北京准干式切削系统价格怎么样
准干式切削是一种先进的切削加工技术,它结合了干式切削和液体冷却切削的优点,具有高效、环保、节能等特点,被普遍应用于金属加工领域。准干式切削是指在切削过程中,通过喷射冷却液体形成薄膜覆盖在刀具和工件接触区域,以降低切削温度和摩擦系数,从而减少切削力和切削温度的技术。相比传统的液体冷却切削,准干式切削不需要大量的冷却液体,减少了对环境的污染,同时也降低了加工成本。准干式切削的优点之一是提高了切削效率。由于喷射冷却液体形成的薄膜可以有效降低切削温度,减少了刀具磨损和切削力,从而提高了切削速度和加工效率。此外,准干式切削还可以减少切削液体的使用量,节约了液体冷却切削中需要处理和回收的废液量,进一步提高了加工效率。准干式切削可以用于金属、塑料和木材等材料的加工。北京准干式切削系统价格怎么样
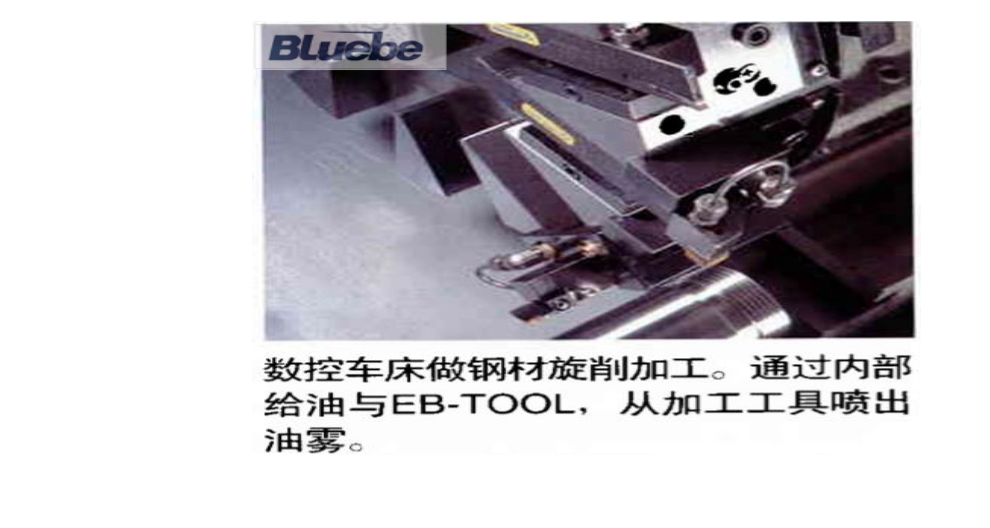
准干式切削具有更好的切削质量和表面质量。由于不使用大量的液体冷却剂,减少了切削区域的温度变化,减小了切削区域的热影响,从而减少了切削过程中的刀具磨损和变形,提高了切削质量和表面质量。准干式切削还可以降低切削成本。传统的液体冷却切削需要大量的液体冷却剂和冷却设备,而准干式切削只需要微量的液体冷却剂和简单的喷射装置,很大程度降低了切削成本。综上所述,准干式切削是一种高效、环保、经济的切削加工技术。它不只减少了对环境的污染和对水资源的消耗,还提高了切削质量和表面质量,降低了切削成本。相信在未来的发展中,准干式切削将会得到更普遍的应用。北京准干式切削系统价格怎么样准干式切削的机床结构要稳定牢固。
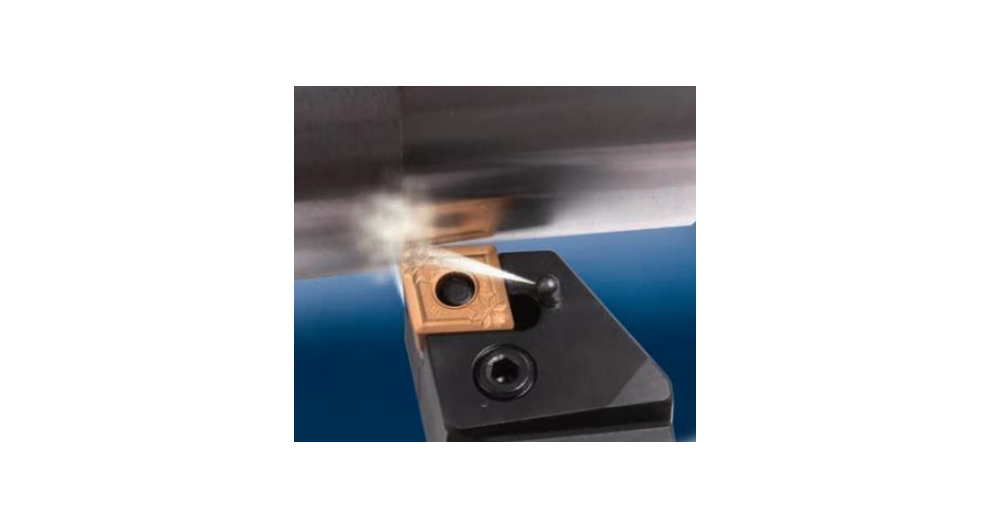
准干式切削的关键技术是切削液的喷射方式和喷射位置的控制。通过优化喷射参数,可以实现切削液的较好喷射效果,减少切削液的溅射和飞溅,提高切削效率和工件表面质量。此外,准干式切削还可以减少切削液的使用量,降低切削成本,同时减少对环境的影响。准干式切削在工业生产中具有普遍的应用前景。首先,它可以提高切削效率,减少生产时间和成本。相比传统的液体冷却切削,准干式切削可以更好地控制切削液的喷射位置和喷射方式,从而减少切削液的浪费和溅射。其次,准干式切削可以提高工件的表面质量。切削液的喷射可以冷却刀具和工件,减少切削温度和切削力,从而减少切削振动和刀具磨损,提高工件的表面光洁度和精度。然后,准干式切削可以减少切削液的使用量,降低对环境的影响。传统的液体冷却切削会产生大量的废液,对环境造成污染,而准干式切削可以减少切削液的使用量,降低废液的排放量,更加环保。
准干式切削具有出色的切削效率。因为没有切削液的介入,准干式切削能更有效地将切削力传递给工件,提高切削效能。相比湿式切削,准干式切削的加工时间更短,生产效率更高。而且,准干式切削不会产生黏糊的切削液,也无需花费时间清理工件和切削液,节省了加工周期,提高了效率。此外,准干式更换切削液,增加了材料和人力成本,而准干式切削只需要定期清洗和维护气流系统,更加方便和经济。同时,准干式切削不需要大量的切削液,降低了材料采购成本,也减少了废液处理所带来的环境压力和费用。准干式切削可以采用数控技术自动化生产。

准干式切削技术的使用可以减少冷却液的使用量。传统的切削加工过程中,需要大量的冷却液来冷却工件和刀具,以防止过热和摩擦。然而,冷却液的使用不只会增加生产成本,还会产生大量的废液,对环境造成污染。而准干式切削技术则通过优化刀具和工件的材料和结构,使得切削过程中产生的热量和摩擦得到有效控制,从而减少了对冷却液的需求。准干式切削技术能够降低废液的排放量。传统的切削加工过程中,冷却液在切削过程中不断流动,与切屑和金属粉末混合在一起,形成废液。这些废液需要经过处理才能排放或回收利用。而准干式切削技术的使用可以减少废液的产生,从而降低了对环境的影响。随着切削速度的提高,单位时间内的材料切除率增加,切削加工时间减少,从而可大幅度提高加工效率。扬州先进准干式切削系统一般多少钱
准干式切削需要结合润滑液和切削参数进行综合优化。北京准干式切削系统价格怎么样
准干式切削的工作原理可以简单地分为两个方面:冷却和润滑。首先是冷却。在切削过程中,切削区域会产生大量的热量,如果不及时冷却,会导致刀具过热,从而影响切削质量和刀具寿命。准干式切削通过喷射切削液和空气的混合物来冷却切削区域,有效地降低切削温度,保持刀具的稳定性和切削质量。其次是润滑。切削液的主要作用是减少切削过程中的摩擦和磨损,从而延长刀具的使用寿命。在准干式切削中,切削液和空气的混合物会形成一个湿润的切削环境,润滑切削区域,减少摩擦和磨损,提高切削质量和刀具寿命。准干式切削的工作原理还涉及到切削液和空气的喷射方式。通常,切削液和空气会通过喷嘴喷射到切削区域,形成一个密集的切削液和空气混合物流,覆盖整个切削区域。这种喷射方式可以确保切削液和空气均匀地分布在切削区域,提供稳定的冷却和润滑效果。北京准干式切削系统价格怎么样
上一篇: 常州机床微量润滑哪家便宜
下一篇: 连云港准干式切削系统定制