精密塑胶模具设计
塑料模具的加工要点:首先、如何加快产品的成型周期?优化模具结构设计和冷却系统是关键。当然,良好的高稳定性的注塑机也是比较必要的。第二、合理选择高精度的模具加工设备与项目跟进团队、QC部门去落实整个项目,这将直接导致客户后期花更少的时间修改和调整模具。并且合理的加工工艺选择会缩短整个塑料模具的加工时间。第三、一副好的模具必须在高速运行下有较长的工作寿命。要做到这一点,就必须使用高质量的塑料模具材料和零件。也保持塑料模具结构的简单,易于客户在自己的工厂中方便维护。第四、与瓶颈的互配性。通常情况下,如果上述要求落实好,那么装配就是没有问题的。瓶盖有这较为完整统一的质量标准和口径参数等,因而说瓶盖的生产制作是相对标准的。精密塑胶模具设计
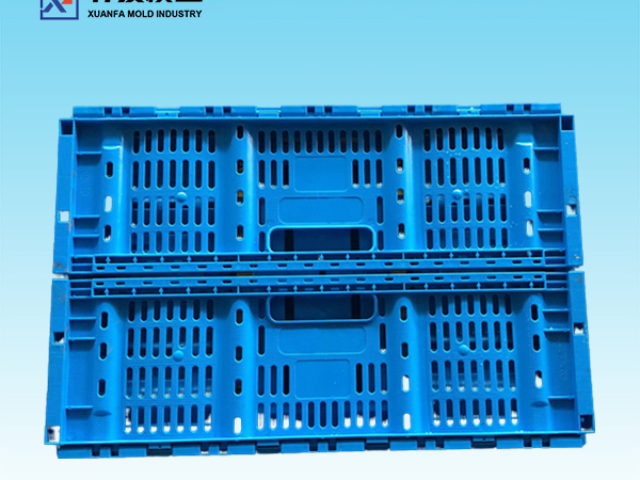
塑料模具选用国际抢先的二级双锥度定位技术,每腔独自自锁,保证模具同心度,良好的冷系统完成常温水冷却的高效率,并且免剪浇口,降低工人劳动强度,模具寿命至少300万次模次。在塑料模具注塑成型的过程中,温度的控制是极其重要的,它不只会影响到制品的质量还会影响到其成型周期。不同的塑料具有不同的流动性,所以其温度控制也不相同。流动性好的塑料,一般控制在60℃左右;流动性差的塑料,一般控制在80℃到120℃之间。另外,结晶塑料和非结晶塑料的冷却过程也不相同,这点在注塑过程中要注意区别。成都塑胶模具原理塑料模具的数控加工具有一定典型性,并比一般产品的数控加工有着更高的要求。
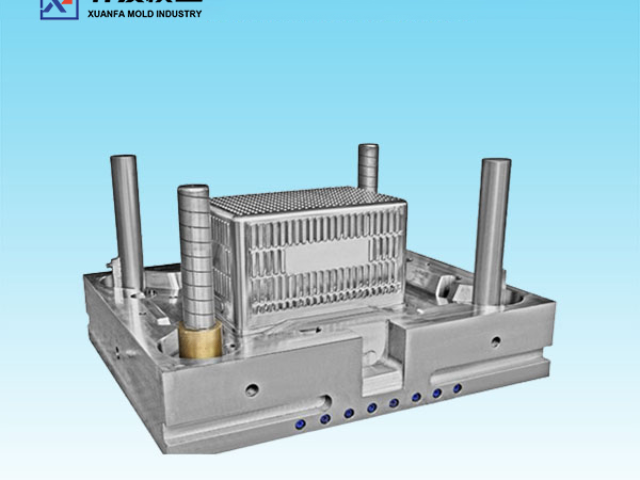
目前常用的日用化妆塑料模具抛光方法:1、电解抛光:电解抛光基本原理与化学抛光相同,即靠选择性的溶解材料表面微小凸出部分,使表面光滑。与化学抛光相比,可以消除阴极反应的影响,效果较好。电化学抛光过程分为两步:(1)宏观整平溶解产物向电解液中扩散,材料表面几何粗糙下降,Ra>1μm。(2)微光平整阳极极化,表面光亮度提高,Ra<1μm。2、日用化妆塑料模具超声波抛光:将工件放入磨料悬浮液中并一起置于超声波场中,依靠超声波的振荡作用,使磨料在工件表面磨削抛光。超声波加工宏观力小,不会引起工件变形,但工装制作和安装较困难。超声波加工可以与化学或电化学方法结合。在溶液腐蚀、电解的基础上,再施加超声波振动搅拌溶液,使工件表面溶解产物脱离,表面附近的腐蚀或电解质均匀;超声波在液体中的空化作用还能够阻止腐蚀过程,利于表面光亮化。
哪些原因会影响到塑料模具的成型:(1)、型胚构成阶段聚合物在挤出机中的输送、熔融、混炼、泵出成型为型胚的构成阶段;在这一阶段,影响塑料模具壁厚散布的主要工艺参数有:①材料的分子量散布、平均分子量;②吹塑机的温度控制系统和螺杆转速,其间温度控制系统包含料斗温度,料筒1区、2区、3区、4区温度,法兰温度,以及储料模头1区、2区、3区、4区温度。(2)、吹瓶模型胚下料阶段型胚从模唇与模芯的空隙中挤出为下料阶段。此时,型胚离模胀大和型胚垂伸这两种现象影响型胚成型。影响壁厚散布的主要工艺参数是吹塑机的模头直径和壁厚控制系统,其间控制系统包含轴向壁厚控制系统和周向壁厚控制系统,以调整模唇与模芯的空隙。塑料模具厂的脱模方法:加入添加剂。
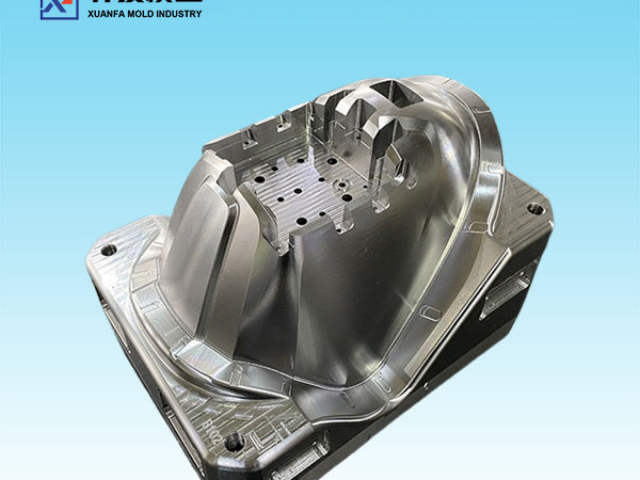
电器塑料模具:电器行业对塑料模具的需求日益增长,主要因为塑料部件在电器产品中扮演着越来越重要的角色。从电视机的外壳到电脑键盘,从家用电器的控制面板到智能手机的内部结构,电器塑料模具不只要满足美观、轻便的要求,还要具备优良的电气性能、耐热性和耐腐蚀性。因此,电器塑料模具的设计与制造需要综合考虑材料选择、结构设计、注塑工艺等多个方面。随着电器产品的智能化和多样化,电器塑料模具也在不断创新,以适应市场的新需求。塑料模具的具体优势:多腔点。北京电器塑胶模具生产
塑料模具如果带有油压接头、气压接头、热流道元件接线板时,应将它们尽可能放置在非操作面,以利操作。精密塑胶模具设计
塑料模具安装完毕,试模前,要对模具进行预热,模具预热的方法大致有两种。是利用模具本身的冷却水孔,通入热水进行加温。目前国内外有模具加温器被大量采用,是模具加温的一种好方法。另外是外加热法。即将铸铝加热板安装在模具外部,从外向内进行加温,这种方法加热快,但消耗热能大。对于北方寒冷的冬季比较适合。对于塑料模具,可以靠注射料的热量来提高温。采用注射不困难的原料也无需进行模具预热。但是,对于大中型模具,采用离温料、高压力将熔料強行注射至摸腔内,尽管也可以得到试模的制件,可是实际上对模具自身损伤比较严重,又浪费能源,同时所得到的制件因内应力大,变形严重,其尺寸比较不稳定,给制件品尺寸的检验带来麻烦。因而这种方法不宜采用。模具安装后预热的同时,注射机筒也在加温,当两者温度均符合要求时,即模具温度达30?60℃以上时。机筒内塑料已呈熔融状态时,并塑化均匀,视为温度合适,即具备了试模注射条件,试模可以进入试注射阶段。精密塑胶模具设计
上一篇: 广州包胶注塑模具生产
下一篇: 南京周转箱注塑模具制作