揭阳自动热熔胶棒生产线
想要热熔胶棒生产线寿命长一些,制定一份完善的热熔胶棒生产线维护保养计划至关重要。首先,每日开机前的检查是基础。需要查看设备的外观是否有损坏、变形或松动的部件。同时,清洁设备表面的灰尘和杂物,确保工作环境整洁。检查各输送带的张紧度,如有松动及时调整。还要检查电气控制系统,查看按钮、指示灯是否正常,线路是否有破损或接触不良的情况。每日的这些简单检查能够及时发现潜在问题,避免小问题演变成大故障,保障生产线的正常启动和运行。热熔胶棒生产线具备高效的生产能力,能够快速响应市场需求,满足大规模生产的需要,为客户创造价值。揭阳自动热熔胶棒生产线
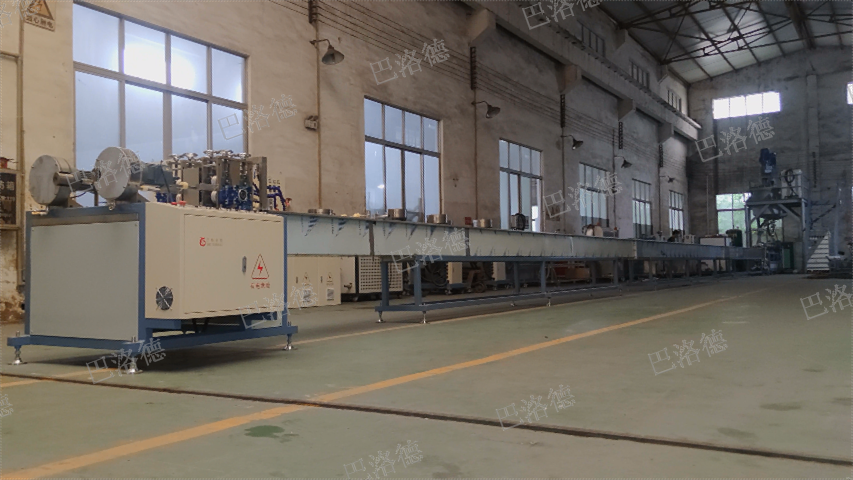
另一个关键的技术参数是挤出压力。合适的挤出压力能够保证胶料均匀、连续地从模具挤出,形成外形规整的胶棒。挤出压力通常通过螺杆的转速、螺距以及料筒的结构来调节和控制。一些高级的生产线可以实现挤出压力的自动调节和监控,根据胶料的特性和生产要求实时优化压力参数。例如,在生产直径较小的热熔胶棒时,需要较高且稳定的挤出压力,以确保胶棒的尺寸精度和表面质量。模具的精度也是不容忽视的技术参数。模具的孔径、孔型以及表面光洁度直接决定了热熔胶棒的尺寸和形状精度。高精度的模具可以使胶棒的直径误差控制在极小的范围内,例如正负0.1毫米甚至更小。而且,优良的模具能够保证胶棒表面光滑,无毛刺、气泡等缺陷,提高产品的外观质量和使用性能。模具的材质通常选用耐磨、耐高温的合金钢,以保证其在长期生产过程中的稳定性和耐用性。揭阳微型热熔胶棒生产线热熔胶棒生产设备的先进设计使得热熔胶棒的生产效率和质量同步提升。
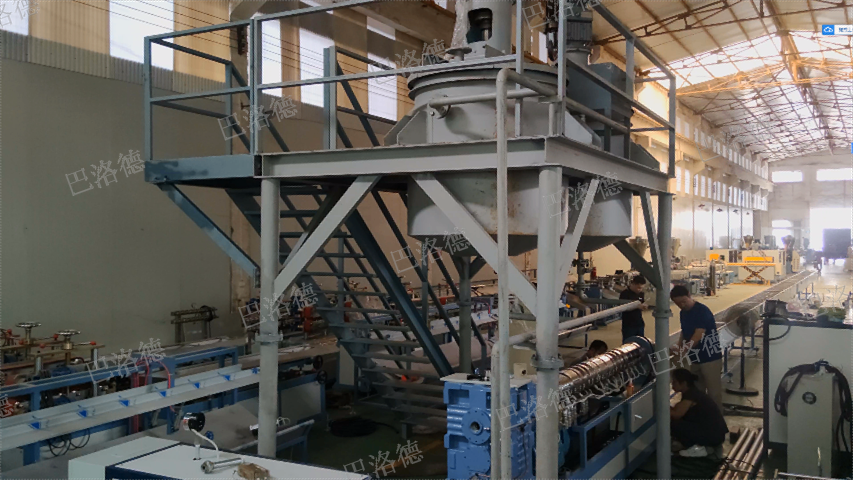
热熔胶棒生产线的内核环节热熔胶棒生产线是一个高度自动化、精密控制的制造过程。其内核环节在于挤出机的运作,该设备通过精密的螺杆设计,实现了热熔胶原料的塑化、混炼与挤出。挤出过程中,温度与压力的精确控制至关重要,它们直接影响到胶棒的成型质量与性能。整个生产线采用全自动控温与变频调速技术,确保生产过程的稳定与高效。原料准备与预处理在热熔胶棒生产线启动前,原料的准备与预处理是不可或缺的一步。原料需确保干净、无杂物,特别是严防金属等坚硬物质的混入,以免损伤设备或影响产品质量。
原料经过严格的筛选与清洗后,进入冷混阶段,为后续的挤出成型做好充分准备。这一环节虽看似简单,却是保证产品质量的基础。挤出成型与冷却牵引热熔胶原料在挤出机中经过高温塑化后,被连续挤出成条状。此时,胶条温度极高且处于熔融状态,需立即进入冷却牵引阶段。牵引机与挤出机同步工作,确保胶条在冷却过程中保持均匀的速度与张力,从而得到粗细一致、表面光滑的胶棒。冷却水循环系统则不断为牵引机提供清洁的冷却水,确保胶棒快速降温固化。经过冷却固化后的热熔胶棒,会被自动切割成预设长度的产品,便于后续包装和运输。
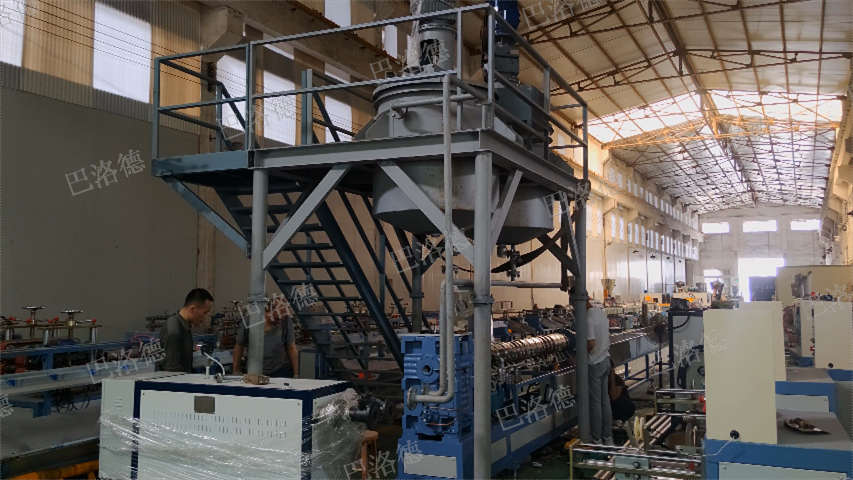
热熔胶棒生产设备具有出色的节能降耗特点。其优化的加热系统和高效的动力传动装置,能够有效地降低能源消耗。例如,采用先进的电磁加热技术或节能型的电阻加热元件,相比传统的加热方式,能够显著提高能源利用效率,减少不必要的能源浪费。同时,设备的合理设计和优化的运行模式,能够降低机械磨损和动力损耗,延长设备的使用寿命,降低维护成本。以某大型生产厂家为例,通过采用节能型的热熔胶棒生产设备,每年能够节省大量的电费和维修费用,提高了企业的经济效益和市场竞争力。热熔胶棒生产线的设计充分考虑了维护的便捷性,设备部件易于拆卸和更换,降低了维护成本。河池热熔胶棒生产线厂家电话
热熔胶棒生产线效率高,企业好帮手。揭阳自动热熔胶棒生产线
热熔胶棒生产线的高效运作离不开严格的质量控制体系。在生产过程中,从原材料的采购到成品的出厂,每一个环节都要经过严格的检测。对于原材料,要确保其质量符合标准,没有杂质和变质现象。在生产过程中,定期对设备进行维护和校准,以保证生产的准确性和稳定性。同时,对生产出的热熔胶棒进行抽样检测,包括外观检查、尺寸测量、粘结性能测试等。只有通过了所有检测的产品,才能进入市场销售。这种严格的质量控制,使得热熔胶棒生产线能够生产出高质量、可靠的产品,满足客户的需求。揭阳自动热熔胶棒生产线
上一篇: 广西微型撕裂膜抽纱开网生产线
下一篇: 苏州铁氟龙管材生产线推荐厂家