沈阳五金车件加工定制厂家
车床件加工是一种常见的机械加工方法,普遍应用于各个行业。它通过车床将工件固定在主轴上,然后通过刀具对工件进行切削、车削、镗削等加工操作,从而得到所需的形状和尺寸。车床件加工具有高效、精度高、适用范围广等优点。车床件加工的工艺流程一般包括工件装夹、刀具选择、切削参数设置、加工操作等步骤。在工件装夹过程中,需要根据工件的形状和尺寸选择合适的夹具,并确保工件的固定牢固。刀具选择是根据工件的材料和加工要求来确定的,不同的刀具可以实现不同的加工效果。切削参数设置包括切削速度、进给量、切削深度等,需要根据工件的材料和加工要求进行合理的选择。加工操作是根据工艺要求进行的,包括车削、镗削、切割等操作。车床件加工通过刀具的选择和切削参数的调整,实现对零件表面的精细加工和光洁度的提高。沈阳五金车件加工定制厂家
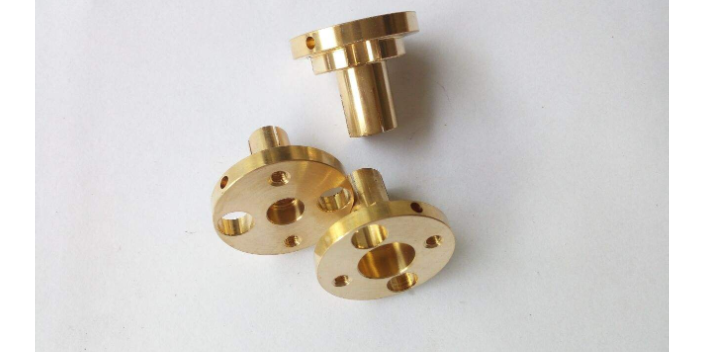
弹簧加工完成后,需要进行测试以确保弹簧的质量和性能。常见的测试方法包括拉伸测试、疲劳测试和硬度测试等。拉伸测试用于测量弹簧的拉伸强度和弹性模量等参数。疲劳测试用于模拟弹簧在长期使用过程中的疲劳寿命。硬度测试用于评估弹簧的硬度和耐磨性。通过测试,可以确保弹簧符合设计要求,并且能够在实际应用中正常工作。弹簧加工普遍应用于各个行业。在汽车行业中,弹簧被用于悬挂系统、刹车系统和座椅调节系统等。在家电行业中,弹簧被用于洗衣机、冰箱和空调等产品中。在电子行业中,弹簧被用于手机、电脑和相机等设备中。此外,弹簧还被应用于医疗设备、航空航天和建筑等领域。弹簧加工的发展和创新,为各个行业提供了更多的应用可能性。沈阳五金车件加工定制厂家车床件加工可以通过刀具的切削速度和进给速度的调整,实现对零件加工时间的控制和生产效率的提高。
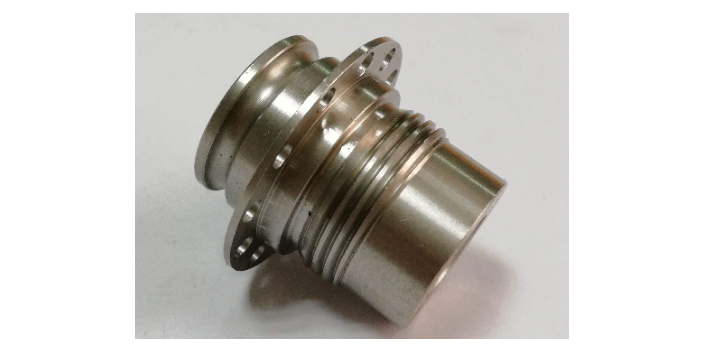
螺钉加工中的质量控制是确保螺钉加工质量的重要环节。在螺钉加工过程中,需要进行严格的尺寸检测、表面质量检查和力学性能测试等。尺寸检测可以使用测量工具如千分尺、游标卡尺等,以确保螺钉的尺寸精度。表面质量检查可以使用目视检查和显微镜等方法,以检查螺钉表面的缺陷和光洁度。力学性能测试可以使用拉伸试验机等设备,以测试螺钉的强度和韧性等性能。随着科技的进步和工艺的改进,螺钉加工技术也在不断发展。目前,越来越多的螺钉加工采用数控机床和自动化生产线,以提高加工效率和精度。同时,新型材料的应用和新工艺的研发也为螺钉加工带来了新的机遇和挑战。未来,螺钉加工将更加注重环保和节能,提高产品质量和可靠性,满足不同行业和领域的需求。
车床件加工的方法有很多,有车削、镗削、切割等。车削是将工件固定在主轴上,然后通过刀具对工件进行旋转切削的方法。镗削是通过刀具在工件内部进行切削的方法,可以得到精度较高的孔。切割是通过刀具对工件进行切割的方法,可以得到所需的形状和尺寸。车床件加工的精度要求较高,一般可以达到0.01mm的精度。这是因为车床件加工是通过刀具对工件进行切削,可以实现较高的加工精度。同时,车床件加工还可以通过刀具的更换和切削参数的调整来实现不同精度的加工要求。车床件加工可以适用于各种材料,包括金属材料、非金属材料等。金属材料包括铁、铜、铝等,非金属材料包括塑料、木材等。不同的材料需要选择不同的刀具和切削参数,以实现满意的加工效果。车床件加工可以使用不同的冷却液和润滑剂,以降低切削温度和延长刀具寿命。
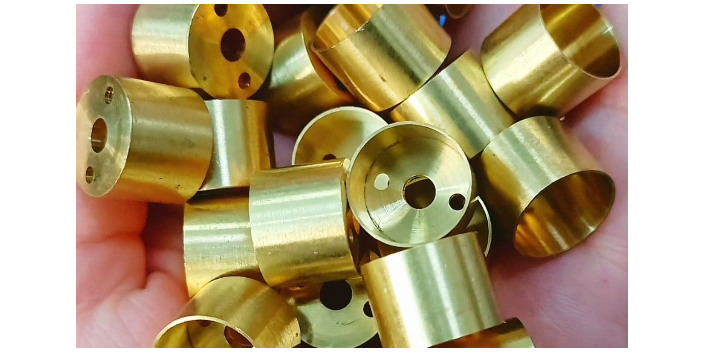
螺栓加工的中心环节是切削加工。切削加工是通过切削工具对螺栓原材料进行切削、车削、铣削等操作,将其加工成螺纹形状。切削加工需要使用的切削工具和设备,如车床、铣床、钻床等。在切削加工过程中,需要控制加工参数,如切削速度、进给量、切削深度等,以确保螺栓的尺寸精度和表面质量。螺栓加工完成后,通常需要进行热处理。热处理是通过加热和冷却的方式改变螺栓的组织结构和性能。常见的热处理方法包括淬火、回火、正火等。热处理可以提高螺栓的强度、硬度和耐磨性,同时改善其内部组织结构,提高螺栓的使用寿命和可靠性。车床件加工可以通过刀具的切削方式,实现对工件内外圆的加工。沈阳五金车件加工定制厂家
车床件加工中的超声波加工技术可以实现对脆性材料的精密加工,避免因切削产生的热变形和损伤。沈阳五金车件加工定制厂家
钻削是一种用于加工孔的加工操作。它通过旋转刀具,利用刀具的运动对工件进行切削,以达到加工孔的尺寸和表面质量的要求。钻削可以分为钻孔和铰孔两种形式。钻孔主要用于加工直径较小的孔,铰孔主要用于加工直径较大的孔。在进行车床件加工时,需要根据工件的要求和加工操作的特点,选择合适的切削工具和加工参数。切削工具的选择要考虑到工件材料、加工形式和加工要求等因素。加工参数的调整要考虑到切削速度、进给速度和切削深度等因素。通过合理选择和调整,可以实现精确的尺寸和表面质量要求。沈阳五金车件加工定制厂家
上一篇: 成都CNC加工车床哪家专业
下一篇: 合肥锁紧螺母