无锡在线检测系统定制
常用的探伤方法有:X光射线探伤、超声波探伤、磁粉探伤、渗透探伤(着色探伤)、涡流探伤、γ射线探伤、萤光探伤等方法。探伤检测是指探测金属材料或部件内部的裂纹或缺陷。原理:它的基本原理是:当工件磁化时,若工件表面有缺陷存在,由于缺陷处的磁阻增大而产生漏磁,形成局部磁场,磁粉便在此处显示缺陷的形状和位置,从而判断缺陷的存在。适用范围,磁粉探伤是用来检测铁磁性材料表面和近表面缺陷的种检测方法。原理,超声波在介质中传播时有多种波型,检验中较常用的为纵波、横波、表面波和板波。用纵波可探测金属铸锭、坯料、中厚板、大型锻件和形状比较简单的制件中所存在的夹杂物、裂缝、缩管、白点、分层等缺陷;用横波可探测管材中的周向和轴向裂缝、划伤、焊缝中的气孔、夹渣、裂缝、未焊透等缺陷;用表面波可探测形状简单的制件上的表面缺陷;用板波可探测薄板中的缺陷。外观检测用于检查产品外部的形象和细节。无锡在线检测系统定制
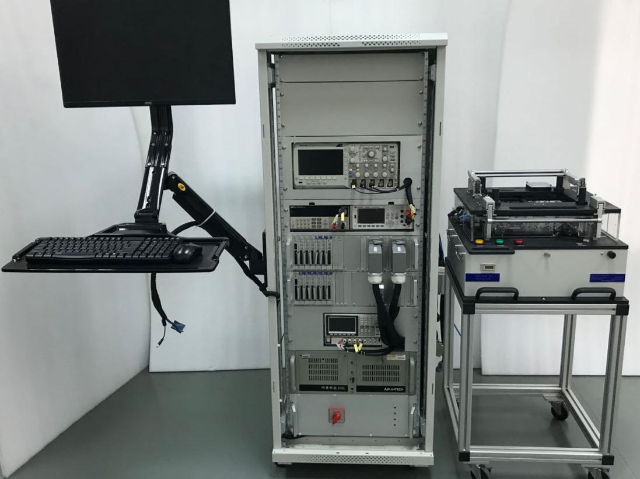
直径检测,在行进中的棒、线、管材直径的检测,宜采用非接触式检测,常用的方法是用光电式检测系统。直径检测传感器大致分激光扫描直径检测传感器,CCD投影直径检测传感器,激光衍射直径检测传感器,而激光扫描直径检测传感器是用得较多的一种。激光扫描直径检测传感器是根据光学的几何原理设计而成,激光适应性强、安装使用方便、测量精度高,与计算机技术相结合可达到智能控制测量数据,同时有的激光扫描测径传感器可以通过网络实现远程控制。上海PCBA检测供应及时的检测与反馈有助于生产过程的优化。
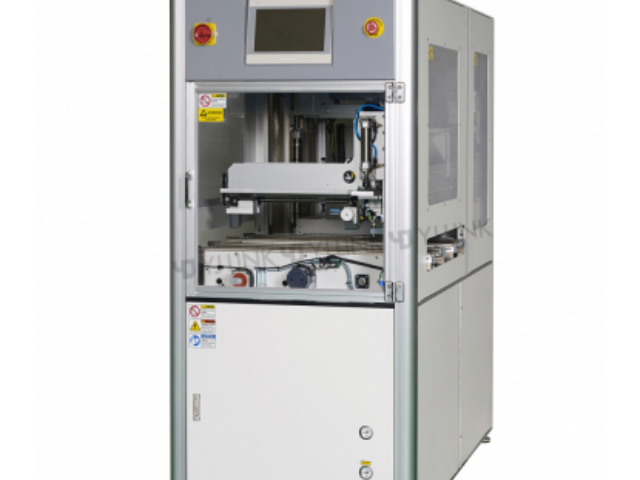
光学摄像头,光学摄像头的任务就是进行光学成像,一般在测量领域都又专门的用于测量的摄像镜头,因为其对成像质量有着关键性的作用。摄像头需要注意的一个问题是畸变。这个就需要使用相应的畸变校正方法,目前也开发出了很多自动畸变自动校正系统。CCD 摄像机及图像采集卡,CCD( Charge Coupled Device) 摄像机及图像采集卡共同完成对目标图像的采集与数字化。目前 CCD,CMOS等固体器件的应用技术,线阵图型敏感器件,像元尺寸不断减小,阵列像元数量不断增加,像元电荷传输速率也得到大幅提高。在基于PC机的机器视觉系统中,图像采集卡是控制摄像机拍照来完成图像的采集与数字化,并协调整个系统的重要设备。图像采集卡直接决定了摄像头的接口为:黑白、彩色、模拟、数字等形式。
机器视觉检测的特点是提高生产的柔性和自动化程度。在一些不适合于人工作业的危险工作环境或人工视觉难以满足要求的场合,常用机器视觉来替代人工视觉;同时在大批量工业生产过程中,用人工视觉检查产品质量效率低且精度不高,用机器视觉检测方法可以较大程度上提高生产效率和生产的自动化程度。而且机器视觉易于实现信息集成,是实现计算机集成制造的基础技术。照明系统按其照射方法可分为:背向照明、前向照明、结构光和频闪光照明等。其中,背向照明是被测物放在光源和摄像机之间,它的优点是能获得高对比度的图像。前向照明是光源和摄像机位于被测物的同侧,这种方式便于安装。结构光照明是将光栅或线光源等投射到被测物上,根据它们产生的畸变,解调出被测物的三维信息。频闪光照明是将高频率的光脉冲照射到物体上,摄像机拍摄要求与光源同步。检测数据的管理和分析至关重要,有助于优化生产过程、提高产品质量。
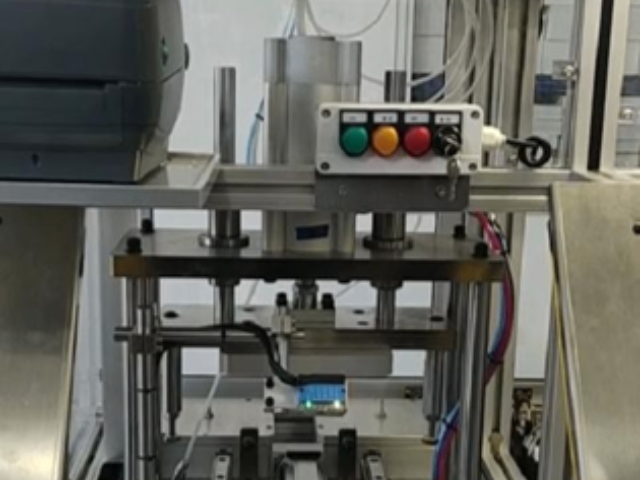
接着,目标识别是通过将特征与预先定义的模型或参考数据进行匹配,从而确定图像中的目标或感兴趣区域。目标识别可以使用不同的算法和技术,例如模板匹配、边缘检测、机器学习等。较后,分类是将目标或感兴趣区域进行分类和标记。分类可以根据不同的要求进行,例如根据目标的类别、行为或属性进行分类。常用的分类方法包括支持向量机、神经网络、决策树等。视觉检测的原理与人类视觉系统的原理有相似之处。人类视觉系统通过眼睛采集图像信息,然后通过大脑对图像进行分析和解释。同样地,计算机通过摄像机或其他图像采集设备获取图像信息,然后通过图像处理和模式识别方法对图像进行分析和解释。检测设备的精确性对产品质量至关重要。嘉兴离线检测按需定制
膜厚检测用于测量薄膜或涂层的厚度。无锡在线检测系统定制
交通监控领域中的应用,智能交通监控领域中,在重要的十字路口安放摄像头,就可以利用摄像头的快速拍照功能,实现对违章、逆行等车牌的车牌进行自动识别、存贮,以便相关的工作人员进行查看。在桥梁检测领域中的应用,人工检测法和桥检车法都是依靠人工用肉眼对桥梁表面进行检测,其速度慢,效率低,漏检率高,实时性差,影响交通,存在安全隐患,很难大幅应用;无损检测包括激光检测、超声波检测以及声发射检测等多种检测技术,它们仪器昂贵,测量范围小,不能满足日益发展的桥梁检测要求;智能化检测有基于导电性材料的混凝土裂缝分布式自动检测系统和智能混凝土技术,也有较前沿的基于机器视觉的检测方法。无锡在线检测系统定制
上一篇: 台州探伤检测支持定制
下一篇: 江苏治具批发