福建自动压铸模具厂家
模具材料与热处理:1.模具材料选择:铝压铸模具通常选用耐热合金钢,如H13、SKD61等,以保证模具在高温下的强度和硬度。2.热处理工艺:通过热处理工艺,如淬火和回火,可以提升模具钢材的硬度、耐磨性和抗疲劳性能。四、模具制造过程1.机械加工:采用数控机床、电火花机、磨床等设备进行模具的粗加工和精加工。2.抛光和研磨:通过抛光和研磨工序,确保型腔表面光滑,以便铸件脱模和减少铸件表面缺陷。3.检测与调试:使用三坐标测量仪、投影仪等检测设备对模具尺寸进行精确测量,确保制造精度。精确控制模具温度和压力是确保压铸产品质量稳定的关键。福建自动压铸模具厂家
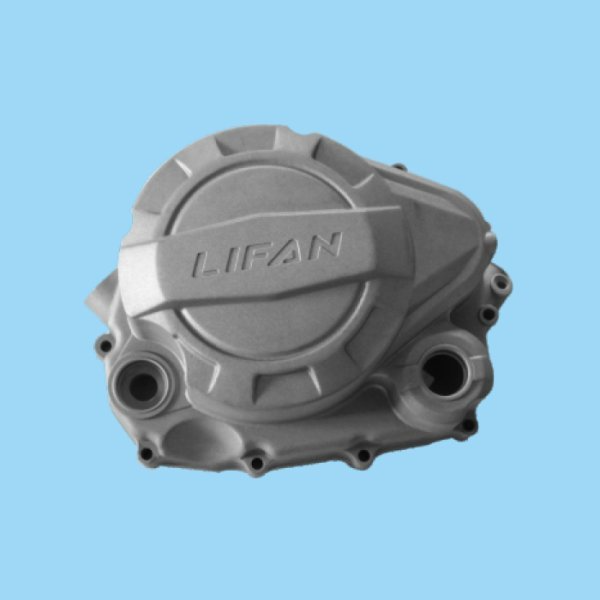
压铸模具的设计遵循“一模一腔”或“一模多腔”的原则,旨在以较少的模具成本生产出符合设计要求的高质量产品。设计过程中需考虑以下几个方面:分型面选择:分型面的合理布局直接影响模具的复杂程度、制造成本及产品质量。浇口设计:浇口的位置、形状和尺寸直接影响金属的流动性和填充效果,需根据产品形状、材料特性等因素综合确定。冷却系统设计:有效的冷却系统能够缩短生产周期,提高产品质量,减少模具热应力。顶出机构设计:合理的顶出机构设计能够确保产品顺利脱模,避免变形或损坏。浙江自动压铸模具多少钱在压铸过程中,模具需要定期检查和更换,以保持较佳性能。
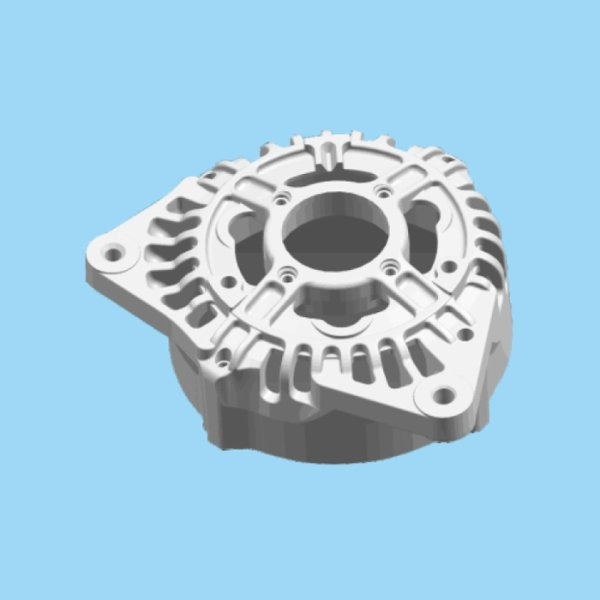
关于导向与定位机构:确保定模和动模在合模过程中的精确对位,防止错位和飞边。顶出机构:用于将凝固后的零件从模具中顶出,便于取件。压铸模具的设计要点在设计压铸模具时,需要考虑以下要点:模具材料的选择:应根据零件的材料、生产批量和模具寿命等因素,选择合适的模具材料。分型面的确定:分型面的选择直接影响到模具的结构和零件的脱模。浇道和排气系统的设计:合理的浇道设计可以确保金属流动顺畅,排气系统则有助于排除型腔内的气体,防止气泡产生。
技术创新智能化设计制造:借助人工智能、大数据等先进技术,实现压铸模具的智能化设计、制造和管理,提高生产效率和产品质量。新材料应用:开发高性能的模具材料,如高强度钢、高温合金、陶瓷基复合材料等,以满足更高精度、更长寿命的模具需求。精密加工技术:发展超精密加工技术,如纳米加工、激光加工等,进一步提高模具的加工精度和表面质量。面临的挑战成本控制:随着原材料价格、人工成本的不断上升,如何有效控制模具制造成本成为企业面临的重要问题。技术壁垒:压铸模具的设计和制造技术门槛较高,需要企业不断投入研发力量,提升自主创新能力。环保要求:随着环保法规的日益严格,压铸模具的生产和使用过程中产生的废弃物处理、能耗降低等问题亟待解决。压铸模具的设计和生产需考虑材料的流动性和凝固特性。
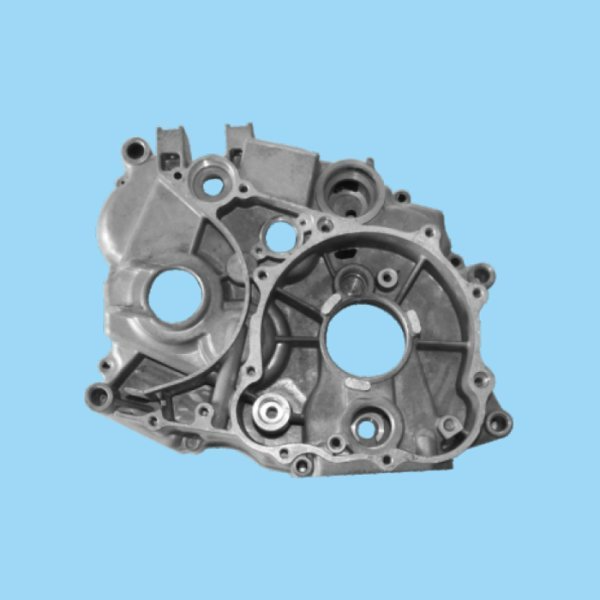
在压铸工艺的广阔舞台上,压铸模具的装配与调试无疑是整个生产流程中的关键环节。这一过程不仅要求高度的技术精度,还需要丰富的实践经验与对细节的追求。压铸模具作为连接设计理念与实体产品的桥梁,其装配与调试质量直接决定了较终产品的精度、性能和市场竞争力。随着制造业的快速发展和消费者需求的日益多样化,对压铸模具的装配与调试提出了更高的要求。因此,深入研究压铸模具的装配与调试技术,对于提升产品质量、降低生产成本、增强企业竞争力具有重要意义。合理的冷却系统设计对于压铸模具至关重要,它能有效控制铸件冷却速度,减少变形和裂纹。北京加工压铸模具公司
压铸模具的维护保养能够延长其使用寿命,降低生产成本。福建自动压铸模具厂家
后续维护与保养:模具的制造并不是一次性的过程,其后续的使用和维护同样重要。在使用过程中,要定期对模具进行检查和保养,及时发现并处理潜在问题。同时,还要对模具的使用情况进行记录和分析,以便为后续的模具制造提供参考和借鉴。压铸模具的制造流程是一个复杂而精细的过程,涉及到多个环节和技术。通过本文的介绍,相信读者对压铸模具的制造流程有了更加全方面和深入的了解。在实际应用中,应根据具体的产品要求和生产条件,制定合适的制造流程和工艺参数,以确保模具的质量和性能达到比较好状态。福建自动压铸模具厂家
上一篇: 上海销售压铸模具供应
下一篇: 河南铝合金压铸模具价格