西宁半导体缺陷检测设备
薄膜缺陷检测设备的工作原理主要是通过光学成像技术,将薄膜表面的图像清晰地投射到显示器上,然后通过图像处理技术对图像进行分析,从而检测出薄膜中的缺陷。这种设备的检测范围非常普遍,可以检测出的缺陷种类多,包括气泡、划痕、裂纹、褶皱、颜色不均等等。而且,由于这种设备的准确率非常高,因此可以有效减少人为因素的干扰,提高产品的质量和性能。薄膜缺陷检测设备的优点不仅在于其检测能力强大,还在于其操作简便,易于维护。这种设备通常采用计算机控制系统,操作人员只需要输入相关的参数,就可以开始检测工作。而且,这种设备的维护也非常方便,一旦设备出现故障,可以通过远程诊断系统进行维修,有效提高了设备的使用效率。标签缺陷检测设备具有多相机同步拍摄功能,可以快速地对大批量标签进行检测,提高了检测效率。西宁半导体缺陷检测设备
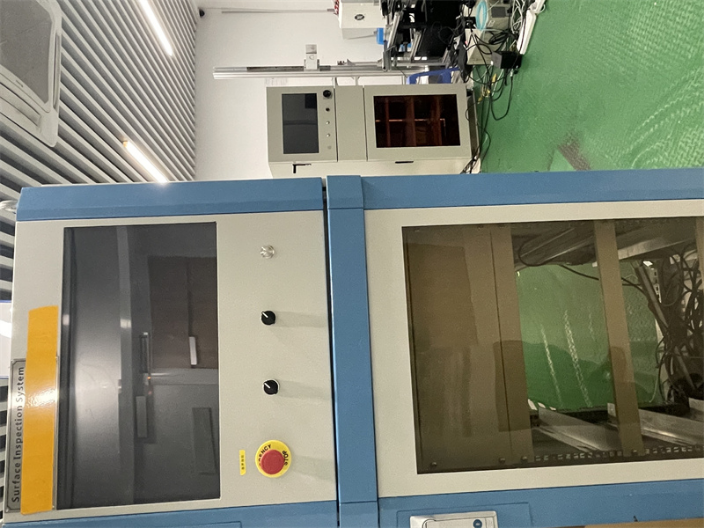
为企业形象加分:之所以现在很多企业都愿意使用这种设备进行外观检测,首要原因便是比人工检测精度更高,功率更快。在作业中,不需要浪费太多成本检测产品,避免出现不良品的问题,让一切产品都能符合出厂标准进行销售,给企业形象加分。作业流程变得简略省心:因为使用专业品牌外观检测设备进行作业,整个作业流程完全不需要人工参与,这样就能很大程度的降低作业成本,不用忧虑人作业业进程出现失误问题。提高检测精度和功率,促进产品出产质量。自动外观检测设备设计解决方案,检测精度高,米级检测速度快,精度高,提高产质量量。天津光刻胶缺陷检测设备通过使用半导体缺陷检测设备,制造商可以降低生产成本并提高生产效率。
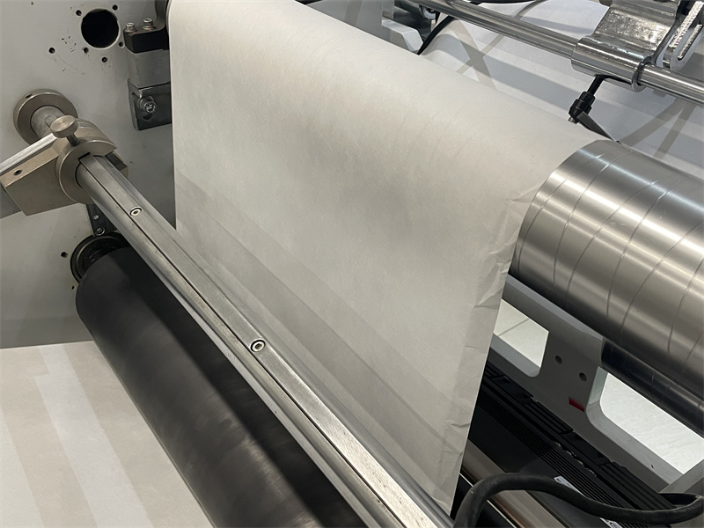
半导体芯片缺陷检测设备具有高度的自动化程度,可以自动完成检测任务,无需人工干预。这种设备可以根据不同的芯片类型和生产线的要求进行定制,以满足不同的检测需求。它可以与生产线的其他设备进行集成,实现自动化生产。这种设备还可以通过远程控制和监控,实现远程管理和维护,有效提高了生产效率和设备的利用率。半导体芯片缺陷检测设备的使用可以有效地提高生产效率,减少人工成本。传统的缺陷检测方式需要人工进行检测,不仅效率低下,而且容易出现漏检和误检的情况。而采用半导体芯片缺陷检测设备可以实现自动化检测,有效提高了检测效率和准确性。同时,这种设备还可以减少人工成本,因为它可以替代人工进行检测,从而降低了生产成本。
在薄膜行业,复合膜生产过程中,会出现各类的表面缺陷,空气中的尘埃,以及空气在高压复合的工艺段会进入复合膜内部,从而使膜材质量下降,这种缺陷都是微米级的,人眼很难观测到,且长时间看也会使眼睛疲劳,这个时候就需要视觉检测设备进行全检,提高产品质量,反馈到工艺端。从检测,到反馈,到调整生产工艺,这是一个闭环的流程。这就是工业中缺陷检测的一些应用和作用。目前机器视觉缺陷检测已在橡胶、电子、五金、汽车、包装、印刷、化工、手机、食品、塑胶、纺织、紧固件等行业得到了普遍的应用。板材表面缺陷检测设备的维护简单,定期清理和维护设备可以延长其使用寿命。
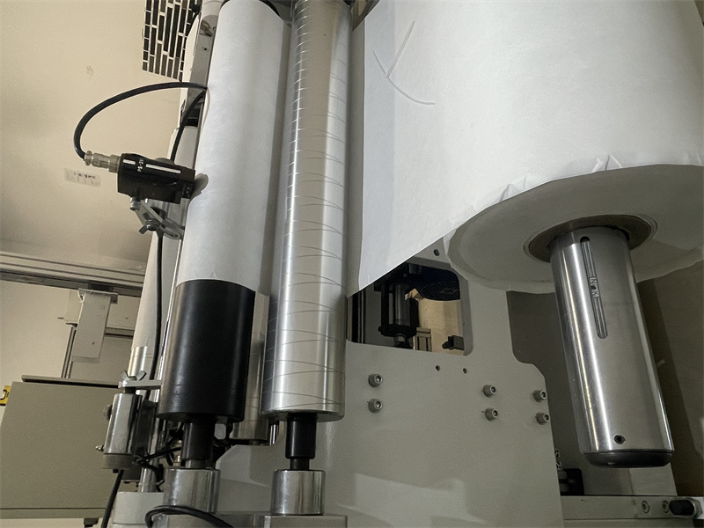
Optima晶圆缺陷检测设备的关键组件有哪些?1.光源:Optima晶圆缺陷检测设备的光源是其中心组件之一,负责提供稳定的光照射到晶圆表面。光源的选择和配置直接影响到检测结果的准确性和稳定性。2.光学系统:光学系统是Optima晶圆缺陷检测设备的另一个关键组件,负责将光源发出的光线聚焦到晶圆表面。光学系统的设计和制造需要考虑到晶圆的特性和检测要求,以确保光线能够均匀地照射到晶圆表面。3.图像采集系统:图像采集系统负责捕捉晶圆表面的图像数据,为后续的数据分析和处理提供原始数据。图像采集系统的分辨率、采样率和噪声控制等参数对检测结果的准确性有重要影响。4.计算机处理系统:计算机处理系统是Optima晶圆缺陷检测设备的控制中心,负责对采集到的图像数据进行处理和分析。计算机处理系统的算法和软件需要具备高度的稳定性和可靠性,以确保检测结果的准确性。X-ray缺陷检测设备利用高能X射线技术,可以快速准确地检测出制造过程中的缺陷。晶圆外观缺陷检测设备生产公司
薄膜缺陷检测设备具有高精度、高稳定性、高可靠性等优点。西宁半导体缺陷检测设备
Optima晶圆缺陷检测是一种先进的自动化检测系统,可以高效地识别和分类晶圆表面的各种缺陷,从而提高生产效率。该系统采用了新的图像处理和机器学习技术,能够准确地检测出晶圆表面的微小缺陷,如裂纹、污点等,并将其分类,以便于后续的处理和分析。Optima晶圆缺陷检测系统的中心技术是图像处理和机器学习。该系统采用高分辨率的摄像头和光源,可以捕捉到晶圆表面的高清晰度图像。然后,通过图像处理技术,将图像中的缺陷区域进行标记和分割,以便于进一步的分析和处理。接下来,系统会使用机器学习算法,对这些缺陷进行分类,以便于后续的处理和分析。西宁半导体缺陷检测设备
上一篇: 半导体缺陷检测设备求购
下一篇: 重庆半导体缺陷检测设备