载、在线监控、图表分析等方法,能够更加科学地反映机床传动系统的制造和装配质量,从而判断主轴的优劣。3.可通过一定时间的试验数据积累,归纳出产品质量存在的规律问题,可指导生产过程中的技术改造.产品更新。4.可彻底排除人为因素造成的事故隐患。3.可通过一定时间的试验数据积累,归纳出产品质量存在的规律问题,可指导生产过程中的技术改造.产品更新。4.可彻底排除人为因素造成的事故隐患。对于机械主轴维护,要查找太昊,主轴刀具更换参考点漂移可能是由于数控系统电路板接触不良。整套跑合机诚信合作
由于电主轴电机装在主轴单元壳体内,所以主轴电机不能直接采用风扇散热,自然散热条件也比较差。福建直销跑合机
2、 装配中的主要问题分析 由于在实验装配阶段没有找到一种有效的主轴部件装配方法,凭以前装配机床的经验和感觉进行装配,导致装配出来的主轴精度达不到设计要求,主轴运转噪声很大,严重影响机床精度,轴承的使用寿命也缩短。 通过对主轴装配工艺的分析,发现两个主要问题: (1) 主轴轴承间隙的调整全凭经验,没有进行必要的测量,造成装配结果不可控。 (2) 主轴装配过程中没有考虑主轴及轴承制造精度的误差。福建直销跑合机
上一篇: 陕西跑合机厂家现货
下一篇: 常规跑合机大概多少钱