南通智能微量润滑售价
微量润滑系统技术的好处:1、使用的微量润滑油绿色环保可降解,并且量少,切削油的用量很大地降低。2、配合MQL装置准确雾化喷射,无油雾弥散到空气中,同时很大地降低刀具/工件之间产生的摩擦热。3、无废油处理,传统的切削液废液需要交由专门的环保部门处理,而微量润滑油在加工过程中就被消耗掉了,无废油产生。4、更洁净,安全的工作环境,避免传统浇注式供给切削液飞溅接触到操作者皮肤,引起过敏。5、降低成本,浇注式切削需要建立一个复杂且昂贵的切削液循环系统,这无形中也增加了制造成本。微量润滑装置具有高效率和低成本投入的优势。南通智能微量润滑售价

微量润滑光滑在加工中心运用的优势:一、与加工中心的高速切削相适应。加工中心为高速、高效加工设备,不论是工作速度还是反应速度都十分方便,因而配套的微量光滑体系也需求具有快速的反应时间。多普赛微量光滑体系可做到开机即有。二、微量润滑降低成本。微量光滑中光滑剂的耗量大约为湿切光滑剂耗量的万分之一,微量润滑降低了光滑剂的成本。一起微量光滑是以压缩空气为动力,与切削液循环体系比较能源消耗也很大地降低。另一方面,微量光滑替代切削液体系后,可直接降低机床本身制造成本。三、微量润滑改善环境。运用微量光滑不会出现运用切削液时乳化液飞溅的状况,对工作环境和机床本身的清洁都可起到保护作用。四、全体功率的提高。微量光滑加工为准干式加工,可省去湿切加工时的工件清洗工序,缩短工艺链,提高生产线的全体功率。徐州机床微量润滑哪里有微量润滑油降低成本:切削油微量使用,有效降低购买和库存成本。
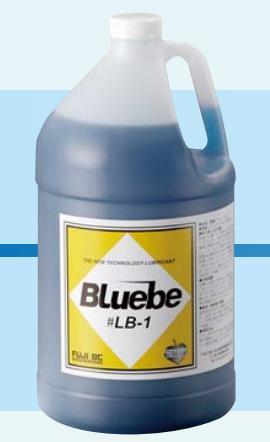
微量润滑是一种环保绿色的加工方式,为什么说是环保的加工方式呢?微量润滑使用的微量润滑油是采用可降解的植物性原料及多种环保添加剂精制而成的,不含矿物油、磷、硫、氯,因而更环保。微量润滑油除了有环保成分的优势外,还具备以下优异性能:1、化学结构稳定,存储的稳定性、热稳定性以及优良的摩擦和吸附性;2、使用量少,节约资源,实现准确润滑;3、具有适当的粘度,很好的渗透性,起到良好的润滑作用的同时减小切削阻力,得到要求的表面粗糙度,提高加工精度;4、导热性好,起到良好冷却作用,能降低切削温度,延长切削工具的使用寿命;5、防锈性好,不对金属腐蚀,不会因腐蚀而损坏机床和工件的精度及表面粗糙度。
微量润滑油在使用上有哪些优势:一、使用微量润滑油有效降低成本。1、专门切削油微量使用,有效降低购买和库存成本;2、省去传统切削液的日常管理和废液处理;3、切削液供应装置简易化,无需循环过滤系统;4、生产效率提高,有效降低生产费用;5、清洁干燥的切屑,可免清洗而直接回炉熔炼省去许多后处理工序;6、工件上几乎无油,甚至可免除后序清洗工序。二、使用微量润滑油提高生产效率/表面质量本申微量润滑具寿命。1、提高切削速度和进刀量;2、减少刀具工件与刀具切屑之间的摩擦;3、提高加工精度和降低表面粗糙度;4、基本保持室温除刀具和工件尺寸变化;5、可以让刀具寿命延长1-2倍。微量润滑可以减少机械设备的磨损,降低维修和更换成本。
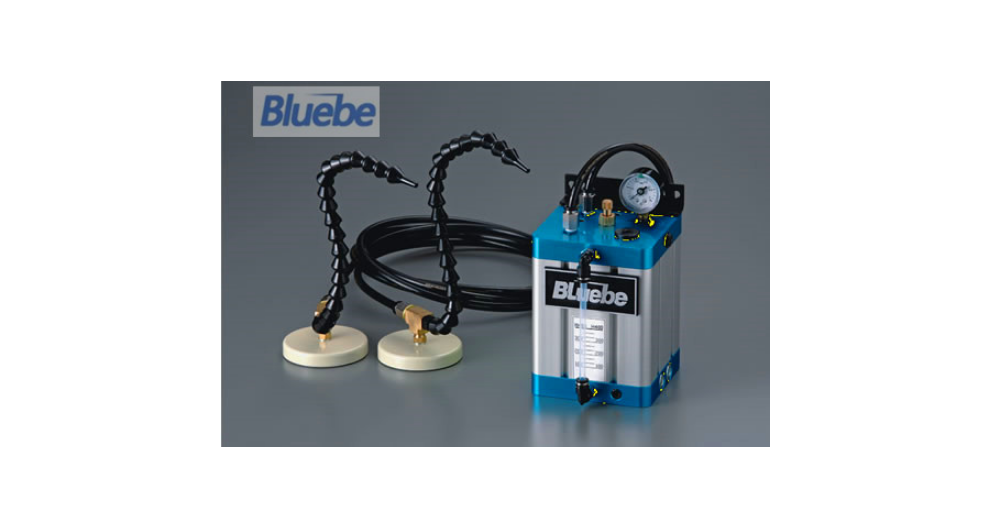
微量润滑技术的发展前景非常广阔。随着人们对机械加工精度和出产效率的要求越来越高,微量润滑被认为是一种非常有效的解决方案。目前,有许多研究正在进行,以提高微量润滑技术的性能和应用范围。例如,研究人员正在努力寻找新型润滑材料,开发更加高效的微量润滑系统,以及探索在不同工况下的微量润滑机理等。除了在机械工程中的应用,微量润滑技术也具有很大的潜力在环境保护方面发挥作用。与传统润滑技术相比,微量润滑技术使用的润滑剂量更少,减少了对环境的污染。此外,微量润滑技术还可以降低机器设备的能耗,减少能源的浪费。微量润滑是一种环保绿色的加工方式。南京微量润滑生产公司
微量润滑油化学结构稳定,存储的稳定性、热稳定性以及优良的摩擦和吸附性。南通智能微量润滑售价
在国内市场上,微量润滑技术也已普遍应用于汽车零部件生产制造过程中,如:曲轴、连杆、箱体箱盖的加工。微量润滑其独特的优势是因为采用了先进的雾化技术,得到了微米级的雾化颗粒,这些颗粒通过主轴及钻头、铣削工具、丝锥等具有内冷通道的设备输送到切削点。油品消耗以ml/h(每小时毫升)为单位,大幅度的降低加工成本及维护成本。与传统加工润滑方式对比具有明显的优势,主要是因为油雾可以是微米级的,有很好的渗透性,使得切屑与加工工具之间具有良好的润滑。微量润滑的优势如下:(1)油雾能渗透到摩擦点位置,起到良好的润滑效果;(2)在深孔加工中,压缩空气流速能带走切削热,而大量的切削热被切屑带走。(3)油耗量低,切削摩擦点始终有适量可靠的润滑油进行润滑;(4)产品体积小,气源消耗低,操作简单;(5)降低机床的运行维护成本和机床制造成本;由于切削液对环境带来的影响日益突显,对节能环保的要求日渐高涨高,选择合适的润滑方式尤其重要,微量润滑可以帮助企业降低运行成本。南通智能微量润滑售价
上一篇: 常州进口微量润滑油
下一篇: 上海进口准干式切削系统哪家强