深圳塑料椅子注塑模具制造
浇注系统浇注系统是指塑料从射嘴进入型腔前的流道部分,包括主流道、冷料穴、分流道和浇口等。浇注系统又称流道系统,它是将塑料熔体由注射机喷嘴引向型腔的一组进料通道,通常由主流道、分流道、浇口和冷料穴组成。它直接关系到塑料制品的成型质量和生产效率。主流道它是模具中连接注塑机射嘴至分流道或型腔的一段通道。主流道顶部呈凹形以便与喷嘴衔接。主流道进口直径应略大于喷嘴直径(0.8mm)以避免溢料,并防止两者因衔接不准而发生的堵截。进口直径根据制品大小而定,一般为4-8mm。主流道直径应向内扩大呈3°到5°的角度,以便流道赘物的脱模。对热固性塑料来说,高一点的模具温度通常会减少循环时间,且时间由零件冷却所需时间决定。深圳塑料椅子注塑模具制造
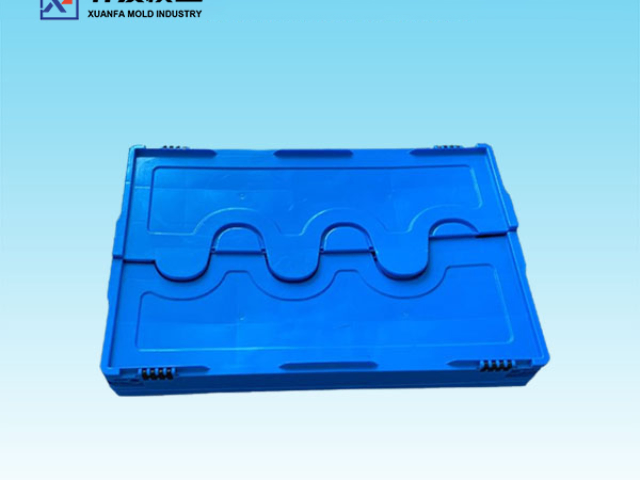
注塑精密加工是一门知识面广,技术性和实践性很强的行业。注塑精密加工生产过程中需使用塑胶原料、色粉、水口料、模具、注塑机、周边设备、工装夹具、喷剂、各种辅料及包装材料等,这些给注塑车间的管理带来了很大的工作量和一定的难度,与其它行业或部门相比,对注塑车间各级管理人员的要求更高,那么注塑精密加工生产怎么运作的呢?注塑精密加工生产需要24小时连续运作,一般为两班倒方式,注塑车间的工作岗位多、职责分工繁杂,对不一样岗位人员的技能要求也亦不一样。要想使注塑车间的生产运作顺利,需要对每个环节和各个岗位所涉及的人员、物料、设备、工具等进行管理,主要包括:原料房、碎料房、配料房、生产现场、後加工区、工具房、半成品区、办公室等区域的运作与协调管理工作。西安注塑模具工艺流程模具内部,由塑料带来的热量通过热辐射传递给材料和模具的钢材,通过对流传递给导热流体。
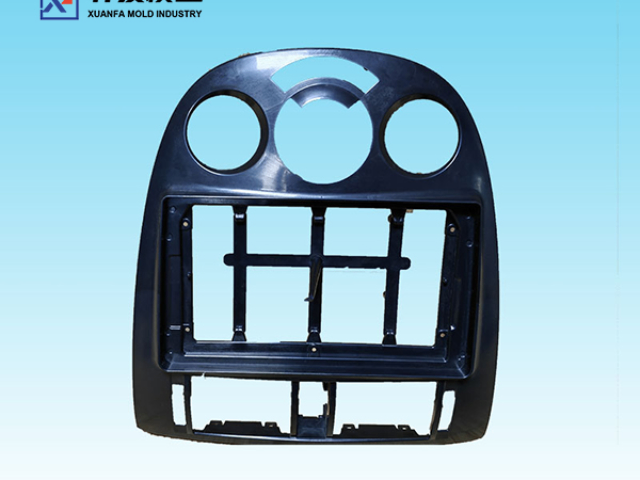
注塑模具厂的好坏怎么看?1.考察注塑模具厂家的公司规模:如厂房面积,员工人数,企业文化等,是否做过类似的产品,较好在前期考察的时候多提出一些比较有针对性的专业问题,让对方回答,这样就能探针模厂的大概实力,2.考察注塑模具厂的生产能力:现在电子行业竞争比较激烈,比较多客户对注塑产品的尺寸精度要求也越来越高,而想要做出好品质的产品是离不开先进的加工设备,即使技术再精湛的技术人员没有好的生产设备也是无法做出好品质的产品,因此在考察注塑模具厂的时候需要到厂家的车间对整体的生产设备做一个详细的评估,如前端的模具加工,注塑加工设备,以及后续的喷油丝印加工设备等等。
大型注塑模具的机器设计:钢铁铸件和能够处理热量的心轴。任何一台用来打磨大型部件的机器重要的设计就是大型的钢铁铸件和一根能够处理热量的心轴。在机器成型、增强硬度和降低热量等方面,钢铁铸件仍然是稳定的材料。至于心轴,则必须采用内部技术来进行冷却,以确保心轴不会自燃或者由于高温产生误差。为了使大型注塑模具的表面达到较好的质量要求,需要一台机器和工具来大幅度减少二次放电加工和手工抛光的时间。加工大型注塑模具通常都需要几天的时间,由于在加工的时候,外部条件会发生变化,要达到必要的精确度,就必须考虑到这些变化。一台不是用来切割大型注塑模具的机器在室温10摄氏度的情况下会改变6度机器圆柱的温度,也会导致轴心角平面发生0.070mm的改变。注塑成型是批量生产某些形状复杂部件时用到的一种加工方法。
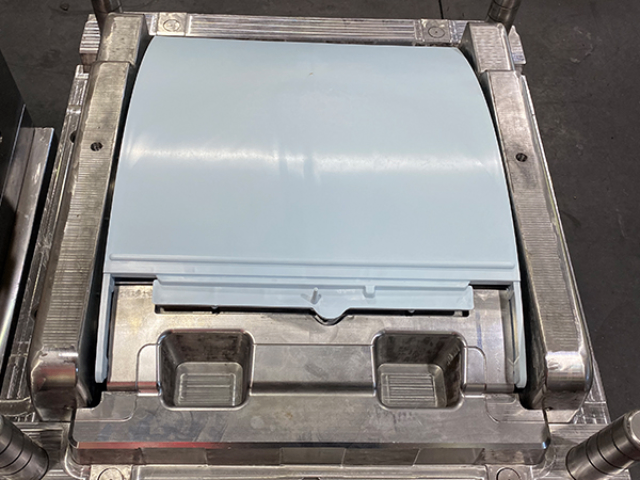
注塑模具保养技巧:1、加工企业首先应给每副模具配备履历卡,详细记载、统计其使用、护理(润滑、清洗、防锈)及损坏情况,据此可发现哪些部件、组件已损坏,磨损程度大小,以提供发现和解决问题的信息资料,以及该模具的成型工艺参数、产品所用材料,以缩短模具的试车时间,提高生产效率。2、加工企业应在注塑机、模具正常运转情况下,测试模具各种性能,并将末尾成型的塑件尺寸测量出来,通过这些信息可确定模具的现有状态,找出型腔、型芯、冷却系统以及分型面等的损坏所在,根据塑件提供的信息,即可判断模具的损坏状态以及维修措施。被导热流体吸收的热量由模温机来带走。苏州电器外壳注塑模具一般多少钱
每套塑料模具的设计、制造成本必须要做到及时汇总。深圳塑料椅子注塑模具制造
影响注射模冷却的因素比较多,如塑件的形状和分型面的设计,冷却介质的种类、温度、流速,冷却管道的几何参数及空间布置,模具材料,熔体温度,塑件要求的顶出温度和模具温度、塑件和模具间的热循环交互作用等。(1)低的模具温度可降低塑件的成型收缩率。(2)模具温度均匀、冷却时间短、注射速度快可以减小塑件的翘曲变形。(3)对于结晶性聚合物,提高模具温度可使塑件尺寸稳定,避免后结晶现象,但是将导致成型周期延长和塑件发脆的缺陷。(4)随着结晶型聚合物的结晶度的提高,塑料的耐应力开裂性降低,因此降低模具温度是有利的。但对于高粘度的无定型聚合物,由于其耐力开裂性与塑件的内应力直接相关,因此提高模具温度和充模速度,减少补料时间有利的。深圳塑料椅子注塑模具制造
上一篇: 南京水桶注塑模具多少钱
下一篇: 杭州玩具注塑模具制造厂