压铸模具
关于定期检查模具:定期对模具进行全方面检查是确保其正常运行的重要措施。检查内容包括模具的精度、磨损情况、裂纹情况、润滑情况等。发现问题应及时处理,防止潜在故障的发生。同时,还应做好检查记录,以便对模具的使用情况进行跟踪和分析。模具的保养需要从多个方面入手,包括定期清洁、及时修复损伤、防止生锈、保持润滑、正确使用以及定期检查等。只有做好这些工作,才能确保模具的长期稳定运行,提高生产效率,降低生产成本。精确控制模具温度和压力是确保压铸产品质量稳定的关键。压铸模具
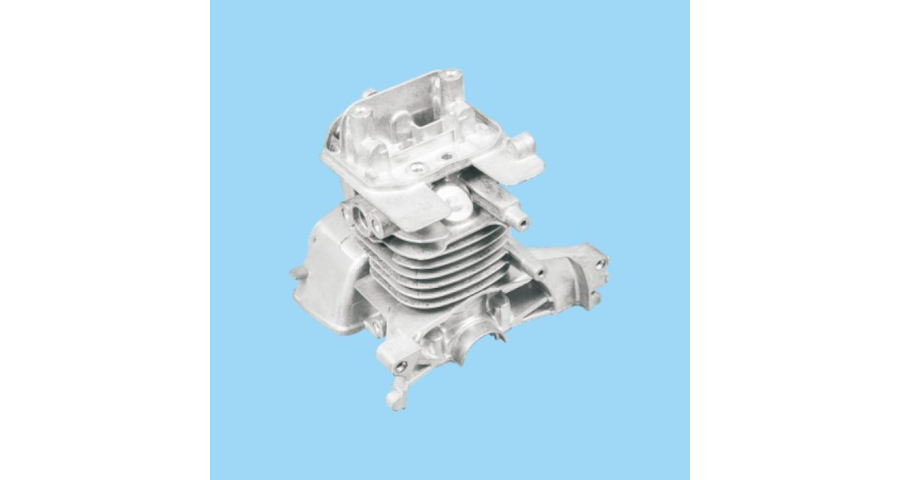
对于损坏的模具,应及时进行维修或更换。在维修过程中,应根据模具的损坏情况制定详细的维修方案,并选择合适的维修方法和材料。对于无法修复的模具,应及时进行更换,以免影响生产进度和产品质量。模具使用注意事项除了上述的维护措施外,在使用压铸模具时还应注意以下几点:严格按照操作规程使用模具,避免因操作不当导致的模具损坏。避免使用超过模具承受能力的压力和温度,以免对模具造成过大的应力和热应力。在使用模具前,应确保模具预热充分,以减少热应力和热裂纹的产生。在模具使用过程中,应密切关注模具的工作状态,如发现异常情况应及时停机检查和处理。广东自动压铸模具批发压铸模具的创新不仅体现在技术上,还包括生产过程的优化和管理方法的改进。
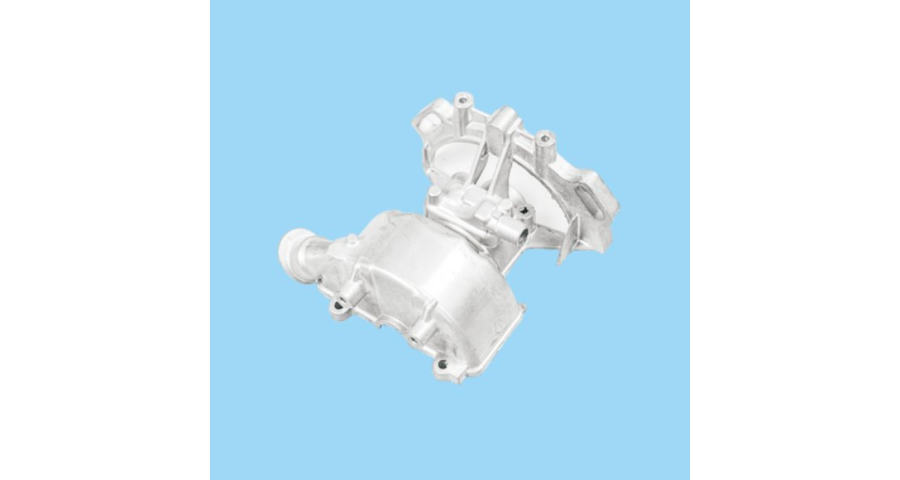
关于导向与定位机构:确保定模和动模在合模过程中的精确对位,防止错位和飞边。顶出机构:用于将凝固后的零件从模具中顶出,便于取件。压铸模具的设计要点在设计压铸模具时,需要考虑以下要点:模具材料的选择:应根据零件的材料、生产批量和模具寿命等因素,选择合适的模具材料。分型面的确定:分型面的选择直接影响到模具的结构和零件的脱模。浇道和排气系统的设计:合理的浇道设计可以确保金属流动顺畅,排气系统则有助于排除型腔内的气体,防止气泡产生。
在现代工业制造的广阔天地里,压铸模具作为一种高效、精密的成型工具,扮演着不可或缺的角色。它不仅是连接设计创意与实体产品的桥梁,更是推动制造业向智能化、高精度方向发展的重要力量。压铸模具,顾名思义,是用于压铸工艺中,通过高压将熔融的金属或非金属液体注入模具型腔,冷却凝固后形成所需形状和尺寸的零件或产品的工具。这一过程融合了压力、温度、时间三大要素的精确控制,要求模具具备极高的精度、强度、耐磨性和热稳定性。压铸模具通常由动模(也称公模)和定模(也称母模)两部分组成,通过合模、注料、保压、冷却、开模、顶出等步骤完成产品的生产。在模具设计阶段就考虑环保因素,可以减少生产过程中的能源消耗和废物排放。
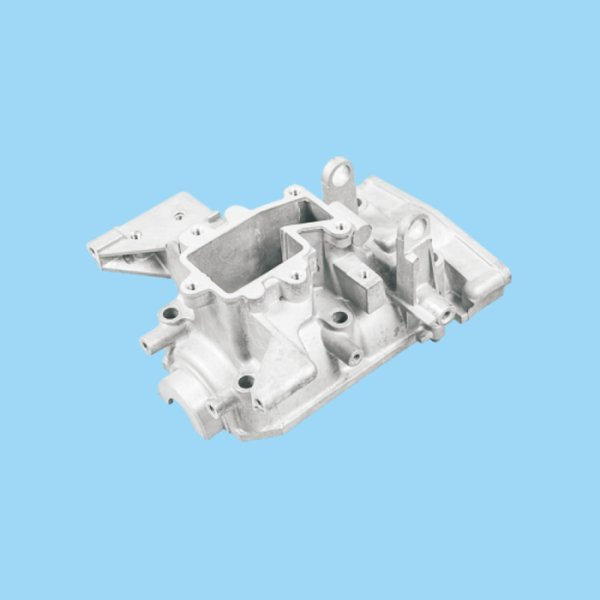
压铸模具的设计遵循“一模一腔”或“一模多腔”的原则,旨在以较少的模具成本生产出符合设计要求的高质量产品。设计过程中需考虑以下几个方面:分型面选择:分型面的合理布局直接影响模具的复杂程度、制造成本及产品质量。浇口设计:浇口的位置、形状和尺寸直接影响金属的流动性和填充效果,需根据产品形状、材料特性等因素综合确定。冷却系统设计:有效的冷却系统能够缩短生产周期,提高产品质量,减少模具热应力。顶出机构设计:合理的顶出机构设计能够确保产品顺利脱模,避免变形或损坏。压铸模具的寿命可以通过合理的设计和质优的材料选择来延长。河南汽车压铸模具多少钱
随着自动化技术的发展,压铸模具正朝着智能化、自动化方向迈进,提升整体生产效率。压铸模具
压铸模具广泛应用于汽车、电子、家电、通讯、航空航天、医疗器械等多个行业。在汽车行业中,压铸模具用于生产发动机缸体、变速箱壳体、车轮轮毂等关键零部件;在电子行业中,则用于制造手机外壳、电脑散热器、连接器等精密部件。随着新能源汽车、5G通信、智能制造等新兴领域的快速发展,压铸模具的应用范围将进一步扩大。技术创新智能化设计制造:借助人工智能、大数据等先进技术,实现压铸模具的智能化设计、制造和管理,提高生产效率和产品质量。新材料应用:开发高性能的模具材料,如高强度钢、高温合金、陶瓷基复合材料等,以满足更高精度、更长寿命的模具需求。精密加工技术:发展超精密加工技术,如纳米加工、激光加工等,进一步提高模具的加工精度和表面质量。压铸模具