盐城级进连续模具修模
定位块的使用方法在具体的模具加工作业中,使用定位块的具体方法有以下几点需要注意:1.选择合适的定位块种类:根据具体的加工需求和模具结构特点,选择合适的定位块种类和材料。2.定位块的安装位置:根据零件的尺寸、形状和结构特点,设计合理的定位块安装位置及固定方式,保证零件加工过程中的稳定性和精度。3.定位块的使用规范:在使用过程中,遵循使用规范,确保定位块的使用寿命和精度稳定。总之,模具里面定位块是模具加工过程中非常重要的部件,具有准确定位、提高加工效率、保证零件精度等多重优点。在实际的加工作业中,合理选择定位块种类和使用规范,可以很大提高模具的加工效率和精度。使用五轴加工中心可对普通的三坐标机床难以加工的复杂零件进行加工,加工的质量好,效率也高。盐城级进连续模具修模
模具
模具冲压时下料偏位尺寸变异有哪些原因,应采取什么对策?下料偏位尺寸变异的主要原因及相应的对策有:1)凸凹模刀口磨损,产生毛边(外形偏大,内孔偏小)需研修刀口;2)设计间隙不当,修改设计并控制加工精度;3)下料位凸模及凹模镶块等偏位,间隙不均,可以调整其位置精度和冲裁间隙;4)导正销磨损,销径不足,可以更换导正销;5)导向件磨损,可以更换导柱导套;6)送料机送距压料放松调整不当,重新调整送料机;7)模具闭模高度调整不当,重新调整闭模高度;8)脱料镶块压料位磨损,无压料(强压)功能或由材料牵引翻料引发冲孔小)可以研磨或更换脱料镶块,增加强压功能,调整压料;9)脱料镶块强压太深,冲孔偏大,需调模减小强压深度;10)冲压材料机械性能变异(强度延伸率不稳定)需更换材料,控制进料质量;11)冲切力对材料牵引造成尺寸变异,可以在凸模刃部端面修出斜度或弧形以改善冲切时受力状况或者在下料部位于脱料镶块上加设导位功能.连云港拉伸连续模具开发数控机床能有效地节省机动时间,快速移动缩短空行程的时间,进给量的范围较大。
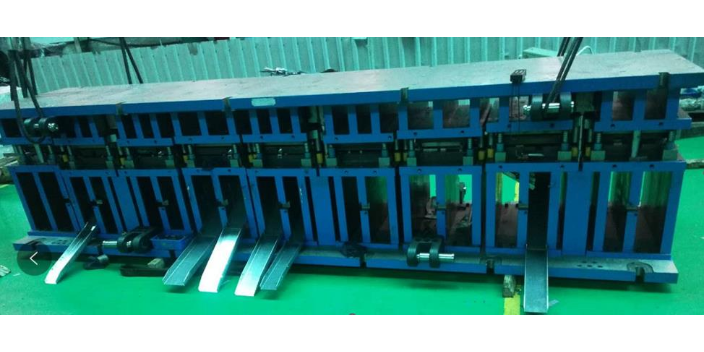
模具冲压时卡料的原因是什么,应采取什么对策?冲压时卡料的主要原因及相应的对策有:1)送料机送距压料放松调整不当,需重新调整;2)生产中送距产生变异,需调整送料机送距;3)送料机故障,需调整及维修;4)材料弧形,宽度超差,毛边较大时,要更换材料,控制进料质量;5)模具冲压异常,造成镰刀弯,消除料带镰刀弯;6)导料孔径不足,上模拉料,研修导正孔;7)折弯或撕切位上下脱料不顺,调整脱料弹簧力量等;8)导料板之脱料功能设置不当,修改导料板,防料带上带;9)材料薄,送进中发生翘曲,送料机与模具间需加设上下压料,加设上下挤料安全开关;10)模具架设不当,与送料机垂直度偏差较大,需重新架设模具
无心磨床的工作原理是:通过砂轮高速旋转进行磨削,同时导轮以较慢速度同向旋转,从而带动工件旋转,作圆周进给。贯穿磨削时通过调整导轮轴线的倾斜角来实现轴向进给,切入磨削时通过导轮架或砂轮架的移动来实现径向进给。无心磨削时,工件的中心必须高于磨削轮和导轮的中心连线,这样便有使工件与磨削砂轮和导轮间的接触点不可能对称,于是工件上某些凸起的表面在多次转动中能逐渐磨圆。如果托扳的顶面是水平的,而且调整得件中心与磨削砂轮和导轮的中心处于同一高度,当工件上有一凸起的点与导轮接触时,则凸起点的对面就被磨成一凹坑,其深试行过意不去凸起点的高度。工件回转180度后,凸起的点与磨削砂轮接触,此时凹坑正好与导轮相接角,凸起的点无法被磨平,此时工件外圆表面为一个等直径的棱圆。模具的设计和制造过程中,通常会确保其在使用过程中的可重复性。
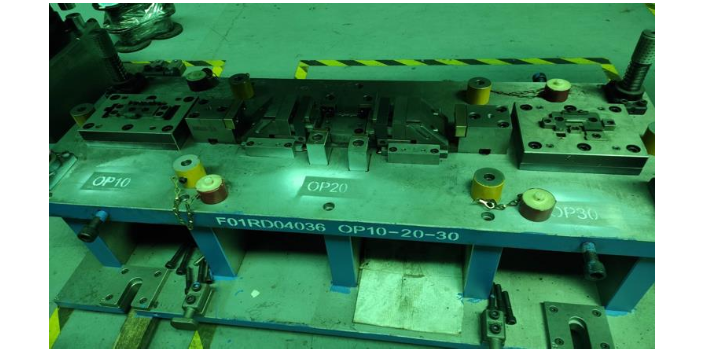
车床夹具的作用:1)保证加工精度用机床夹具装夹工件,能准确确定工件与刀具、机床之间的相对位置关系,可以保证加工精度。(2)提高生产效率机床夹具能快速地将工件定位和夹紧,可以减少辅助时间,提高生产效率。(3)减轻劳动强度机床夹具采用机械、气动、液动夹紧装置,可以减轻工人的劳动强度。(4)扩大机床的工艺范围利用机床夹具,能扩大机床的加工范围,例如,在车床或钻床上使用镗模可以代替镗床镗孔,使车床、钻床具有镗床的功能。数控机床能适应不同品种、规格和尺寸的工件加工。扬州弹片冲压模具图
数控加工时采用小直径刀具、小切深、小切宽、快速多次走刀来提高切削效率。盐城级进连续模具修模
生产中造成模具修理的原因有很多,主要有以下几个方面:(1)冲模零件的自然磨损,包括定位和导向零件的磨损,模柄松动,凸模在固定板上松动,凸凹模间隙变大刃口变钝.(2)制造工艺不当,主要是冲模材质不好,淬火硬度不够,凸凹模倒锥,导向零件精度和刚性不足及凸凹模安装后中心轴线偏心等.(3)冲压操作不当:冲模底面与压力机工作台面不平行,压力机工作中心与冲模工作中心不重合,凸模进入凹模刃口太深,压力机操作中故障和冲压工粗心不按规程操作导致模具损坏.盐城级进连续模具修模
上一篇: 宁波冲压模具加工
下一篇: 扬州冷轧钢冲压模开发