摩托车驱动轴制作
随着全球汽车行业的快速发展,提高生产效率和降低成本成为了制造商面临的重要挑战。模块化驱动轴的设计与制造是应对这一挑战的有效策略之一。模块化设计是一种将复杂产品分解为多个模块或组件的设计方法。在驱动轴的设计与制造中,这意味着将驱动轴分解为若干个单独的模块,每个模块都具有特定的功能和接口。这种设计使得每个模块可以单独设计、测试和制造,从而快速组装成完整的驱动轴。 模块化设计的优势在于提高了设计的灵活性和可扩展性,简化了产品开发流程,缩短了研发周期。同时,当需要对产品进行升级或修改时,只需更换或改进相应的模块,而无需重新设计整个产品。在应对紧急加速或急转弯时,三段式驱动轴能够迅速响应,提供良好的操控稳定性。摩托车驱动轴制作
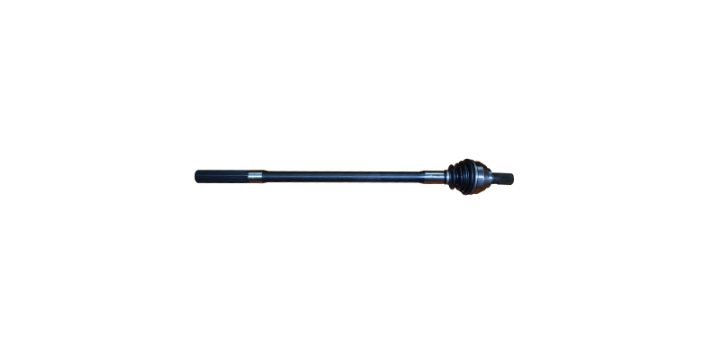
在汽车制造中,驱动轴是关键的组件之一,它负责将动力从传动系统传递到车轮。因此,驱动轴的性能直接影响到汽车的驾驶效率和安全性。选择合适的材料对于优化驱动轴的性能至关重要。因此,不同材料在驱动轴制造中的应用及其性能特点,以及如何通过材料选择来优化驱动轴的性能是很重要的。只有通过合理选择材料和采用先进的热处理技术,才可以明显优化驱动轴的性能,满足不同汽车应用的需求。随着新材料和新技术的发展,未来驱动轴的性能有望进一步提升,为汽车工业的进步做出贡献。深圳新能源车驱动轴制造基于扭矩传感器信号的控制策略可以实时调整驱动轴的输出扭矩,实现稳定的扭矩传递。
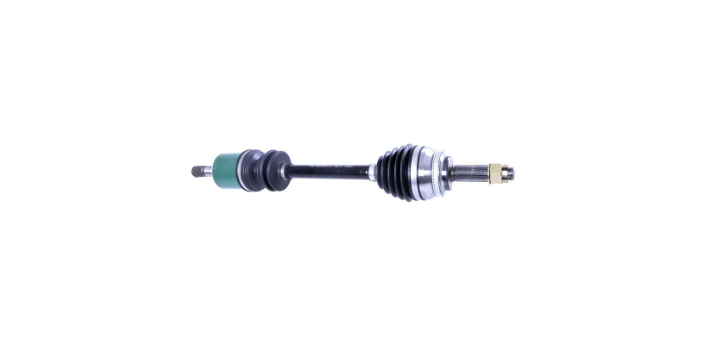
驱动轴在新能源汽车中的独特应用特点有哪些? 1、高扭矩输出的适应性:电动汽车的动力源由电动机取代传统内燃机,其扭矩输出特性更为直接且高效。因此,驱动轴需具备更强的扭矩承载能力,以应对电动机瞬间释放的高扭矩,确保动力传输的平稳与高效。 2、高效能与低噪音要求:新能源汽车追求的是高效能与低能耗的完美结合,同时要求更低的运行噪音以提升驾驶体验。驱动轴作为关键传动部件,其设计需充分考虑减少能量损失、提高传动效率,并通过精密加工与优化设计实现低噪音运行。 3、集成化与智能化趋势:随着汽车电子化、智能化程度的提高,驱动轴也逐渐向集成化、智能化方向发展。例如,通过集成传感器与智能控制单元,实现对驱动轴状态的实时监测与故障预警,提升车辆的安全性与可靠性。
智能化驱动轴技术的发展还包括故障预警系统的完善。该系统利用先进的算法分析监测到的数据,能够及时发现异常模式,预警潜在的故障。这种预警机制极大地提高了行驶的安全性,减少了因驱动轴故障导致的事故风险。故障预警系统还可以与车辆的维护系统整合,自动记录故障代码和相关信息,便于维修人员快速诊断问题并进行维修。 另一项重要的研发成果是智能化驱动轴的自动调整传动效率功能。这项功能通过对驱动轴的实时监测和控制,可以优化传动系统的响应和效率。例如,根据路况和驾驶模式,系统可以自动调整扭矩分配,提高燃油经济性,减少排放。自动调整功能不只提升了驾驶体验,还有助于延长驱动轴和其他传动部件的使用寿命,因为它们始终在更佳状态下运行。等速驱动轴的设计影响着车辆的燃油效率,优化设计有助于减少能量损失。
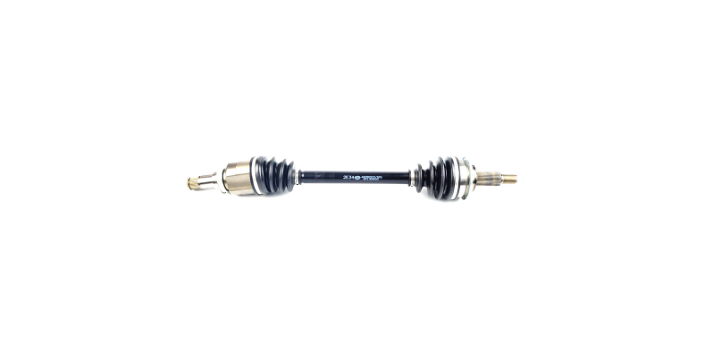
在自动驾驶汽车中,驱动轴必须能够实现高精度的传动控制。这是因为自动驾驶车辆需要精确控制加速、减速和转向,以适应复杂的交通环境。为了达到这一目标,制造商正在开发具有高分辨率传感器和精密控制系统的智能驱动轴。 这些系统通过实时监控车辆的动力输出和行驶状态,能够快速准确地调整驱动轴的扭矩和转速,确保车辆的平稳行驶和动态响应。此外,结合先进的算法和机器学习技术,驱动轴控制系统能够预测路况变化,并提前做出调整,从而提高驾驶的平顺性和安全性。驱动轴的强度和刚性直接影响汽车的操控性和乘坐舒适性。广州商务车驱动轴厂商
驱动轴是一条旋转轴,将发动机的动力传输到车轮。摩托车驱动轴制作
驱动轴的制造是一项系统工程,它融合了材料科学、机械设计、精密加工与热处理技术等多领域的精髓。从原材料的选择开始,就需严格把关,确保所选材料既满足更高的强度、高耐磨性的要求,又具备良好的可加工性和经济性。 1、材料选择:根据驱动轴的使用环境和性能要求,精选好的合金钢、铝合金或复合材料等,确保材料本身的稳定性和耐用性。 2、精密加工:采用高精度数控机床进行车削、铣削、磨削等加工工序,确保驱动轴各部位的尺寸精度、形状精度和位置精度达到设计要求。同时,通过先进的刀具技术和冷却液系统,减少加工过程中的热变形和残余应力。 3、热处理:通过淬火、回火等热处理工艺,改善材料的内部组织结构和力学性能,提高驱动轴的强度和韧性。热处理过程中需严格控制温度、时间和冷却速度等参数,以确保热处理效果的一致性。 4、装配与调试:在完成所有加工和热处理工序后,进行精密的装配与调试工作。确保驱动轴与变速箱、驱动轮等部件之间的配合间隙合理、运转平稳。摩托车驱动轴制作
上一篇: 深圳农用车万向节定制
下一篇: 深圳电机驱动轴定制厂家