浙江系统视觉检测
缺陷检测通常是指对物品表面缺陷的检测,表面缺陷检测是采用先进的机器视觉检测技术,对工件表面的斑点、凹坑、划痕、色差、缺损等缺陷进行检测。南京熙岳智能科技有限公司开发了不少该类检测软件,该系统可根据设定的技术指标要求自动进行检测,并对有缺陷部位进行标识,还可以根据需要自动分拣、剔除。对不良位置进行定位,可控制贴标设备会打印设备进行标识对不良品图像进行自动存储,可进行历史查询自动统计(良品、不良品、总数等)异常时提供声、光报警,并可控制设备停机系统有自学习功能,且学习过程操作简单螺丝、轴承、齿轮等精密部件的长宽高、直径等尺寸测量,划伤、划痕、缺损、等表面缺陷检测。浙江系统视觉检测
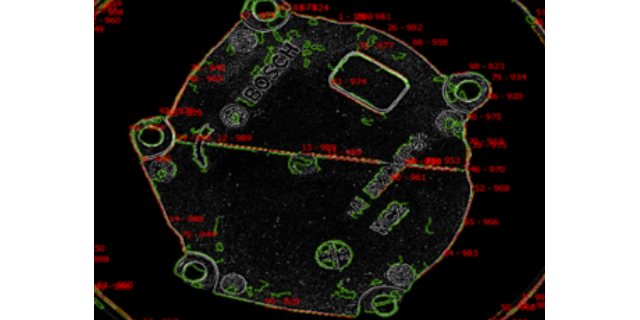
定制机器视觉检测用机器视觉检测方法可以提高生产效率和生产的自动化程度。而且机器视觉易于实现信息集成,是实现计算机集成制造的基础技术。可以在快速的生产线上对产品进行测量、引导、检测、和识别,并能保质保量的完成生产任务。南京熙岳智能科技有限公司市一家专门定制机器视觉检测设备的公司。机器视觉系统的特点是提高生产的柔性和自动化程度。在一些不适合于人工作业的危险工作环境或人工视觉难以满足要求的场合,常用机器视觉来替代人工视觉;同时在大批量工业生产过程中,用人工视觉检查产品质量效率低且精度不高。江西机器人视觉检测定制机器视觉检测服务准确地找到被测零件并确认其位置,上下料使用机器视觉来定位,引导机械手臂准确抓取。
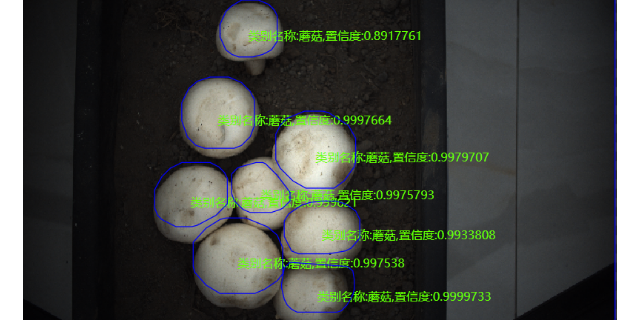
机器视觉检测较常见的问题点有哪些?1、光源与成像:机器视觉中质量的成像是第一步,由于不同材料物体表面反光、折射等问题都会影响被测物体特征的提取,因此光源与成像可以说是机器视觉检测要攻克的难关。比如现在玻璃、反光表面的划痕检测等,很多时候问题都卡在不同缺陷的集成成像上。2、重噪音中低对比度图像中的特征提取:在重噪音环境下,真假瑕疵的鉴别很多时候较难,这也是很多场景始终存在一定误检率的原因,但这块通过成像和边缘特征提取的快速发展,已经在不断取得各种突破。3、对非预期缺陷的识别:在应用中,往往是给定一些具体的缺陷模式,使用机器视觉来识别它们到底有没有发生。但经常遇到的情况是,许多明显的缺陷,因为之前没有发生过,或者发生的模式过分多样,而被漏检。如果换做是人,虽然在操作流程文件中没让他去检测这个缺陷,但是他会注意到,从而有较大几率抓住它,而机器视觉在这点上的“智慧”目前还较难突破。4、嵌入式解决方案发展迅猛,智能相机性能与成本优势突出,嵌入式PC会越来越强大。模块化的通用型软件平台和人工智能软件平台将降低开发人员技术要求和缩短开发周期。
南京熙岳智能科技有限公司在钢铁行业已服务了众多客户,针对不同客户的定制化方案,助力其达到制造行业内的先进地位。未来,南京熙岳智能科技有限公司将继续以绿色发展、低碳发展、提升产品质量、智能制造为原则,助力我国钢铁工业的高质量发展。钢铁行业在我国的经济发展中有着至关重要的地位,钢材是钢铁工业为社会生产和生活提供的产品的主要表现形式,钢铁表面瑕疵检测设备,凝聚了机器视觉领域的多项先进技术应用,利用光学原理,通过图像处理和分析对产品表面可能存在的缺陷进行检测。嵌入式视觉技术主要的应用包括ADAS、工业自动化以及安防监控。
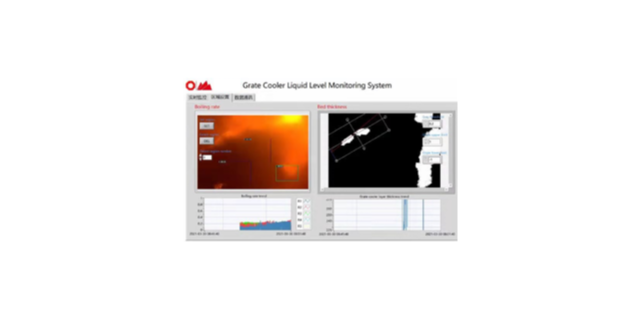
发展迅猛的自动化技术在我国掀起了热潮,我们对机器视觉的认识加深,每个人对它的看法发生了巨变。机器视觉系统让大批量、持续生产的自动化程度提高了,提高了为工业生产效率和产品精度,同时获取信息与自动处理的能力变得极其快,为工业生产的信息集成提供了有效途径。机器视觉技术不断成熟和进步,应用范围变得越来越宽泛。目前这机器视觉应用基本可以概括出机器视觉技术在工业生产中能够起到的作用。南京熙岳智能科技有限公司也跟上这快速的步伐。公司是一家集研发、专属定制、及销售为一体的高新科技企业,致力于智能工厂、精益生产、工业工程设计(IE)生产力解决方案,在生产制程所需的机器视觉检测、AGV无人搬运、自动化设备及系统集成等领域广泛应用于工业自动化。定制机器视觉检测服务可以长时间地作测量、分析和识别任务。安徽工业视觉检测系统
彩色相机用于产品颜色提取学习,分析获得产品颜色信息进而检测输出产品颜色个数、色差、色序等关键指标。浙江系统视觉检测
机器视觉是人工智能正在快速发展的一个分支。简单说来,机器视觉就是用机器代替人眼来做测量和判断。机器视觉系统是通过机器视觉产品(即图像摄取装置,分CMOS和CCD两种)将被摄取目标转换成图像信号,传送给专门的图像处理系统,得到被摄目标的形态信息,根据像素分布和亮度、颜色等信息,转变成数字化信号;图像系统对这些信号进行各种运算来抽取目标的特征,进而根据判别的结果来控制现场的设备动作。南京熙岳智能科技有限公司给客户定制的一些设备都是运用机器视觉来解决的。浙江系统视觉检测
上一篇: 福建ccd视觉检测设备
下一篇: 北京机器视觉检测