锂电池生产线组装线批发
为了响应可持续发展战略,我们的锂电池生产线融入了绿色能源循环利用系统。该系统利用太阳能光伏板为生产线提供部分电力,减少了对传统能源的依赖。同时,在生产过程中产生的废热、废水等副产品,通过先进的能源回收技术转化为可再利用的热能或清洁水,实现了资源的较大化利用。此外,对于废旧锂电池的回收处理,我们建立了完善的回收体系,通过专业设备提取有价值的金属元素,用于新电池的生产,形成了闭环的绿色产业链。创新科技锂电池生产线搭载了先进的数字化质量控制平台,该平台集成了质量追溯、数据分析与持续改进三大功能模块。高效烘干设备确保锂电池极片干燥质量。锂电池生产线组装线批发
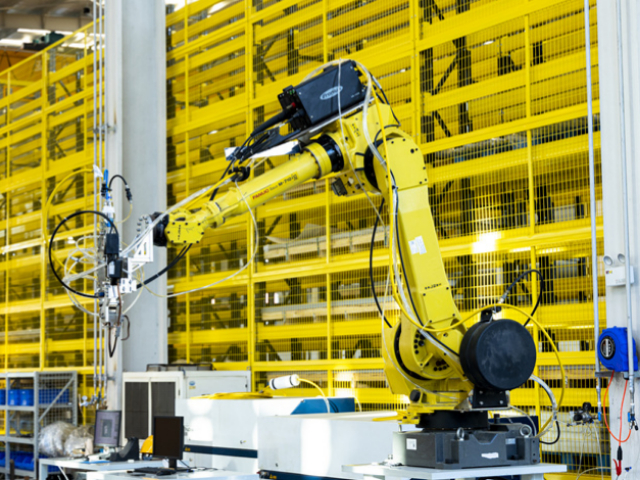
高效锂电池生产线的工作原理涉及多个复杂而精细的步骤,每个步骤都直接关系到电池的性能和质量:电芯组装与注液,电芯的组装是将正极片、负极片和隔离膜以卷绕或叠片的方式组合在一起,形成裸电芯。组装完成后,需向电芯内注入适量的电解液。电解液是电芯内部能量交换的媒介,其注入量直接影响电池的性能和安全性。过多或过少的电解液都会导致电池性能下降甚至失效。因此,注液过程需严格控制注入量,确保每个电芯都能获得比较好的电解液配比。18650锂电池生产线生产商家锂电池生产线采用自动化设备提高生产效率。
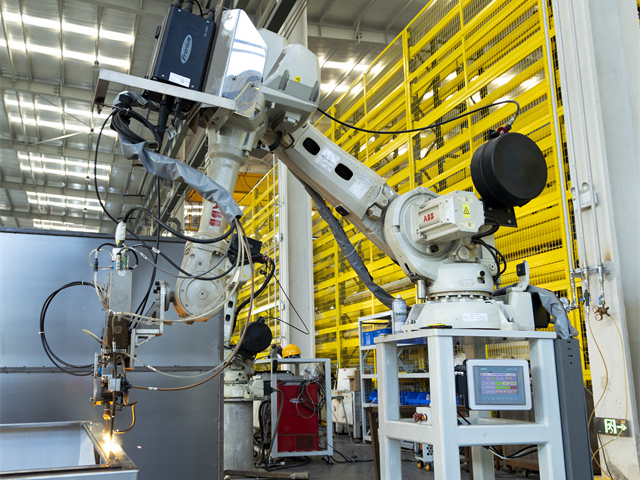
现代化锂电池生产线的工作原理是一个高度集成、精密控制的过程,涉及多个关键环节。电芯卷绕与封装,电芯的卷绕是将涂布好的正负极极片和隔膜按一定顺序卷绕成电芯的过程。这一步骤需要高精度的卷绕机和自动化设备,确保极片间的精确对齐和隔膜的完整包覆。卷绕完成后,电芯被送入封装机进行封装,包括底焊、顶盖焊接等步骤,形成密封的电芯单元。封装过程中需严格控制温度、压力等参数,以防止电芯内部短路或漏液。注液与化成,注液是将电解液注入电芯内部的关键步骤。电解液是锂电池中离子传输的介质,其质量和注入量直接影响电芯的性能和寿命。注液过程需精确控制注液量、速度和温度,确保电解液能够均匀浸润极片并达到比较好的浸润效果。注液完成后,电芯需经过化成工艺,通过充放电循环启动电芯内部化学反应,形成稳定的SEI膜,提高电芯的循环寿命和安全性。
为了提升锂电池的能量密度与安全性,高产生产线引入了智能化的卷绕/叠片与焊接技术。根据电池设计需求,生产线可灵活切换卷绕或叠片工艺,通过高精度机器人操作,实现电芯内部结构的精确构建。焊接环节则采用先进的激光焊接或超声波焊接技术,确保电芯极耳连接牢固可靠,同时减少热影响区,保护电芯内部结构不受损害。智能化的焊接监控系统能实时监测焊接质量,及时发现并处理潜在问题。注液与封口是锂电池生产中的关键环节,直接关系到电池的容量、内阻及安全性。高产锂电池生产线配备了先进的自动化注液系统,能够精确控制电解液的注入量与速度,减少气泡产生,提高电解液分布的均匀性。随后,自动化封口机通过精密的机械结构与先进的密封材料,确保电芯封口处的密封性与强度,有效防止电解液泄露与外部环境影响。这一系列自动化操作不仅提高了生产效率,明显提升了电池的安全性与可靠性。自动化仓储系统提高锂电池库存管理效率。
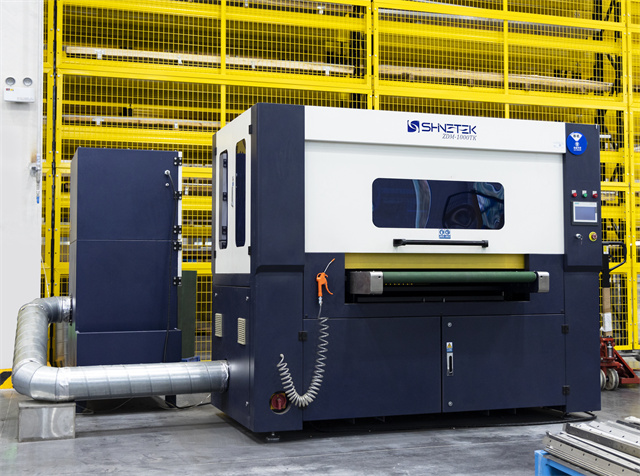
高产锂电池生产线的首要环节是原料准备与混合。在这一阶段,正极材料(如LiCoO2、LiNiO2等)、负极材料(如石墨)、导电剂、粘合剂以及电解液等关键原材料被精心挑选并送入生产线。这些材料在严格控制的温度、湿度环境下进行混合,通过真空搅拌机将活性材料均匀搅拌成浆状。此过程对原料配比、搅拌时间等均有极高要求,以确保浆料的均匀性和稳定性,为后续工序打下坚实基础。混合好的浆料随后进入涂布工序。在这一阶段,浆料被均匀涂布在铜箔或铝箔上,形成正负极极片。涂布过程中需严格控制极片厚度和重量的一致性,以避免对电池性能产生不良影响。涂布完成后,极片进入辊压工序,通过辊压机对极片进行压实,以提高极片的密度和导电性,同时确保极片表面的平整度和强度。锂电池生产线的自动化控制系统能够实现生产过程的监控和调整。上海汽车锂电池生产线求购
锂电池生产线的工艺改进能够提高电池的安全性和环境友好性。锂电池生产线组装线批发
锂电池生产线融入了物联网、大数据等先进技术,实现了生产过程的智能化管理与维护。通过数据采集与分析,管理者可以实时掌握生产线的运行状态、生产效率、设备故障率等关键指标,为决策提供有力支持。同时,智能化的维护系统能够提前进行预测设备故障,安排预防性维护,减少停机时间,提高设备利用率和整体生产效率。锂电池生产线的不断优化与升级,不仅推动了锂电池行业的快速发展,促进了相关产业链的升级与创新。生产线上的技术创新,如新材料的应用、工艺改进等,不断推动锂电池性能的提升和成本的降低,满足了新能源汽车、储能系统等领域对高性能、低成本锂电池的迫切需求。此外,生产线的智能化、绿色化转型,为整个制造业树立了标志,引导了产业升级的新方向。锂电池生产线组装线批发
上一篇: 锂电池装备产品
下一篇: 杭州固态电解质膜成型机产品