梅州订单型生产管理系统哪家专业
生产管理软件在模具行业的优势有:1、提高生产效率:通过优化生产计划和工艺流程,减少生产过程中的浪费和延误,提高生产效率。2、降低生产成本:通过精细化管理和降低库存等方式,减少不必要的浪费和开支,降低生产成本。3、提高产品质量:通过对生产全过程的监控和控制,确保产品质量的稳定性和一致性,提高客户满意度。4、促进企业管理现代化:生产管理软件的应用推动企业管理的数字化转型,提高企业的竞争力和市场适应性。展望未来,生产管理软件将在模具行业中发挥更加重要的作用。随着技术的不断创新和市场的不断拓展,生产管理软件将进一步完善其功能和应用范围,更好地满足模具企业的需求。生产管理软件实现了模具生产过程的可视化管理,让管理者能够直观了解生产情况。梅州订单型生产管理系统哪家专业
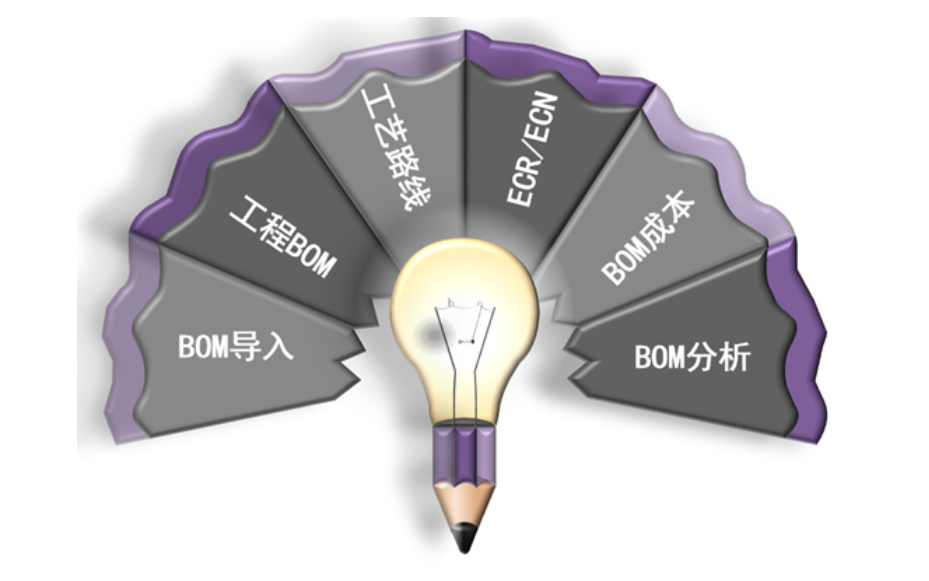
生产管理软件通过自动化的方式,将生产过程中的各个环节进行集成管理,实现生产过程的高效协调。它可以自动化地进行订单管理、物料采购、生产计划安排、生产进度跟踪等工作,有效减少了人工操作的时间和错误率。同时,生产管理软件还可以通过数据分析和预测,帮助企业合理安排生产资源,提高生产效率,实现更快速的交付。生产管理软件可以帮助企业实现生产过程的优化,减少资源的浪费和成本的增加。通过对生产过程的监控和分析,生产管理软件可以帮助企业发现生产过程中的瓶颈和问题,并提供相应的解决方案。此外,生产管理软件还可以帮助企业进行库存管理,避免库存积压和过剩,降低库存成本。通过降低成本,企业可以增强竞争力。潮州工厂车间生产管理系统生产管理软件支持模具生产的协同作业,提高了团队协作效率,减少了沟通成本。
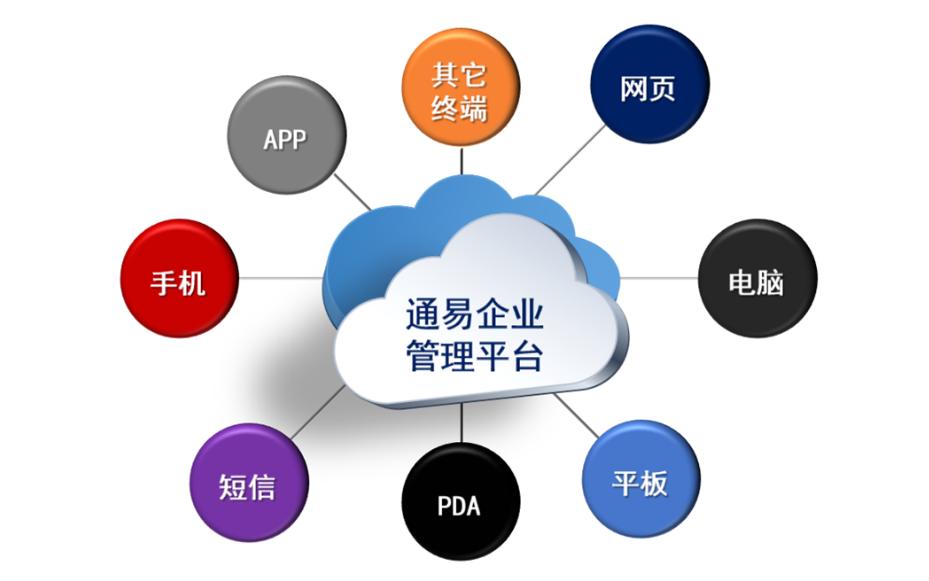
模具行业的库存管理一直是一个难题,过高的库存会增加企业的资金压力,而过低的库存则可能导致生产中断。生产管理软件可以通过对销售预测、生产计划和库存数据的分析,帮助企业实现库存管理的优化。软件可以自动计算库存水平,并提供及时的库存报警和补货建议,避免库存过高或过低的情况发生,提高资金利用效率。生产管理软件可以实现生产过程的可视化管理,通过数据采集和监控设备的连接,实时显示生产线上的各项指标和状态。这样,企业管理人员可以随时了解生产情况,及时发现问题并采取措施,提高生产线的稳定性和可靠性。
生产管理软件在物料管理方面发挥着重要作用,传统的物料管理多依赖于人工记录和盘点,容易出现错漏和延误。而生产管理软件可以实现物料的实时跟踪和精确控制,通过设置至低库存量和安全库存量,系统会自动提示采购需求和补货时间点,从而减少库存积压和缺料风险。当然,生产管理软件在五金行业的应用还远不止这些。例如,在设备管理方面,软件可以监控设备的运行状态和维护周期,预防故障发生,延长设备寿命;在人力资源管理方面,软件可以根据生产计划自动排班,合理调配人力资源,提高劳动生产率;在成本控制方面,软件可以实时收集成本数据,分析成本构成,帮助企业发现成本节约的潜在空间。通过生产管理软件,企业可以实时监控设备的运行状态,及时进行维护保养,延长设备使用寿命。
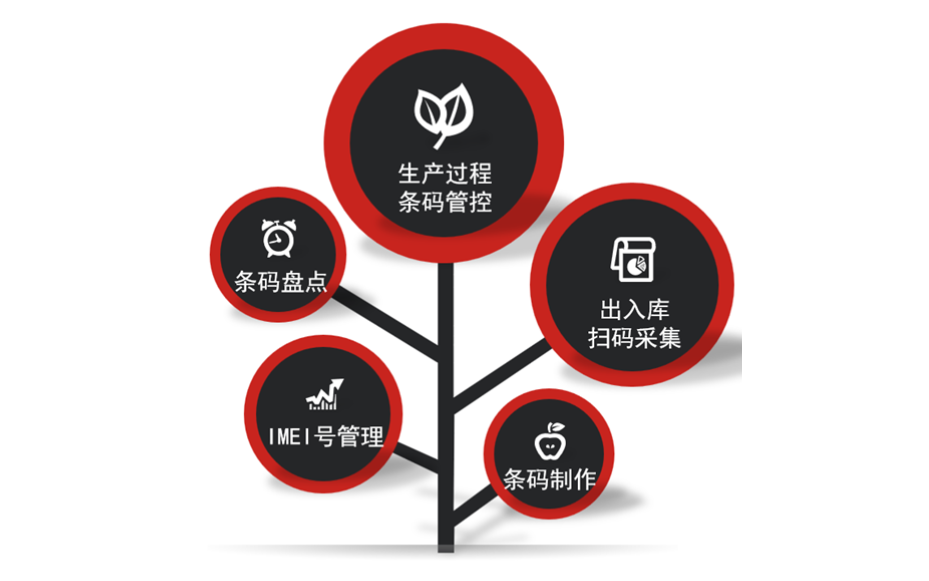
生产管理软件能够实现生产流程的标准化与自动化,传统的生产管理模式往往存在信息传递滞后、人工操作误差等问题,而生产管理软件则通过数字化手段对整个生产流程进行统一规划与实时监控,从而确保每一个生产环节都能够按照既定标准执行。无论是物料采购、库存控制,还是生产计划、工艺路线设定,都可以借助软件实现精确调度与智能管理,有效降低了人为错误的发生概率,提高了生产效率和产品质量。生产管理软件有助于提升资源利用效率,通过实时收集并分析生产数据,软件能够精确预测物料需求,有效减少库存积压和过度采购,从而降低成本,提高资金周转率。同时,通过对设备运行状态的实时监控,可及时进行预防性维护,延长设备使用寿命,降低故障停机时间,进一步提升生产效能。生产管理软件简化了五金企业的生产流程,降低了人工操作的错误率,提高了生产效率。光明服饰生产管理系统价格
生产管理软件优化了五金行业的库存管理,减少了库存积压,提高了资金周转率。梅州订单型生产管理系统哪家专业
在生产过程中,人为因素是导致错误的常见原因,生产管理软件通过标准化操作流程,减少人为干预,从而降低错误率。同时,软件还能实时监控生产质量数据,一旦发现问题即刻报警,便于及时纠正。如同精密仪器的生产,严格的质量控制是产品成功的关键,管理软件的应用有效保证了产品的一致性和可靠性。生产管理软件提供了从原材料到成品全过程的可视化管理,所有信息实时更新,为企业管理层提供了准确的数据支持。决策者可以依据这些数据做出更为科学合理的判断。例如,通过对生产数据的深入分析,某电子企业发现了产能瓶颈所在,及时调整策略,有效避免了潜在的损失。梅州订单型生产管理系统哪家专业
上一篇: 云浮企业生产管理系统哪家专业
下一篇: 龙岗服装erp生产管理系统多少钱