广州市花都区母婴产品液态硅胶模具图片
液态硅胶模具具有优异的透明度、抗撕裂强度、回弹性、抗黄变性、热稳定性、耐水、透气性好、耐热老化性和耐候性。同时,其粘度适中、便于操作,制品透明性高,可看到模具内灌铸材料是否有气泡等缺陷,线收缩率≤0.1%,复制制品尺寸精密。
广州佳泽硅胶科技有限公司是集设计研发、生产制造为一体的一站式”硅胶+”专业服务商,国家高新技术企业。现在,佳泽的产品已销往全球35个国家及地区,获得全球3000多名客户的认可,产品遍及消费电子、医疗美容、工业机械、汽车制造等领域。 模腔的精度直接影响到制品的尺寸精度和外观质量,因此在加工模腔时需要采用高精度的加工设备和工艺。广州市花都区母婴产品液态硅胶模具图片
液态硅胶模具
可精细成型:复制复杂结构:液态硅胶在成型前流动性好,能够适应不同形状和尺寸的模具,并且在固化成型后体积变化极小。因此,液态硅胶模具可以精确地复制出各种复杂的结构和形状,满足婴儿喂养用品多样化的设计需求,如制作出具有特殊形状的奶嘴、带有防胀气装置的奶瓶等。细节表现出色:能够很好地呈现出产品的细节,使喂养用品的外观更加精致,提高产品的质量和美观度。例如,可以清晰地制作出奶嘴的出奶孔、奶瓶的刻度等细节部分,方便家长使用。广东奶瓶奶嘴液态硅胶模具厂由于液态硅胶模具的设计复杂且成本高,因此更换模具需要较高的成本和时间。
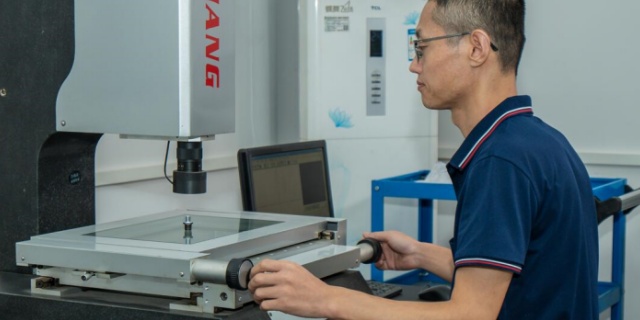
液态硅胶模具的价格区间较大,从几元到几十万元不等。具体价格取决于模具的具体要求和用途。模具规格和尺寸:模具的规格和尺寸越大,所需的材料越多,制造成本也越高,因此价格也会相应上升。模具复杂度:模具的复杂度包括结构的复杂性和精度的要求。结构越复杂、精度要求越高的模具,制造难度越大,价格也就越高。定制程度:如果客户需要定制特定形状、尺寸或功能的模具,厂家需要根据客户需求进行设计和制造,这会增加制造成本和时间,因此价格也会相应提高。生产厂家:不同厂家的生产工艺、技术水平、原材料采购渠道等都会影响模具的价格。一些品牌或经验丰富厂家生产的模具价格通常较高,但质量和售后服务也更有保障。
除了之前提到的婴儿日常用品、餐具与饮具、玩具与护理用品等用途外,婴儿液态硅胶模具还有以下一些用途:一、婴儿辅食制作工具辅食模具:液态硅胶辅食模具可用于制作婴儿辅食,如水果泥、蔬菜泥等。这些模具形状多样,可以制作出有趣的辅食形状,增加婴儿对食物的兴趣和接受度。
二、婴儿生活用品浴室用品:液态硅胶因其防滑和耐用的特性,可以被用来制作婴儿浴室用品,如防滑垫、洗澡玩具等。这些产品有助于提升婴儿在浴室中的安全性和舒适度。其他生活用品:液态硅胶模具还可以用于制作婴儿的生活用品,如挂饰、手环等,这些产品不仅具有装饰作用,还可以作为婴儿的身份标识或安全提示。 液态硅胶模具应用于医用零部件,如导管、注射器活塞、硅胶密封圈等。这些制品对模具的精度和卫生要求高。
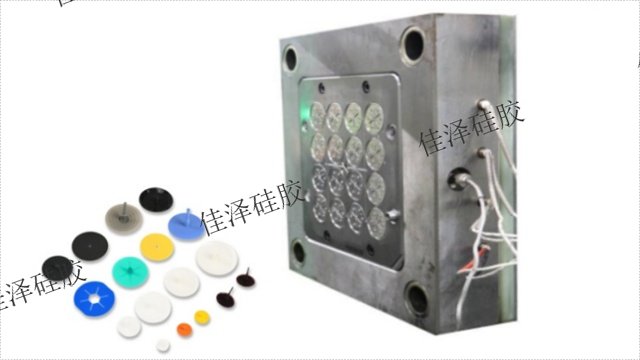
液态硅胶模具常见价格范围简单模具:对于一些结构简单、尺寸较小的液态硅胶模具,价格通常较低,可能低至几千元甚至更低(如一些小型烘焙模具或DIY模具)。中等复杂度模具:中等复杂度的液态硅胶模具,如一些用于食品包装或医用品的模具,价格可能在几万之间。高精度复杂模具:对于高精度、结构复杂的液态硅胶模具,如用于汽车零部件、电子产品外壳等的模具,价格可能高达5万甚至更高。
广州佳泽硅胶科技有限公司是一家对环境负责的有机硅公司,致力于生产定制的液态硅胶模具与液态硅胶制品。 广州佳泽硅胶科技有限公司目前为多个行业提供硅胶及塑胶成型技术解决方案。广州市子宫扩张球囊液态硅胶模具供应商
生产汽车零部件,如发动机密封件等。液态硅胶模具能够生产出具有复杂形状和高精度汽车零部件。广州市花都区母婴产品液态硅胶模具图片
在医疗领域,液态硅胶模具被广泛应用于医疗器械和生物材料的制造。例如,人工关节、血管、气管等医疗器械,以及药品包装材料、人造皮肤、骨骼等生物材料。液态硅胶模具的高精度和生物相容性使其成为这些产品的理想选择。
广州佳泽科技公司产品涉及领域:通讯、手机、3C防水配件类液态硅胶制品,汽车电子配件类液态硅胶制品,母婴液态硅胶用品,液态硅胶密封制品,液态硅胶厨具类制品,工业密封硅胶制品、塑胶制品、双色塑胶制品等。 广州市花都区母婴产品液态硅胶模具图片
广州佳泽硅胶科技有限公司的高能力包括所有方面的设计和生产过程。我们可以帮助您为您的部件选择合适的LSR,提供优化制造性(DFM)和部件性能的部件设计支持,提供质量的模具,以及大量的部件生产和包装解决方案,以保持您更低的成本。 我们与全世界原材料供应商合作,通过设计和优化定制的硅胶零件和制造工艺来满足每个程序的指定需求,从而为我们的合作伙伴提供更大的价值。欢迎各位朋友来厂参观交流学习液态硅胶注塑成型工艺的应用。
上一篇: 广州市月经杯液态硅胶产品制造厂
下一篇: 广州鸭嘴阀液态硅胶制品成本